It is readily apparent that in the past decade, any manufacturing processes a company identifies that are not reliant upon technology, yet driven by manual labor, have already shifted production to lower-cost countries. Many companies that sought to capitalize on decreasing their operational costs overseas, and in particular in China, are now experiencing the effects of rising labor-cost pressures, resulting in their search for the next emerging “hot spot” location that can provide low-cost, unskilled labor that is the foundation for traditional manufacturing. Regardless of manufacturing sector, a company must have the necessary skilled workforce available from the start.
An Authoritative Definition
Advanced manufacturing, however, is not dependent on pursuing the lowest-cost environment around the globe. Advanced manufacturing, while lacking an authoritative definition, is more likely to be:
- Capital-intensive utilizing expensive machinery and equipment requiring a low-risk location (when considering natural disaster, economic, political, and social stability)
- Energy-intensive with extremely sensitive equipment highly dependent on a reliable power supply
- Labor-intensive, yet requiring fewer positions, with an increasing demand on higher-skilled labor to execute necessary tasks due to process automation
- Proprietary in nature and based on unique knowledge requiring strong intellectual property laws
As a leader of innovative manufacturing solutions, the United States is well positioned in the global economy to see increased/continued investment and projected related activity for these so-called advanced manufacturing operations — from the revival of the domestic automotive industry through innovative and cutting-edge technologies, to growth in related transportation industries and sectors that have also visibly improved (such as aircraft, trains, and spaceships). Advanced manufacturing techniques are also creating greater efficiencies for the production of everyday consumer goods, such as those in the food and medical industries.
Why is the United States currently well positioned for these projects? With the exception of the U.S. tax climate, other critical location factors typically associated with the key criteria cited above are competitive advantages for the United States when compared with other developed nations. As the leading innovator of new advanced technologies, the U.S. is able to compete on a global scale, even with a relatively high cost of labor; because the application of technology and innovation support advanced levels of production, the volume of labor required is reduced.
In addition to offsetting the high-cost labor market with fewer overall jobs, the U.S. appears to be enjoying a period of abundant energy resources, and offers among the lowest-cost energy for developed countries anywhere in the world. Additionally, the overall risk profile (economic and social stability) of the U.S. is relatively low. There are effective intellectual property laws and a high level of transparency on how business is conducted. Finally, despite an aging infrastructure network, there is still access to highly reliable core utilities, such as water, sewer, telecom, gas, and electric — all important factors when determining where to invest hundreds of millions of dollars or more for a single operation. Yet, an underlying factor remains the access and availability of skilled labor.
The Labor Factor
It has been a common theme to hear about the shortage of skilled labor, despite the relatively high unemployment over the past few years. A typical manufacturing position requires a different profile of employee than in previous generations. Reportedly, more than 27 percent of all manufacturing employees have a bachelor’s degree or higher. The wages of manufacturing jobs continue to rise as well (which may be a reflection of the growth of advanced skills to support the changing manufacturing base) with an average annual manufacturing salary in the U.S. at nearly $60,000.
The continued innovation and technology implications infiltrating and driving manufacturing advancements dictate very specific human interaction and support. The ability to develop and retain talent for these specific projects and industries is imperative to their success. Where other key location criteria can be measured very directly (cost of electricity, state tax structure, risk of natural disasters), the ability to measure the implications of labor is more difficult to attain. No single factor can clearly establish the ability of a location to offer the immediate presence of labor skills. Comparative wage levels may reflect a long tenured workforce in their respective positions rather than the skill level of the labor force. Educational attainment for a location can’t be pegged to a specific industry or labor subset. And there are dozens of other criteria that can be considered, but still not clearly point to the right labor environment for a project.
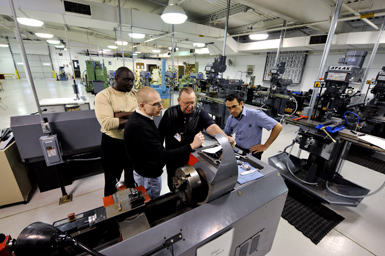
Partnering With Educational Institutions
Regardless of industry or sector of manufacturing, a company must have the necessary skilled workforce available from the start. The best community will have the ability to provide or develop a workforce with the requisite skills, whether it is for a company that manufactures and assembles executive jets or a medical device manufacturer. It is critical that partnerships between the business community and higher education institutions are established.
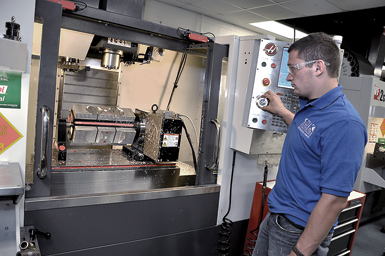
Many states now include grants directly to educational institutions as part of incentive and inducement packages to attract substantial new projects/investment/job creation opportunities. These grants may not directly benefit a company’s bottom line, but establishing the foundation for a sustainable workforce pipeline through partnership with local higher educational institutions is a critical component to the long-term viability of many companies to successfully operate in a particular location. States and communities that are able to demonstrate support for the development of people skills will be best positioned to see continued growth in the advanced manufacturing sector.