Driving Into An Electric Vehicle Future
The transition to EVs will bring mega investments and thousands of jobs to some communities while disrupting makers of ICE vehicles, the communities in which they’re located, as well as their employees.
Q1 2022
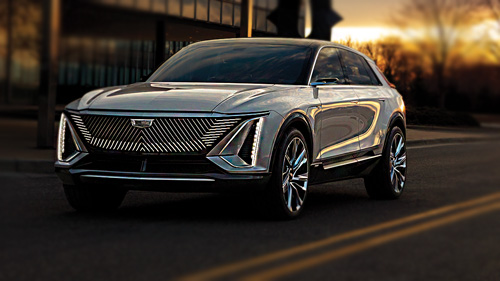
Don’t forget that disruptive technologies are, well, disruptive. One person’s opportunity, one community’s economic development win, quite often means disruption for someone else’s livelihood and some other community’s economy. The story is only starting to unfold, but the transition to electric vehicles, or EVs, is shaping up to be the automotive industry’s most important story going forward.
Powering Up the Changes
“Some traditional automotive companies — particularly parts companies dedicated to the internal combustion engine — if they don’t change they aren’t going to survive the EV transition,” according to Dennis Cuneo, who owns DC Strategic Advisors and has years of background as an automotive industry executive, including with Toyota. “Companies that produce engines, engine parts, gas tanks, exhaust systems — those products are eventually going to be phased out. And so will the plants in communities that make them, unless they are transformed into something else.”
“If you are making headliners, sunroofs, and certain interior components, you might be largely unaffected,” agrees Bernard Swiecki, director of research at the Center for Automotive Research in Ann Arbor, Michigan, and director of its Automotive Communities Partnership. “But if you are making powertrain components or fuel tanks, that’s going to impact your bottom line.”
Meanwhile, Cuneo says, there’s a world of opportunity out there for companies and communities that are riding EVs into the future. For “plants that make battery packs and motors, inverters, chargers, there will be a lot of opportunities there, a lot of new plants and parts to be made,” he notes.
East Asia is presently the dominant location for production of lithium-ion batteries, or LIBs, used in a lot of consumer electronics and increasingly used to power EVs, according to Alexandra Segers, general manager of Tochi Advisors LLC. “Currently, China, Japan, and Korea collectively host over 80 percent of all LIB cell and automotive LIB cell manufacturing capacity,” she says. Production experience and well-developed supply chains may keep it that way for a good while.
“However, other regions, including North America, are getting more competitive in the growing automotive LIB cell market,” she says. Indeed, one recent U.S. Department of Energy report cited more than a dozen new U.S. battery cell manufacturing operations that could be operational within the next few years.
“Most U.S. cell and battery plants are relatively new, but several are owned by companies which have experience in battery manufacturing,” Segers says. “Almost all U.S.-based LIB manufacturing is targeted to serve the domestic new upcoming EV market.”
Battery plants are more likely to spring up as new factories rather than retrofits of existing operations, Swiecki points out. “There is not an existing part of the industry that can be transitioned. You used to make spark plugs and now you’ll make batteries? It really doesn’t work that way.” On the other hand, “there are engine plants adding electric motor production to their product portfolios.”
One community’s economic-development win quite often means disruption for someone else’s livelihood and some other community’s economy. Locations Old and New
Some regions where EVs are on the rise already have a significant automotive history, while some regions are relatively new to auto-related manufacturing. Tesla is an EV player working in both situations. Cuneo points to Tesla’s “Gigafactory” in Nevada — it’s a $6 billion investment worth about 7,000 jobs, making EV batteries in a state that has not traditionally been an automotive powerhouse.
On the other hand, Tesla’s assembly plant in Fremont, California, employs some 10,000 people at a facility that opened back in the 1960s to make General Motors vehicles, then became the GM/Toyota New United Motor Manufacturing Inc. operation in the 1980s. Texas has been in the automotive business for decades, first with GM in Arlington, then Toyota in San Antonio, and now Tesla is making a big splash in Austin.
