Since the beginning of last year, nearly a dozen big-ticket EV battery plant projects involving capital expenditures of more than $1 billion have had ground broken or been announced, with at least two more expected later this year. Cumulatively, Detroit’s Big Three have initiated battery assembly plant projects totaling $17 billion.
Unfortunately, in the near term, most of the components used to make EV batteries at these new battery assembly plants — including lithium battery cells, anodes, cathodes, separators, and battery packs — will be coming from overseas, with more than 90 percent of component production still based in Asia.
The only category of EV battery components with a healthy supply of domestic producers currently are battery management systems (BMS) and thermal management systems (TMS), software systems that ensure safe charging, monitor individual battery cells, regulate temperature, and control demand discharge under a wide range of driving scenarios and atmospheric conditions.
Most of the BMS and TMS systems are still made where they were invented, in the United States, with major suppliers including Leclanché North America in Anderson, IN (BMS); Infinion, San Jose, CA (BMS); Nuvation Energy, Sunnydale, CA (BMS); Dana, Maumee, OH (TMS); VOSS Automotive, Fort Wayne, IN (TMS); and Hanon Systems, Novi, MI (TMS). But as electric-vehicle production ramps up around the world — with General Motors, which was supplanted by Toyota in 2021 as the top selling auto brand in the U.S. (the first time GM has been dethroned as the U.S. sales leader in nearly 90 years), boldly declaring it will cease production of gasoline-powered engines in 2035 — supply-chain shortages may be looming as early as next year for the most critical EV battery components, lithium-ion battery cells.
South Korea-based LG Energy Solution (also known as LG Chem) currently is the largest global supplier of lithium battery cells for EVs, with two lithium cell suppliers in China (CATV and BYD) ranked second and third, respectively. Six of the 10 largest global lithium battery cell producers — and 16 of the top 20 — are in China, three (LG Chem, SK Innovation, and Samsung SDI) are based in South Korea, and one (Panasonic) is based in Japan. But as this is being written, a new contender for the global lithium battery cell production crown is about to enter the ring with these heavyweights.
Tesla Prepares to Put the Pedal to the Metal on Battery Cell Production
Tesla, which partnered with Panasonic to make lithium-ion battery cells at its EV battery gigafactory in Nevada, is busy making contingency plans for an anticipated logjam in global battery cell supplies, which Tesla Founder Elon Musk has predicted will be the auto industry’s next major supply chain crunch after the global semiconductor shortage eases.
Musk’s plan to deal with Tesla’s battery cell supply needs has the boldness we’ve come to expect from a 21st-century Edison who has launched an industry leader in electric vehicles and NASA’s leading producer of space rockets. Tesla is about to become one of the world’s largest producers of lithium battery cells, and it will soon unveil full-scale battery production lines at three of its gigafactories (on three different continents) deploying a new high-energy, lower-cost battery cell design it says is better than anything currently on the market.
Since the beginning of last year, nearly a dozen big-ticket EV battery plant projects involving capital expenditures of more than $1 billion have had ground broken or been announced. Tesla has begun producing its new 4680 series high-energy battery cells this year at what the company calls a “pilot plant” (with about 10 GWh of production capacity) in Fremont, CA. Early next year, Tesla will launch large-scale (100 GWh capacity) battery cell production lines for 4680 batteries at its new Gigafactories in Austin, TX; Berlin; and Shanghai. The three mega-plants also will build battery assembly packs and assemble completed 4680 EV batteries. (With an average EV battery pack currently storing about 60KWh of energy, 100 GWh of production capacity can supply EV batteries for up to 600,000 vehicles per year.)
Tesla’s 4680 battery features a tabless cylindrical cell in a much bigger format than current lithium-ion cells, generating six times more power than the cells the company has been producing in Nevada with Panasonic, with each cell having five times the energy storage capacity of previous designs while significantly reducing the cost of production. Tesla says fully charged 4860 batteries will have a driving range 16 percent longer than EV batteries currently on the market.
Despite a commitment from Panasonic to build 4680 battery cells at a new $700 million plant in Japan, Musk also has been busy this year lining up 4680 production commitments from battery cell suppliers making lithium cells for his EV vehicle competitors. Musk first sounded the alarm about a potential global lithium battery cell crunch in a tweet on Tesla’s “Battery Day” on Sept. 21, 2020, when the company unveiled details about its 4680 batteries: “We intend to increase, not reduce, battery cell purchases from Panasonic, LG, and CATV and possibly other partners, too. However, even with our cell suppliers going at maximum speed, we still foresee significant shortages in 2022 and beyond unless we take action ourselves,” he said.
