Front Line: Performing Physical Tasks Remotely
Rapid advances in automation are even allowing some tasks in manufacturing facilities to be tackled remotely.
Q2 2022
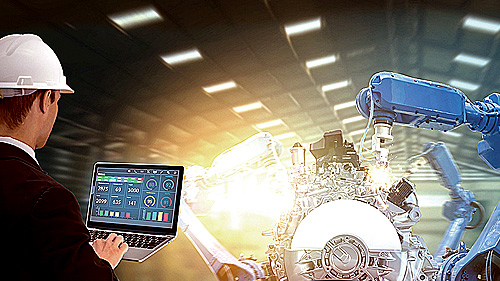
Korean battery-maker LG Energy Solutions is betting large on the future of remote work. It announced it will build a $1.7 billion, fully automated, smart factory in a Phoenix suburb, with remote support, manufacturing intelligence, logistics automation, and more. Full automation is no longer a ”wave of the future.”
As more companies adopt the latest artificial intelligence technology, more employees — whose presence on-site was required by the physical tasks they perform — will be able to work remotely, experts say.
“There is definitely a push toward automation based on what I’ve seen the last couple of years,” says Jacob Everett, a site selection and incentives consultant with Indianapolis-based McGuire Sponsel. Everett says the pandemic “definitely accelerated the pace at which companies are either looking to implement or have implemented automation with the use of robotics. A lot of my clients are trying to automate some physical tasks and move workers into higher-skilled, more knowledge-based roles.”
Making it possible for companies to function, even thrive, with fewer workers is especially crucial in the current tight labor market. Making it possible for companies to function, even thrive, with fewer workers is especially crucial in the current tight labor market, says Graham Immerman, VP of marketing with MachineMetrics, a Northampton, Mass.-based software provider. “We’re operating within the greatest labor shortage in the history of industry. Employers really have no choice but to reduce the burden of non-essential tasks and decision-making through digitization and empower their workforce to do more with less,” says Immerman. “In manufacturing, non-production staff can be as much as 25 to 50 percent of total head count.” By using remote connectivity “theoretically, organizations can enable potential (other) work for these employees.”
Manufacturing Tasks That Can Be Performed Remotely
In a blog post, the San Francisco-based data analytics company Sight Machine listed some on-site manufacturing functions that could be switched to remote, with the help of digital platforms. They include production planners/schedulers; software and process engineers, who would no longer need to rely on on-site observations; and maintenance work-order processors. Accomplishing this kind of major shift requires real-time access to data from the site, Sight Machine VP Sudhir Arni wrote.
Strong, reliable connectivity is essential to enabling any remote workforce. “That information is what enables the effective monitoring of assets and gaining precise insights on process,” Immerman says, and also, “how to leverage remote workers to provide real-time support and expertise.” Strong, reliable connectivity is essential to enabling any remote workforce, he adds, “especially when the goal is to remotely access and visualize real-time data, to allow remote workers to make informed decisions at a moment’s notice, wherever they are.”
One of the greatest drivers of productivity is being able to optimize health and maintenance of production equipment. But with less skilled labor it can be easier said than done. But, when machines go down, connectivity can enable an engineer to remotely access local data from manufacturing equipment. “You can remotely diagnose and even resolve machine issues from anywhere at any time,” Immerman explains.
More remote automation obviously elevates the importance of secure broadband and reliable electricity. “If systems are going to have ‘hiccups,’ the more they automate, the more potential for increased downtime,” Everett says.
As companies rely more on remote operation, how will that impact site selection criteria and processes? “For now, the site selection criteria are relatively similar to what they have been for the past five or 10 years,” Everett says. But it’s possible that less reliance on human capital might enable some companies to operate in some less densely populated areas.
Project Announcements
Shapeways Holdings Expands Livonia, Michigan, Operations Complex
07/07/2023
Germany-Based Becker Robotic Equipment Plans Canton, Georgia, Manufacturing Complex
12/07/2022
LEGO Group Plans Chesterfield County, Virginia, Manufacturing Plant
06/17/2022
Scotland-Based PowerPhotonic Plans Sahuarita, Arizona, U.S. Headquarters-Production Campus
04/04/2022
A. Duie Pyle Plans Manassas-Richmond-Roanoke, Virginia, Cross Dock Service Centers
03/15/2022
Black Buffalo 3D Corporation Relocates-Plans Smithfield Township, Pennsylvania, Manufacturing Complex
02/07/2022
Most Read
-
20th Annual Area Development Gold and Silver Shovel Awards
Q2 2025
-
In Focus: AI Is Changing Incentives Math
Q2 2025
-
Optimizing Your Rail-Served Transportation Network: Strategy Before Steel
Q2 2025
-
How to Choose the Right Site for Your Factory in 2025’s Volatile Landscape
Q2 2025
-
From Silicon to Server: Mapping the Data Center Supply Chain
Q2 2025
-
Tariffs, Talent, and U.S. Expansion
Q3 2025
-
First Person: David Robey, Co-CEO of QTS Data Centers
Q2 2025