Or consider Lordstown, Ohio. GM has a long history there, too, making everything from sedans and vans to the Pontiac Firebird. GM sold its assembly facility there to entrepreneurs who have a dream of building EVs — a difficult dream not yet fulfilled, though the latest news is that there could be action on the assembly lines there yet this year. In the meantime, though, it’s reported that construction of the GM and LG Energy Solutions plant in Lordstown, which will house an Ultium Cells battery plant worth more than $2 billion and 1,100 jobs, is well under way.
GM is investing billions in other places, as well. Its broad plans include battery plants in Michigan and Tennessee. The company also picked its Spring Hill plant in Tennessee as a site for EV manufacturing, including the luxury Cadillac Lyriq. And among other developments, GM has announced upgrades at an existing plant near Detroit that has been making the electric Chevy Bolt and will be configured to turn out electric pickup trucks by 2024.
Then, of course, comes the huge Ford announcement last September of its BlueOval City complex in western Tennessee that will turn out electric F-series pickups along with advanced batteries. A BlueOval SK Battery Park development in central Kentucky will add battery production to power Ford and Lincoln EVs. Altogether, Ford and its partner, SK Innovations, are investing more than $11 billion in the Tennessee and Kentucky operations.
Beyond the GM and Ford activity in Tennessee, the state’s EV business includes Nissan’s Smyrna operation. In 2012, Nissan started battery production there, and the next year began producing its Leaf EV in Tennessee. And three years ago, Volkswagen announced that Chattanooga would be its North American site for making EVs, and it’s also bringing EV engineering to Chattanooga.
Battery plants are more likely to spring up as new factories rather than retrofits of existing operations. Georgia is also among the places poised to win in the EV future. SK Innovation’s portfolio includes two battery plants in a state that gained its first major automotive assembly plant, Kia, a bit over a decade ago. And Georgia’s biggest recent announcement came from Rivian Automotive, which is planning a $5 billion, 7,500-employee battery and electric truck assembly plant in the Atlanta area. Segers notes that Rivian picked a former Mitsubishi facility in Normal, Illinois, for its first manufacturing plant, and now has planted its flag in the right-to-work Southeast.
Arizona, meanwhile, has not traditionally had automotive manufacturing, says Cuneo. But now is home to the Lucid EV plant, the Nikola commercial EV operations, and Canada-based ElectraMeccanica.
If those last few automakers mentioned above seem like something less than household names, get used to it, Swiecki says. The EV business is full of new entrants, including some from parts of the world that haven’t typically sold cars here before. “VinFast, a Vietnamese company, is planning to start selling their vehicles here in the United States,” he cites as an example. “They are talking about a U.S. plant. In conventional vehicles you’d have a much harder time for a brand-new company from Vietnam to come over and set up shop in the U.S. making vehicles. The EV world makes that possible.”
EV Developments All Over
Needless to say, the transition to EV production is happening all over the map, though the same can be said for the way traditional gas-powered vehicle production shifted from its original clusters. “Traditional automotive production locations have been significantly splintered over the last 30 years or so,” says Peter Wells, director of the Centre for Automotive Industry Research at Cardiff University in Wales. “In the U.S., the arrival of the original ‘transplants’ from Japan marked the start of a shift away from Detroit to nontraditional locations.”
Similar splintering changed the automotive map in Europe, he says. “The creation of the enlarged EU facilitated a peripheralization of much of the supply industry seeking low-cost locations, again accentuated by the investment in assembly by VW Group and others into these locations.”
“In general, the auto production base right now is quite distributed, and I would expect the electrified part of it to also be distributed,” adds Swiecki. “There will be a tendency to try to locate the battery plants within a reasonable shipping range of assembly plants,” he says — not necessarily adjacent, but not a world away, either.
“Battery packs are heavy and difficult to transport,” Wells agrees. “In an ideal world, these would not be far from the point of final assembly. This basic issue is evident in much of the current wave of investment in battery manufacturing, especially in the European Union, where the vehicle manufacturers are mostly focused on converting existing plants to an EV focus.”
