Vetter: To my knowledge, I don’t believe that we have seen this type of activity happening within our food and consumer products clients’ operations. In fact, what we are experiencing is a ramp up in production on their existing lines. Lines that had some, or even significant amounts of idle time in their production schedule prior to COVID-19, have now been replaced with increased production time in order to meet the higher demand of keeping food on the grocery store shelves, especially ready-to-eat (RTE) foods as well as household cleaning products, disinfectants, hand sanitizer, and toiletries.
One drawback we have seen as a result of this increase in production is that some of the new product projects that our clients were currently undertaking had to be put on the back-burner to meet the higher demands for their existing products. The idle time required for the construction and modification of the lines for those new products and projects is now a very low priority. Currently, there is no appetite from the general population for the next “new” or “improved” product. The old tried-and-true staples are in great demand right now.
AD: What is being done at these plants during this time as far as cleaning and maintenance, etc.?
Vetter: In the food manufacturing world, cleaning and maintenance are second nature. Having appropriate cleaning plans for product switches and end-of-run productions is standard and something these manufacturers are accustomed to performing. Meeting the FDA guidelines for that is adequate during the current pandemic. However, general cleaning of frequent touch points such as door handles and handrails has increased significantly.
AD: How are outside contractors and/or vendors dealt with at those plants that do suspend operations?
Vetter: As mentioned previously, we haven’t experienced any suspended operations with our clients, but we have heard, in cases such as these, most vary by client. Some clients shut their doors to outside vendors completely, while most have followed state and local guidelines that have labeled construction as an “essential” business, so engineers and contractors are allowed in the facility. Overall, in these facilities, there are health assessments/checks with a questionnaire and temperature checks performed prior to any persons entering the facility.
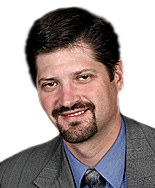
Vetter: Companies are utilizing social distancing as much as possible. They are removing tables/chairs in the lunchroom, decreasing occupancy counts in both conference and meeting rooms, having individuals wear masks — all are standard practice right now. It is also known within this industry that some jobs and tasks must be performed with another employee and social distancing cannot be adhered to. Those types of tasks and contact are being minimized, if possible, and performed only if they can be done safely.
AD: What about retooling plants, e.g., GM now making ventilators? Other examples?
Vetter: One of SSOE’s consumer products manufacturing clients approached us to assist them with the conversion of a portion of their batch tanks to make hand sanitizer solution. It was adapted extremely quickly to help meet the immediate increase in demand. The client produces this sanitizer for donations to local hospitals, nonprofit agencies, and first responders. However, this may become a long-term line as market demand has increased and is expected to remain high.
Many other clients have done what they can, either on an individual level or as an industry group. Utilizing 3D printers, both the companies themselves — and their employees personally — are making face shields and face masks. Additionally, many are making donations of N95 masks to front-line personnel in hospitals and EMT staff. There are a lot of kind actions being performed by many.
AD: Once a business decides it is safe to re-open, what stages must it go through to get up to capacity again?
Vetter: Ensuring their employees can be safe and feel safe is of upmost importance. There are several measures that must be taken to ensure this prior to returning. Some of those tasks include reconfiguring workspaces, offices, and furniture/equipment to help ensure social distancing, making individual face coverings available for each and every employee, creating traffic patterns with designated stopping points and physical barriers for employees if necessary, etc.
Internally, SSOE has created a Return to Office Playbook developed by our COVID-19 Core Team, which details plans for the short-term that need to be executed, as well as policies and procedures associated with moving forward into our new normal.
It will be some time until things get up to full capacity again though. We believe the best approach is a staged process, where only a portion of the employees come back at a time, using alternative work schedules allowing for social distancing. This can occur especially if others can work remotely to help support this effort. Having the proper inventory of PPE, including face masks and hand sanitizer, is a must. All of these things need to be looked at to ensure a smooth and safe transition back.
AD: How does the company maintain the trust of its employees that the workplace is now safe?
Vetter: Employers should be completely transparent with their employees on exactly what they can do and what they can’t. All must follow CDC guidelines to help ensure safety, whether that is adhering to the number of personnel allowed, to taking temperatures of personnel, and providing appropriate PPE to all.