How can large employers and state and community leaders work together to put these people back to work, while at the same time attracting industry and investment? One answer may be to invest in education and training programs. In response to various labor issues, many states and large employers are working together to create programs to provide targeted workforce training. Working with educational institutions and industry-specific trade groups, businesses and state governments are attempting to train or re-train groups of workers in order to attract specific industries to their areas. This provides employers with a more knowledgeable, flexible, and transferable workforce, which in turn creates revenue for states.
Some Examples
There is no better example than Georgia’s Quick Start program, which is the oldest program in the U.S. having trained over one million employees in more than 6,500 projects. Georgia’s success is largely due to the very close partnership between the company and the state, and since Georgia has always been in the forefront when it comes to tailoring the training unique to each company’s needs, it continues to be a shining star in a field that is starting to fill quickly with training and other education-focused programs.
Louisiana has created a “Certification for Manufacturing” (C4M) as part of its FastStart training. This one-semester streamlined course prepares students with certification within the field of manufacturing. Upon completion of the program, graduates can interview for open positions or continue their education.
Alabama’s AIDT program is also promoting workforce growth through job training. Through AIDT, Alabama has built multiple training centers across the state in an effort to cluster/organize specific targeted industries. The state is covering all of its bases:
- By sea, AIDT Maritime Training Center assists the maritime industry in the southern region;
- By air, Alabama Aviation Training Center (AATC) provides training for the aerospace industry. Alabama recently invested $7 million for another aviation center at Mobile Aeroplex, which helped Airbus prepare a workforce for its newest aircraft assembly facility.
- By land, various training centers help industries from forest-based and green biomaterials to construction. Additionally, Alabama has equipped 38 Mobile Training Units (MTUs) that are customized for specific company needs, as these units will travel to a company’s location to provide training.
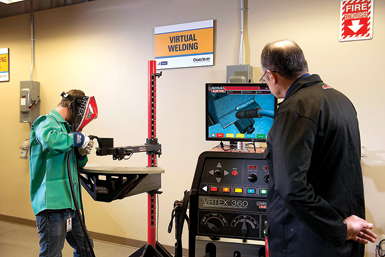
In South Carolina, the ReadySC team is using their “3D Process”: Discovery, Design, and Delivery for training. ReadySC will work with a company to determine the skills required for it to be successful, and will then specifically design a training program to fit its needs, timing, process, and even culture. ReadySC will collaborate with the local technical college and the company to provide training for future employees demonstrating a commitment to the community. Recently, through partnerships with Spartanburg Community College (SCC), manufacturing consortiums, manufacturers, and ReadySC, students enrolled in the advanced manufacturing and industrial technologies programs (such as the “mechatronics” program, which is a blend of mechanical, electrical, computer, hydraulics, pneumatics, robotics, and other manufacturing skills courses) were offered multiple job opportunities, sometimes prior to finishing their programs.
Two-year community or technical college programs offer alternatives to students for whom a four-year bachelor’s education is not financially feasible. One such program gaining recent prominence is the Tennessee Promise, which provides two-year, tuition-free attendance at a community or technical college in Tennessee. The Tennessee Promise program focuses on increasing the number of students attending college in Tennessee by providing students with tuition and fees not normally covered by the Pell grant and the HOPE scholarship. The Promise scholarships may be used at any of Tennessee’s 13 community colleges, 27 colleges of applied technology, or other eligible institutions offering an associate’s degree program. An additional benefit of the Tennessee Promise is that the program also mandates required mentoring meetings, eight hours of community service for each enrolled term, as well as minimum GPA maintenance.
Georgia is also offering $500 per semester to students enrolled and taking classes in one of 10 strategic industries identified by Governor Deal’s High Demand Career Initiative. With an upcoming January 2016 enrollment window, the Strategic Industry Workforce Development Grant program (combined with the use of the HOPE scholarship program) will help students cover the remaining 25 percent of education costs not currently covered by the HOPE program, thereby providing a tuition-free education leading to a new career.
Finally, we can’t forget about traditional training programs that may be just as effective for an existing workforce. Last year, Florida got back in the game with its unified branding of CareerSource Florida. CareerSource is now promoting the FloridaFlex training grant program (which was formerly known as the state’s Quick Response Training program). The 2015-2016 available budget for the FloridaFlex program is $12 million, which will allow awarded companies the ability to use the funds for various reimbursable expenses such as trainers’ salaries, curriculum development, textbooks/manuals, among other costs.
In response to various labor issues, many states and large employers are working together to create programs to provide targeted workforce training. A Culture of Learning
When establishing workforce assistance programs, it is valuable to have a balanced program that allows for industry-specific training, while also providing ongoing training for transferrable skills across similar industries. Having effective training resources to cater to each individual company’s workforce needs is a differentiating factor; however, ensuring that employees are developing skills that can be used across several similar industries should not fall by the wayside. With companies continuing to focus on available skilled workforce and workforce development, communities that take a holistic approach to creating ongoing learning cultures will benefit by being more prepared to face unexpected economic challenges or changes in an area’s targeted industries.
And sometimes a lack of an available workforce creates a learning environment. Training has always been a vital part of any company’s success; by creating a learning culture, a company may be able to establish deep roots in a community. Some companies are shifting away from hiring specific skillsets and focusing on creating an ongoing learning culture based on training to have skills available when necessary.
Take for example a precision device manufacturing company that initially trains its employees on a specific part of the manufacturing process; once the employees’ specific manufacturing position’s skills are mastered, the employee is then trained on the process immediately before and after the one he/she performs. Thus, the company’s employees are capable of filling in if an employee performing the process immediately before or after the one he/she performs is unable to work.
The additional training on other processes has multiple benefits. Not only does additional training benefit the employee (by potentially allowing for overtime hours in other roles), it enables the company to provide a continuity of manufacturing processes to ship a finished product without delays. The additional employee training also benefits the local community by providing a more marketable workforce with more diverse manufacturing skills.