More recently, Musk has said lithium battery cell demand will not exceed supplies this year due to industry-wide assembly line production output reductions first caused by the pandemic and now due to the global shortage of semiconductors.
The Biden Administration has identified development of a domestic lithium-ion battery supply chain as a strategic goal as well as an imperative in the effort to mitigate the impact of climate change. New rules of origin under the USMCA (which replaced the North American Free Trade Agreement, or NAFTA) will give automakers another strong reason to localize the battery supply chain in North America. In order to qualify for tariff-free trade under the terms of the USMCA, the percentage of “core parts” in a vehicle —including EV batteries, which represent about 40 percent of the value of an EV — that must be produced “locally” (meaning in the U.S., Canada or Mexico) is rising from the NAFTA rate of 62.5 percent to 70–75 percent by the end of next year.
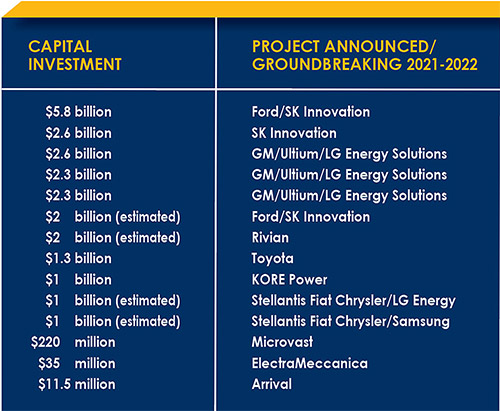
The best news on the domestic EV battery supply chain front, aside from the huge investments in new battery assembly facilities, is that the U.S. automotive industry — backed by a surprising new champion of at least one form of renewable energy — is moving quickly to create a new supply chain for the critical raw materials used to make EV batteries, primarily lithium, nickel, cobalt, manganese, and copper foil. The new raw materials supply chain for EV batteries won’t rely on metals from mines around the world: it will come from recycled EV battery materials collected and separated in new recycling centers that are going up at a rapid clip in the U.S. and Canada.
Australia is the world’s largest producer of raw lithium, extracting 40,000 metric tons of the light, white metal in 2020, followed by Chile (20,600), China (14,000), and Argentina (6,200); most of the world’s cobalt comes from a region in Africa straddling Zambia and Zimbabwe. While there are projects under way to expand relatively small U.S. lithium mines in Nevada and North Carolina (and lithium mines in Newfoundland and Labrador in Canada), and to revive the only known U.S. cobalt deposit at the aptly named Blackbird Mine in Salmon, ID, a new domestic supply chain for recycled EV battery materials is being spearheaded by several new partnerships that aim to create a bevy of recycling centers throughout North America.
Redwood Materials, based in Carson, NV, is building a closed-loop EV battery recycling supply chain for Ford to recycle nickel, cobalt, lithium, and copper. It announced it will build a battery materials manufacturing plant that will produce 100 gigawatts/year of cathode-active materials by 2025 and aims to provide materials to power five million EVs by 2030.
The Biden Administration has identified development of a domestic lithium-ion battery supply chain as a strategic goal as well as an imperative in the effort to mitigate the impact of climate change. Koch Strategic Platforms (KSP), one of six subsidiaries of Koch Industries’ Investments Group, is investing $100 million in Toronto-based Li-Cycle to build new EV battery recycling centers in North America. KSP’s investment in Li-Cycle comes on the heels of a $100 million investment by KSP in zinc-based battery storage maker Eos Energy Enterprises; KSP also is backing next-gen battery cell producer FREYR (based in Norway) and e-mobility company REE Automotive.
Li-Cycle extracts cobalt, nickel, lithium, and other materials from used batteries, defective material or scrap from other manufacturing facilities, then recycles it into usable material. Through a hub-and-spoke model, Li-Cycle’s central recycling facility is in Rochester, NY, with smaller facilities in Ontario. The company is building new recycling centers in Tuscaloosa, AL, and Gilbert, AZ.
