Optimizing Market Share in the EV Industry
With huge growth expected in the EV/battery production market, manufacturers must start their project planning early, taking into account labor, energy, and supply chain needs.
Q1 2022
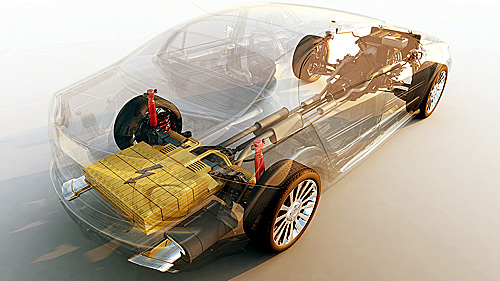
Putting that data in terms of U.S. dollars, Statista.com further asserts, “Between 2020 and 2026, the size of the global electric vehicle market is expected to increase over fourfold to reach an estimated global market size of some US$725 billion by 2026.”
For EV manufacturers, these growth projections convert to more facilities, increased manpower, and strained supply chains to ultimately produce more vehicles for distribution. At the same time, the EV battery market is also projecting significant growth. According to Business Wire, “The global EV batteries market is expected to grow from $22.99 billion in 2021 to $38.32 billion in 2025.”
The major factors driving the EV battery market include decreasing battery prices, increasing investment by leading automotive OEMs to secure the battery supply chain for their future electric vehicles, and increasing adoption of EVs worldwide.
This rate of growth means EV industry manufacturing leaders are racing to capture market share. In order to optimize their competitive edge, leaders need to effectively plan their facilities to avoid costly pitfalls and achieve success. Here are key considerations.
Site Selection
Greenfield vs. Brownfield — The first consideration for many new manufacturing facilities is determining whether to select a greenfield or brownfield site, and that includes examining the schedule and cost deltas between the two among other factors. Battery production plants are almost exclusively greenfield sites, while electric vehicle OEMs are more likely to consider brownfield sites, which may have initially been designed for production processes similar to those intended for the plant in question.
Thus far, direct foreign investors have been most likely to consider brownfield sites, using operational strategies such as knock-down kitting, micro-factory, and other efficiency strategies to optimize costs and speed to market. Operational target dates set by international startup investors also play a role in brownfield vs. greenfield considerations, as the “race to market” factor takes hold.
Yet, owners may have very limited options other than to consider a greenfield, as the supply of available existing facilities with 300,000+ square feet is very limited. A greenfield provides an owner the ability to fully customize their facility to their process and offers geographic flexibility (you can build it “anywhere”); existing facilities are where they are.
Additional factors weigh into the greenfield vs. brownfield decisions in addition to the costs of developing local infrastructure and access to utilities. With a greenfield site, owners must consider flood plains and environmental concerns specific to an area, such as endangered species, potential for natural disasters, and soil conditions that impact the building’s foundation. For brownfield sites, the focus is on suitability and adaptability of the existing facility, including the size and layout, what modifications will be required to adapt it to the new owner’s processes, whether the site is code compliant for the new process and, if not, whether the required upgrades are prohibitive.
Statista.com asserts the size of the global electric vehicle market is expected to reach an estimated US$725 billion by 2026. In one example, a major overhaul of MEP (mechanical, electrical, and plumbing) infrastructure was so expensive and time-consuming that it negated the schedule advantage of buying an existing facility over building new. This example illustrates a general market trend. Generally speaking, major MEP equipment is back ordered to such an extent that owners can practically build a new facility before such equipment is able to be delivered. So if overall costs are similar between new construction and retrofit of existing, but there’s no longer schedule advantage of buying existing, why even do it?
Location — Location is a key factor. Battery producers need to be reasonably proximate to their clients, which may include more than one OEM. Sourcing of raw materials is also critical. Because raw material supply chains for the EV industry are emerging simultaneously with production processes, the raw material factor is dynamic. Business and tax incentives offered by the state also factor into the location equation.
However, perhaps the most significant factor today on where EV manufacturing companies choose to locate plants is the available labor market. If there is a competing facility that draws local labor and talent, there may not be the workforce volume for another in the same area.
Utilities + Energy — Convenient access to utilities is always important but battery cell manufacturers specifically have above-average needs for water and electricity. Sites with access to aquifers or an opportunity to drill new wells offer the potential for substantial operational savings.
In terms of energy, availability is one variable of the equation but lead times to get the energy to the site can prove to be a surprisingly challenging factor. Large utility providers across the country are seeing longer lead times to get major equipment onto sites. Even something as simple as high-voltage cabling to run a new line to a site has longer lead times than ever before, often highlighting such a component as a critical path item.
For EV and battery manufacturers, energy availability becomes even more challenging when large percentages of the energy must come from renewable sources. Battery/EV producers often have corporate social responsibility initiatives that revolve around providing a green product and producing it ethically and sustainably. Potential customers will want to know how much of their energy used in the plant comes from renewable sources. Carbon footprint reduction strategies are prevalent in the operating philosophy and public relations messaging for both battery projects and EV OEMs.
