Strategies for Accelerating Project Execution
Pandemic-related project delays have prompted manufacturers to investigate alternative project-delivery approaches to make up for lost time.
Q1 2021
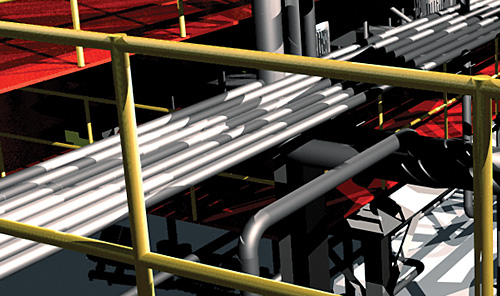
Prior to the pandemic many manufacturing companies had design and construction projects, either in progress or in the pipeline, with aggressive schedules. To slow the spread of the disease, many manufacturing operations and construction sites were shut down while new safety precautions were developed and implemented. Furthermore, uncertainty in the market caused many companies to delay committing large capital investments into expanding their operations.
Over the summer, the manufacturing industry has slowly begun its return to pre-pandemic production levels. As this occurs, companies have done little to relax pre-COVID targets for newly constructed facilities, as projected production dates are a key driver for the majority of manufacturers, especially for advanced technology markets like electric vehicles where speed to market is such an important factor. This has resulted in compressed design and construction schedules and a need for the architecture/engineering/construction (A/E/C) industry to offer unique ways to accelerate project delivery.
Following are insights into strategies, solutions, and key considerations which can be implemented to accelerate project execution and help companies get back on track.
Consider Alternative Project Delivery Methods
Historically, many manufacturing leaders have preferred the traditional design/bid/build model. This delivery method takes a linear, step-by-consecutive-step approach, first bringing an A/E on board to design a complete package of construction documents. Once design is complete, project execution goes on hold as the construction documents are bid out to contractors. This bid process can take a considerable amount of time, dependent on the level of detail an owner puts into reviewing, evaluating, and eventually awarding a contractor.
Each of the alternative project delivery methods requires the owner to relinquish some portion of control over to the design/construction team in order to accelerate the schedule. Although this process has the least amount of risk to the owner, its step-by-step approach makes it the longest in terms of schedule duration. Instead, consider a design/build approach where the A/E and the contractor are simultaneously brought on board at the beginning of a project. Not only does this delivery method facilitate a more expedited constructability review process, it can substantially compress the overall project schedule by omitting the bid delay between the design and construction phases.
An alternative project delivery method, similar to the design/build approach, is EPCM (engineering, procurement, construction, management). This “single source” approach, where a sole firm acts as designer, contractor, and owner of all vendor contracts, has been used extensively throughout the oil, gas, and petrochemical industries where projects are inherently complex and require extensive coordination. In a situation where it is imperative to meet an aggressive production date, an EPCM approach may prove beneficial, as having all project vendors leveraging their expertise under a single contract can reduce construction change orders and result in significant schedule reductions.
One of the more progressive delivery methods from a procurement perspective is integrated project delivery (IPD). In this approach, the owner, design firm, and contractor are all bound by a joint agreement and, if well executed, all parties share the financial incentives of a project being completed ahead of schedule and below budget. Although this delivery method may come with an owner’s perceived loss of control, this extremely collaborative delivery method has resulted in projects completed with drastically reduced schedule and cost.
It is important to understand the impact of schedule compression strategies on the overall project lifecycle. Similar to design/build and EPCM, IPD invites key subcontractors to be part of the design process. This allows owner requirements and design intent to be communicated early to trades who can, in turn, provide constructability feedback in real time during the planning phase when its impact is most beneficial. This early collaboration between owner, A/E, and contractor can have a significant impact on reducing construction costs and compressing project schedules.
Implement “Pull Ahead’ Approach
Each of the above alternative project delivery methods requires the owner to relinquish some portion of control over to the design/construction team in order to accelerate the schedule. However, some manufacturing organizations have very stringent procurement protocols that do not allow this perceived loss of control over the competitive bid process.
If that is the case, projects can be broken into smaller, defined scopes of work based on critical path activities. These “pull ahead” packages can enable an owner requiring the design/bid/build delivery method to start construction activities before the bulk of design is complete, allowing for the project to be completed at a more accelerated pace than the traditional design/bid/build approach.
For example, take a greenfield manufacturing facility. By designing and awarding an early civil/sitework package, construction can begin while the structural steel and foundation design development is under way. As soon as key mechanical and/or electrical equipment requirements are known, a long-lead equipment package can be released for pre-purchase. The building shell can then be designed and bid, typically followed by the mechanical, electrical, and plumbing (MEP) package to be released last. This process allows construction to start early and gives more time for the engineering details to be refined without impacting the overall construction schedule.
