A look back at 50 years of economic development evolution begins with the prizes that communities seek. “Fifty years ago it was largely about industrial manufacturing,” says Larry Gigerich, managing director at Ginovus, who has been working in economic development for roughly half of that timespan.
The drive to lure big factories to town was so prevalent that people referred to the practice as “smokestack chasing,” Gigerich observes, adding that communities in the South were particularly known for doing so. “They were looking to get manufacturers that were located in the Mid-Atlantic, the Northeast, or the Midwest. North Carolina was an early pioneer, wanting to grow industry and ensure that people had higher incomes.”
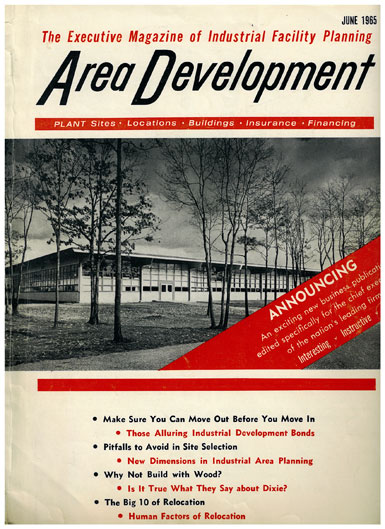
“We’re not a manufacturing economy as much, though some states still are,” agrees Dean Uminski, principal and certified economic developer with Crowe Horwath LLP.
And even in places where manufacturing is still a big part of the mix, times have changed, says Mark Sweeney, senior principal at McCallum Sweeney Consulting. “The manufacturing facility itself has changed so much,” he says. “The ratio of capital to labor is so much higher than it used to be. It’s not unusual to have a million-to-one ratio of investment dollars to jobs. It’s not typically the very large job creator that it was.”
Logistics and Labor
Given the nature of the global economy, logistical considerations often play a greater role in manufacturing site decisions these days, Sweeney adds — “looking at the entire supply chain and seeing it globally.” That often means paying more attention to the proximity of such things as international ports or airports.
And that’s not the only reason for paying more attention to logistics, says Tim Feemster, managing principal with Foremost Quality Logistics. Building efficiencies into the supply chain and getting the most for every transportation dollar is a much more complex science than it was 50 years ago. After all, he says, back in those days, “Most freight was regulated, so it wasn’t nearly as big an impact.” With deregulated air, truck, and rail transportation options, there’s a much greater ability to really squeeze out incredibly significant cost-efficiencies as part of a careful location decision-making process.
Also vastly different today, compared with 50 years ago, are the kinds of skills needed to work at a warehouse or distribution center, Feemster adds. Facilities that once provided a lot of work for lower-skilled laborers now are much more in need of workers with expertise in robotics and computing, he says. “It’s not your father’s warehouse anymore. We have a more sophisticated workforce requirement.”
The idea of offering economic development incentives to sweeten a potential deal is nothing new, but the wild one-upmanship really took off as international automotive manufacturers started seeking locations for massive assembly plants in the ’80s and especially the ’90s
That, of course, is true across virtually all industries, including manufacturing, which also used to need a lot of lower-skilled workers but now requires fewer people, but a whole lot more expertise. “With advanced manufacturing and robotics, we’ve eliminated some of the workers, but it’s highly skilled,” says Uminski, whose economic development experiences have included helping find locations for steel industry facilities.
“Within manufacturing, the overall demand for skills has gone up considerably, and continues to push the envelope,” agrees Sweeney, who is based in the part of the country once known for smokestack chasing. “The South, a long time ago, stopped selling on cheap labor,” he notes.
Evolving Incentives
Another big change through the years has been the relative importance of economic development incentives. Certainly, the idea of offering something to sweeten a potential deal is nothing new, but the wild one-upmanship really took off as international automotive manufacturers started seeking locations for massive assembly plants in the ’80s and especially the ’90s, Sweeney says. Now, it’s hard to imagine a deal without significant incentives of some sort. “Most companies have some level of expectation that incentives will be part of the location decision,” he says.
That said, the makeup of incentive packages has evolved even as the dollar value has increased. “A lot of incentives were used to offset upfront project costs,” Gigerich explains. “Local communities and states have become more sophisticated. Many areas are trying to create pools that are more flexible.” Incentives tied to initial site development have been joined by other kinds of tax breaks and a lot of emphasis on training assistance.
And as incentives have evolved, accountability has grown. More deals include clawback provisions and other measures designed to hold recipients to their end of the bargain, Gigerich says. “Government entities expect companies are going to do what they say they are going to do.”
The manufacturing facility itself has changed so much...the ratio of capital to labor is so much higher than it used to be. It’s not unusual to have a million-to-one ratio of investment dollars to jobs. It’s not typically the very large job creator that it was. Mark Sweeney, Senior Principal, McCallum Sweeney Consulting
Increasing Information
Also evolving dramatically has been the economic development and location selection process itself. “Like everything else, it’s now dominated by information — the demand for information in location decisions,” Sweeney says. “It’s a much more objective, corporate, highly defensible decision, as opposed to an individual’s personal choice.”
“Years ago you didn’t have access to as much information as you do now,” Uminski agrees. And that, he adds, has helped speed up the whole process of choosing a location. “The time has been compressed, from start to finish.”
A process that might have taken 12 to 18 months, or even longer for a massive project, takes only a fraction of the time, Gigerich observes. “In today’s world, if it’s longer than nine months it’s unusual. The industry has grown more sophisticated, and there is so much more information available in today’s world to expedite the process.”
In fact, all of the newer and more easily accessible information resources have helped location professionals whittle down the list of possibilities much further before they ever get in touch with local economic development officials for negotiations. “Now, we’re eliminating lots of locations before you even reach out,” Gigerich says. What was once a long list of initial contacts is often down to just five or seven, “and it’s not unusual to get it down to two or three before starting to engage with local economic development officials.”
Changing Cast of Characters
And finally, the cast of characters has changed as the economic development story has evolved. Fifty years ago, not that many locations had organizations working specifically on economic development matters, but today there are economic development organizations in nearly every jurisdiction, including local municipalities, regions, and every state government, Gigerich observes.
Meanwhile, there are many more consultants too, including quite a few focused just on location and economic development, and many more that are linked to accounting/consulting firms, law firms, and real estate agencies.
“I’ve seen more willingness of economic development organizations to work with site consultants,” Uminski observes. “We’re viewed as allies. I’m not sure that before, they understood the value that we bring to the process, but now that value is more readily accepted.”