Koch Industries’ new enthusiasm for renewable energy in the form of recycled EV battery materials stands in stark contrast to its decades-long opposition to wind energy as an oil and gas conglomerate based in the Kansas. For years, the Koch brothers used their considerable lobbying power to lean on the KS state legislature in opposition to tax credits for wind turbine installations in the Sunflower State. Eventually, market forces took hold and Kansas has now become the state with highest percentage of electricity generated by wind power.
Announcing his company’s new partnership with KSP, Li-Cycle Co-Founder and CEO Ajay Kochhar said that regardless of Koch Industries’ reputation and history, the chance to partner with KSP was a “huge opportunity.” Besides the direct investment, Kochhar said Li-Cycle will benefit from KSP’s operational expertise; Koch also will help Li-Cycle construct, test, and ship modular facilities for future expansions.
Retriev Technologies and Heritage Battery Recycling recently merged their battery management and recycling businesses, creating the largest lithium-ion battery recycler in North America, which will operate under the Retrieve brand.
American Battery Technology Co. is building a $39 million EV battery recycling facility in Fernley, NV, near Reno. ABTC also will build a hazardous waste storage facility at the Tahoe Reno Industrial Center in McCarran, NV, adjacent to Tesla’s battery gigafactory.
The establishment of a domestic, sustainable supply chain for EV battery raw materials is seen as an essential first step in reshoring — or, more accurately in this case, building from scratch — a start-to-finish domestic supply chain for EV battery components. However, the conventional wisdom about EV raw materials may soon by upended by a technological breakthrough from — you guessed it, Tesla — which reportedly is developing lithium-sulfur cathodes that will eliminate the need for metals including cobalt and nickel, while greatly increasing the energy storage capacity of batteries.
Battery Assembly in U.S.
Since the beginning of last year, just about every month has been punctuated with the announcement of a major new battery assembly facility in the U.S., with a crescendo of new projects in the second half of the year. Most of the deals have involved partnerships with leading global battery cell producers, including LG Chem and SK Innovation, both of South Korea, which along with Samsung, Panasonic, and China’s CATL (the world’s largest producer of lithium-ion battery cells) form the top tier of lithium cell makers.
In twin announcements in September, Ford made an $11.4 billion commitment with battery partner SK Innovation to build what the automaker called a “vertically integrated ecosystem” for electric vehicles and EV batteries at new facilities in Tennessee and central Kentucky. Ford will build a $5.6 billion, 3,600-acre mega-campus called Blue Oval City in Stanton, TN, that will include a new assembly plant for electric F-Series pickup trucks, a BlueOvalSK battery plant, and a recycling center. Ford says the campus will “reimagine how vehicles and batteries are made,” creating 6,000 new jobs. SK Innovation also is building a new $2.6 billion EV battery assembly plant in Commerce, GA, in Jackson County to supply other automakers.
Ford simultaneously announced that Glendale, KY, in Hardin County will be the site of a new $5.8 billion BlueOvalSK Battery Park featuring two new battery assembly plants that will supply Ford’s North American vehicle assembly plants with locally assembled batteries that will power next-generation electric Ford and Lincoln vehicles, also creating 6,000 new jobs. Ford says that its global EV plan will require at least 240 GWh of battery cell capacity by 2030. Ford has pledged that the new plants in KY and TN will be designed to be carbon-neutral with zero waste to landfill once fully operational in 2026.
The establishment of a domestic, sustainable supply chain for EV battery raw materials is seen as an essential first step in…building from scratch a start-to-finish domestic supply chain for EV battery components. General Motors’ EV battery assembly joint venture with LG Chem, known as Ultium, announced in 2021 that it will build three new EV battery assembly pants: a $2.3 billion facility in Lordstown, OH; a $2.3 billion plant in Spring Hill, TN; and a $2.6 billion plant in Lansing, MI.
Stellantis Fiat Chrysler is planning to build two EV battery assembly plants, one partnering with LG Chem and the other partnering with Samsung, at sites to be announced later this year. According to reports, Toyota North America is planning a new U.S. battery assembly facility in a partnership with Tsusho America.
Despite all of the new U.S. battery assembly plants in the pipeline — and regardless of how big a splash Tesla makes with its full production lines for lithium battery cells — the overall global balance of power in the EV battery supply chain is not expected to shift dramatically between now and 2030. EV industry analysts projected last year that lithium battery production capacity in Asia will increase to 1,624 GWh by 2030, more than seven times larger than the projected EV battery capacity in North America.