Front Line: Trend Toward Microfactories Continues
By utilizing microfactories, manufacturers can respond quickly to changes in product design and demand.
Q4 2019
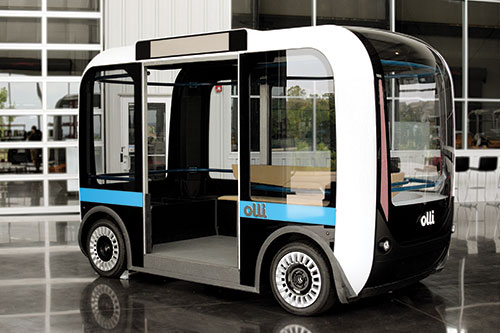
Enabled by digital technology — including 3D printing — microfactories feature modular design and a small footprint, as small as 50 square meters. They can be run by small teams of highly trained workers. Modules can be modified, subtracted or swapped out to adapt to changing market and consumer needs.
The microfactory concept was birthed at the Mechanical Engineer Laboratory (MEL) of Japan in 1990 and has been advanced by research institutes and universities, internationally. To date, perhaps the most high-profile manufacturer to employ microfactories has been General Electric, which opened its first two microfactories in Abu-Dhabi and Dubai, UAE. The Abu-Dhabi factory helps local industrial companies adopt additive manufacturing and design practices. The Dubai facility works with consumer goods and service companies. GE’s partners in the region are Mubadala Development Company, an Abu-Dhabi-based investment and development company, and the Dubai Future Foundation.
Louis Librandi, a principal with Deloitte, says the micro trend has had the most impact in two manufacturing sectors: textiles and electronics. Librandi sees a link with the growing practice of “customized purchasing,” in which consumers can order and purchase clothing or other items which were — at least partially — made to their specifications. Microfactories are well suited for “small-batch production,” Librandi says.
Microfactories are also used in recycling — or reclaiming — rare earth materials from discarded electronic equipment, such as silver, iron, copper, and palladium. Those materials are sometimes found in “conflict zones,” where mining is difficult or extremely expensive, so reclaiming is a viable substitution, adds Librandi. In 2018, The Center for Sustainable Materials Research and Technology (SMaRT Center) at the University of New South Wales (UNSW) in Australia announced the opening of a microfactory that will be dedicated to the recycling of electronic waste. This factory turns recycled plastic waste into 3D printing filaments. A robot can sift through discarded laptop and cell phone components to identify useful elements. A precision, small furnace melts down the parts. Metal alloys can be remade into various parts.
Microfactories are relatively easy to set up and don’t require as much capital as traditional factories. Innovation and Speed to Market
Microfactories are relatively easy to set up and don’t require as much capital as traditional factories. Additionally, manufacturers can respond much more quickly to change in product demand “if they are not constrained by traditional manufacturing overhead and organizational structure,” says Librandi. “Microfactories offer much better opportunities for innovation and speed to market, potentially driving lower costs…A number of OEMs have been looking at how they can incorporate microfactories as part of their supply base and how to manage this new entity. From an OEM standpoint, they need a different skill set to manage that type of supplier and guarantee the quality of the product.”
One of the biggest drivers is being able to serve local markets. In the age of high transportation costs and tariffs, “It’s very beneficial if I don’t have to put products on a ship to spend eight weeks on the ocean,” Librandi says. Further, in the age of Amazon, consumers want to get what they want when they want it; waiting weeks or even months for something they ordered to arrive is a thing of the past. That accelerated delivery trend increases the importance of accelerated supply chains and accelerated design and manufacturing.
For example, Local Motors, an Arizona-based company uses 3D printing to make custom-designed vehicles, calling itself the first digital OEM. They include Strati, the first 3D-printed car, and the Olli, a self-driving bus. The primary material Local Motors uses to make its vehicles is carbon fiber-reinforced thermoplastics. By using ultra-efficient 3D printing, Local Motors can reduce tooling costs by 50 percent and reduce overall production time by 90 percent.
Last year, Local Motors announced the formation of San Francisco-based LM Industries Group, which develops mobility products. LM says it can turn a concept into a finished vehicle within one year.
“LM Industries is on a mission to transform mass manufacturing to micro-manufacturing in order to match the new pace of technology and quickly changing consumer needs,” LM Industries CEO and co-founder John B. Rogers, Jr. said in a statement. Part of that mission is sharing its technology with other manufacturers.
“For an entity or person who is going to start a microfactory, it’s really important to focus on strategy — how they are going to win and what is the value proposition,” Librandi explains. He expects the trend toward smaller, more mobile factories to continue developing.
Project Announcements
Shapeways Holdings Expands Livonia, Michigan, Operations Complex
07/07/2023
Germany-Based Becker Robotic Equipment Plans Canton, Georgia, Manufacturing Complex
12/07/2022
LEGO Group Plans Chesterfield County, Virginia, Manufacturing Plant
06/17/2022
Scotland-Based PowerPhotonic Plans Sahuarita, Arizona, U.S. Headquarters-Production Campus
04/04/2022
A. Duie Pyle Plans Manassas-Richmond-Roanoke, Virginia, Cross Dock Service Centers
03/15/2022
Black Buffalo 3D Corporation Relocates-Plans Smithfield Township, Pennsylvania, Manufacturing Complex
02/07/2022
Most Read
-
20th Annual Area Development Gold and Silver Shovel Awards
Q2 2025
-
In Focus: AI Is Changing Incentives Math
Q2 2025
-
Optimizing Your Rail-Served Transportation Network: Strategy Before Steel
Q2 2025
-
How to Choose the Right Site for Your Factory in 2025’s Volatile Landscape
Q2 2025
-
From Silicon to Server: Mapping the Data Center Supply Chain
Q2 2025
-
Tariffs, Talent, and U.S. Expansion
Q3 2025
-
First Person: David Robey, Co-CEO of QTS Data Centers
Q2 2025