The most significant factor today on where EV manufacturing companies choose to locate plants is the available labor market. Indeed, carbon footprint reduction strategies are becoming so important that some owners are willing to prioritize them at any cost. Carbon footprint strategies are such a key consideration from the very beginning of projects that large utilities have created or enhanced internal consultancy/advisory departments to support the carbon footprint strategy needs of these new investors, and state economic development agencies have increased the percentage of renewable sources to attract major investors to their states. State regulated (or unregulated) utilities have become a fundamental consideration for site selection.
Supply Chain
Most major components/inputs of the EV and battery total supply chain are emerging simultaneously across the globe to meet OEM production targets, and those in the A/E/C industry are vying to get involved with nearly every component of the supply chain: EV production facilities, lithium recycling facilities, battery cell production facilities, and raw material processing.
Market Forces + Contract Dynamics — These market forces are driving a significant amount of JV (joint venture) strategy between OEMs and suppliers, both foreign and domestic. Direct supply chain contracting is also very dynamic. To meet these challenges, the supply chain itself will need to expand at the same rate as the EV/battery markets, with investments in raw materials, metals, refining, and cathode production.
To ensure availability amidst this combination of interrelated factors, many OEMs are bringing production of batteries and semiconductors in-house. Some companies are venturing even further up and down the supply chain, internalizing metals processing and refining, and are now considering controlling even the raw material.
On the back end, industry leaders are considering recycling issues as numerous companies are making significant investments in battery recycling facilities. Recycling factors into the geographical aspect of site selection because, although battery production is localized, batteries are recycled all over the U.S., so consolidating recycling operations through a reasonable methodology can be a challenge. The supply chain to support all this doesn’t exist right now, and there are opportunities to streamline the supply chain as it grows to support demand.
Tier 1 Targets — Production dates are primary drivers of Tier 1 companies. Individual OEMs have a brief history of setting contracts with specific battery producers. In the past, companies contracted for batteries without any contingencies but are now taking a more permanent ownership role in their own battery supply, with co-located suppliers and battery production as part of an EV assembly campus.
Tier 2 to Tier 3: Battery Cell Producer to Battery Materials — Tiers 2 and 3 are comprised of battery cell and battery material producers. Anecdotally, there has been a broad market assumption that raw materials will be available to produce enough batteries to match EV production, but this assumption has yet to be proven true. As a result, many industry insiders are predicting a wave of battery material projects, some with large capital expenditures. The typical project size for battery production and materials projects can exceed 1,000,000 square feet and cost from $500 million to more than $1 billion. This includes everything from various electrolyte blended cathode/anode chemical products to battery grade graphite and nickel, all of which must emerge to support the EV supply chain.
For EV and battery manufacturers, energy availability becomes even more challenging when large percentages of the energy must come from renewable sources. Insight
Start Early — Starting early with site selection and project planning is the only way to meet aggressive market demand. This is especially true at present, with historic constraints in not only the supply chain but also the construction industry. Lead times have now doubled and tripled, even for items that were widely available in the relatively recent past. The critical path is the availability of materials (or lack thereof) as OEMs and battery cell producers engage in a race to market.
Advance planning and coordination is vital. Because of the broader scope of energy use, especially in battery cell production and battery materials projects, advance planning is essential as the industry targets the electrification of the North American auto market.
Energy suppliers that have been regionally focused are now creating nationwide coalitions to support EV infrastructure. Raw materials suppliers are realizing that there is no reason to compete with others because the demand is so high that there is more than enough work for everyone. Even in the construction/design industry, firms that were formerly competitors are teaming up to work together on massive projects that no one firm can support alone. One of the surprising silver linings of the supply chain crunch is that the demands are generating foreign direct investment into the U.S. as European and Asian companies are expanding into North America to meet supply chain needs. Because many of these companies are already at the Tier 2/Tier 3 level, with established project and process definition, they bring a wealth of insight to streamlining production that startups would take years to internally develop. While there have been some logistical challenges resulting from the demand for electric vehicles and the support systems to make them broadly available, there have been lessons learned, process and planning improvements, and positive growth to meet market demand that will change the way the industry does business today and for years to come.
Project Announcements
Mutares Plans Auburn Hills, Michigan, Manufacturing Operations
08/01/2025
British-Based McLaren Plans Baltimore, Maryland, Vehicle Processing Operations
08/01/2025
Adient Plans Normal, Illinois, Production Operations
07/29/2025
Sumitomo Electric Wiring Systems Plans Simpson County, Kentucky, Manufacturing Operations
07/10/2025
TMG & Haartz Solutions Plans Bostic, North Carolina, Manufacturing Operations
07/02/2025
Torc Robotics Plans Ann Arbor, Michigan, Engineering Operations
06/27/2025
Most Read
-
What We’re Getting Wrong About Gen Z’s Future in the Skilled Trades
Q3 2025
-
A New Course for U.S. Shipbuilding
Q3 2025
-
Optimizing Your Rail-Served Transportation Network: Strategy Before Steel
Q2 2025
-
In Focus: AI Is Changing Incentives Math
Q2 2025
-
How to Choose the Right Site for Your Factory in 2025’s Volatile Landscape
Q2 2025
-
Reshoring Reality Check from Construction
Q3 2025
-
The New Math Behind Mexico and U.S. Manufacturing Decisions
Q2 2025