Segers adds that these plants have a significant demand for power and water, so utility supply and cost are high on the list of location considerations, along with availability of skilled labor. And companies tend to be in a hurry to get up and running, she says. “Project schedules are nowadays much faster than a couple years ago. Companies want to start construction soon after finding a site location and are looking for fast-track permitting and pro-business state conditions.”
The EV business is full of new entrants, including some from parts of the world that haven’t typically sold cars here before. A Bumpy Transition
The internal combustion engine has powered the vast majority of vehicles for well over a century. It’s hardly surprising that the transition to EVs will be incredibly disruptive, but the jury is still out on how speedy that transition will be. Segers notes that major automakers have announced ambitious timetables for the transition. GM, for example, expects to be largely electric by 2035, she says, BMW at least half electric by then, and Volvo could be fully electric even a few years earlier.
Challenges lie ahead no matter how fast the EV evolution happens. On one hand, a relatively fast transition would be earth-shattering, requiring explosive developments in charging infrastructure and manufacturing alike. On the other hand, a slow transition just drags out the logistical and financial challenges facing the industry.
“Right now, a lot of the industry is basically supplying two different product lineups,” Swiecki points out. “As you transition your company, you’re going to continue making decreasing volumes of what goes into conventional vehicles, while simultaneously ramping up electric vehicles.”
And that’s a significant challenge for a comparative low-margin business, he says. As companies phase out production of traditional vehicles and the parts that are needed for internal combustion vehicles, “you’re losing economies of scale, but at the same time EVs are not getting economies of scale yet. This is a business where scale is the lifeblood.”
A possible solution is diversification, he says — finding ways to share parts and components between more kinds of electric vehicles. “We’re seeing sharing of EV platforms between passenger cars, midsize trucks, full-size trucks. Some of the suppliers are also electrifying agricultural equipment,” Swiecki says. “All of those things are attempts at gaining scale. It’s also risk distribution. If you can serve multiple customers and product sectors simultaneously, you decrease your exposure to a problem in any one area at one time.”
“One key new development that is worth a look is the co-location of battery disassembly and battery assembly,” Wells says. “I think probably VW Group is furthest advanced on this, with a pilot facility in Germany designed to form the basis of mass disassembly in the future — thereby closing the materials loop for the next generation of batteries.”
The transition to EVs will certainly bring challenges and disruptions, but it’s real and here to stay, says Segers, and the investments will be eye-popping in both dollars and job numbers. “The investment is much higher compared to a standard assembly plant,” she notes, but “we will see many more of those announcements. This is the new era of the automotive industry. All automakers are committed to electrifying their vehicle lineup.”
Project Announcements
Sumitomo Electric Wiring Systems Plans Simpson County, Kentucky, Manufacturing Operations
07/10/2025
TMG & Haartz Solutions Plans Bostic, North Carolina, Manufacturing Operations
07/02/2025
Torc Robotics Plans Ann Arbor, Michigan, Engineering Operations
06/27/2025
Commercial Specialty Truck Holdings Expands Cynthiana, Kentucky, Operations
06/17/2025
General Motors Expands Tonawanda, New York, Production Operations
06/05/2025
Daimler Truck Financial Services USA Plans Charlotte, North Carolina, Headquarters Operations
05/29/2025
Most Read
-
20th Annual Area Development Gold and Silver Shovel Awards
Q2 2025
-
In Focus: AI Is Changing Incentives Math
Q2 2025
-
Optimizing Your Rail-Served Transportation Network: Strategy Before Steel
Q2 2025
-
How to Choose the Right Site for Your Factory in 2025’s Volatile Landscape
Q2 2025
-
From Silicon to Server: Mapping the Data Center Supply Chain
Q2 2025
-
Tariffs, Talent, and U.S. Expansion
Q3 2025
-
First Person: David Robey, Co-CEO of QTS Data Centers
Q2 2025