By breaking the project up into smaller packages that are released sequentially and in alignment with the construction schedule, stakeholders can achieve the benefits of an accelerated schedule, while maintaining owner-required competitive procurement protocols. This does require a more robust level of construction management staff and may necessitate additional resources for manufacturers that do not have a U.S.-based facilities team.
Determine Level of Design Detail
Under a traditional design/bid/build approach, construction documents and 3D models are developed to a sufficient level of detail to support the contractor bid process. Once a contractor is awarded, select trades must further develop the design to a fabrication level of detail based on the design intent provided within the construction documents.
Owners should ensure those responsible for making schedule compression decisions consider recommendations from both the design and construction industry experts. For example, many engineering firms will produce steel design drawings that require shop drawings, and a subsequent lengthy shop drawing approval process (e.g., exact dimensions and details of bolt hole locations) before the steel can be ordered and fabricated. This step inherently comes with over-production and extra processing — both of which are forms of waste as defined by Lean methodology.
Owners are encouraged to investigate the 3D modeling capabilities of potential A/E’s before selecting a design team, as some firms have the ability to design to the fabrication level of detail, potentially avoiding the waste of redundant design effort. Involving an A/E that can produce fabrication-level designs in-house shortens the schedule by eliminating this added step, and on large-scale manufacturing projects, this approach can significantly reduce the construction schedule by enabling steel to be ordered months sooner than traditional methods.
Understand Impact of Schedule Compression Strategies
It is important to understand the impact of schedule compression strategies on the overall project lifecycle, and keep in mind that design hours and construction hours do not always translate directly as a one-to-one time savings. An emphasis in decisive planning during the design process can translate into substantial construction time and cost savings. Just like swimming one mile can provide an equivalent workout and calorie burn as seven miles running, a one-day increase in the planning/design phase might result in a 15-day savings to the construction schedule based on the increase in coordination it can provide. Spending additional time up front during the planning and design phases can result in substantial time and money savings during construction execution. Owners should ensure those responsible for making schedule compression decisions consider recommendations from both the design and construction industry experts.
When conducting project interviews, consider whether team members have the right “chemistry” to work collaboratively. Remember Design and Construction Is a People Process
Often in the design and construction of manufacturing projects there is a huge emphasis on technical qualifications of the design and construction team. Predominantly less of a focus is placed on the “soft skills” that are necessary at the leadership levels of the project team, and it is the soft skills/personalities of leaders that drive the success of the team.
When conducting project interviews — especially for the design/construction of a complex, fast-tracked manufacturing project that requires extensive collaboration to meet an aggressive schedule — consider whether team members have the right “chemistry” to work collaboratively. Many organizations underestimate the positive impact team compatibility can have on project execution or, just as important, how the lack of this chemistry can negatively impact it.
Accelerating Project Execution After COVID Delay
Many manufacturing organizations continue to utilize the same project delivery method over and over because of familiarity and comfort with the status quo. Pandemic-related project delays, however, have prompted manufacturers to investigate alternative approaches to make up for lost time. If implemented effectively, these alternative delivery methods can help manufacturers not only make up for pandemic-related delays and meet critical start-of-production dates, but also enhance their competitiveness by ensuring their product’s speed to market, while potentially achieving some cost savings along the way.
Project Announcements
Busch Vacuum Solutions Plans Tempe, Arizona, Operations
08/18/2025
Made Scientific Establishes Princeton, New Jersey, Manufacturing-Headquarters Operations
08/18/2025
Comcast Establishes West Palm Beach, Florida, Operations
08/17/2025
Buttonwood Farm Expands Fortuna, Missouri, Egg Production Operations
08/15/2025
MerryGoRound Plans Pittsylvania County, Virginia, Fulfillment Operations
08/14/2025
Hartman Cabinetry Plans Jonesburg, Missouri, Operations
08/14/2025
Most Read
-
What We’re Getting Wrong About Gen Z’s Future in the Skilled Trades
Q3 2025
-
A New Course for U.S. Shipbuilding
Q3 2025
-
Optimizing Your Rail-Served Transportation Network: Strategy Before Steel
Q2 2025
-
In Focus: AI Is Changing Incentives Math
Q2 2025
-
How to Choose the Right Site for Your Factory in 2025’s Volatile Landscape
Q2 2025
-
Reshoring Reality Check from Construction
Q3 2025
-
The New Math Behind Mexico and U.S. Manufacturing Decisions
Q2 2025