Four Site Factors That Can Derail Your Construction Budget
Although sitework is expensive, most of the expense can be planned and accounted for if your contractor is on board early in the construction process.
Q4 2019
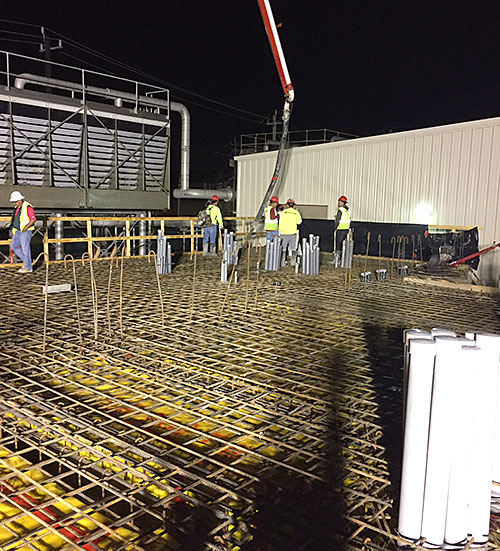
Sitework itself is expensive, but what can cause budgets to skyrocket is when the full scope of sitework isn’t planned and accounted for in the initial budget. There are a lot of unknowns when it comes to a site and — without a full investigation coordinated between the owner, design team, and contractor — those unknowns can cost your project a lot of money. Here are four variables that impact the cost of sitework:
1. Subsurface Conditions
A geotechnical report is the first step to managing the costs associated with sitework. First, it will reflect what kind of soil conditions are present on site. Are the soils suitable for use as fill? Are they moisture sensitive? Will they require chemical stabilization or conditioning? But there’s a lot more your contractor needs to know about what’s going on below grade. Is there rock that will increase the cost of excavation and/or utility installation? Are any of the on-site soils potentially contaminated or hazardous? Are there any potential pits or sinkholes lurking under the surface? What about ground water? Will a perimeter dewatering system be required, or can water be managed by normal sump and pump methods? All of those issues and the work required to resolve them should be fully addressed in the budget as it’s being developed.
At a municipal parking garage site in Florida, we determined, based on the geotechnical report, we needed to relocate an 8-inch and 10-inch water main, approximately 300 linear feet of gas line, and numerous data and phone lines servicing the nearby office buildings and courthouse before we could begin the overall excavation process required on site. From there, in order to get the foundation installed, we had to excavate, turn, import, and backfill more than 300,000 cubic yards of dirt. Without the valuable insight from the geotechnical report, we wouldn’t have been able to plan that work in advance, and it would have delayed the schedule and further impacted the area around the tight site, which was already challenging with limited access and heavy pedestrian traffic.
The labor shortage in our industry has been a persistent problem impacting construction costs, and sitework is no different. 2. The Right Foundation
Once you understand what kind of site conditions you’re dealing with, next you should determine what kind of foundation your building needs. This is a perfect example of how bringing your contractor in to work closely with the design team can save your project money. Can on-site soils be compacted sufficiently to support your building? Or will it require a deep foundation system? Changes in foundation systems can mean an increase in cost. Early evaluation of potential foundation systems could make the difference between being under or over budget.
Knowledge of the Houston-area’s clay-like soils was vital in building the foundation for the Central Utility Plant at a hospital near Houston. The original foundation design called for the foundation to be built directly on the soil. In the past, the hospital experienced similar foundations heave from the soil expanding or swelling, costing them millions of dollars. To prevent the foundation of this new structure from heaving, Hoar partnered with the structural engineer to carton-form the slab. We used 12-inch cardboard-like, honeycomb forms, covered them with Masonite and plastic sheeting, and then installed them between the trench and slab to reinforce it. The cardboard ultimately disintegrated leaving just the Masonite behind, which gives the foundation’s reinforcement a 12-inch movement.
3. Specialized Sitework
There’s a lot of unique site conditions that could require additional work. If that work isn’t accounted for in your budget, it can quickly derail it. On a recent project, the unstable soil required deep dynamic compaction across 40 acres of the site. In addition, a significant amount of contaminated soil had to be treated and cleaned in alignment with EPA standards. Fortunately, our client was aware of the extensive sitework requirements and brought us, their engineer, and design team in early to collaborate, plan, and manage the work.
At another industrial site near Birmingham, Ala., conducting an environmental assessment early on helped us plan enough time for asbestos abatement on a two-story residence-turned-office-building that needed to be demolished before we could begin a 300,000-square-foot plant expansion.
4. Labor Costs
The labor shortage in our industry has been a persistent problem impacting construction costs, and sitework is no different. To combat the issue, we have focused on preconstruction and getting involved early in the building process. This allows us to select trade partners early and gives us and our partners enough time to collaborate as a team to plan out the work and staffing needs. On an industrial project in a remote area of Alabama, this early planning led us to host job fairs in order to hire enough workers to meet a demanding schedule and complicated concrete pours.
There are also other ways to create savings. For example, one of the most expensive factors of excavating and grading in an urban area is the cost of hauling materials to and from the site. We have had success using excess materials on site, eliminating the need for removal. For example, on a recent project, we spread, compacted, and then developed the excess soil into an attractive grassy area. By eliminating the need to haul materials away, we maintained our site budget and kept the design moving forward so construction could start on schedule.
In Sum
Sitework is expensive. But most of the expense can be planned and accounted for if your contractor is on board early. In contrast, a past project — where we were added to the team after the initial program budget was established — developed a major hurdle when we completed our first design development estimate. The program site costs had been initially set at $1 million while, due to unanticipated site conditions, our design development budget came in closer to $2 million. At that point, the only thing we could do was to value engineer the design and cut costs to the actual building. If we had been involved earlier in the design phase, we could have done a full investigation of the site and thoroughly evaluated site development costs, so that a more accurate site estimate could have been included in the budget from the beginning — saving time and money and preventing unpleasant surprises later in the project.
Project Announcements
Buttonwood Farm Expands Fortuna, Missouri, Egg Production Operations
08/15/2025
MerryGoRound Plans Pittsylvania County, Virginia, Fulfillment Operations
08/14/2025
Hartman Cabinetry Plans Jonesburg, Missouri, Operations
08/14/2025
eBliss Global Plans Utica, New York, Manufacturing Operations
08/14/2025
QTS Data Centers Plans Cedar Rapids, Iowa, Operations
08/14/2025
AbbVie Expands North Chicago, Illinois, Production Operations
08/13/2025
Most Read
-
What We’re Getting Wrong About Gen Z’s Future in the Skilled Trades
Q3 2025
-
A New Course for U.S. Shipbuilding
Q3 2025
-
Optimizing Your Rail-Served Transportation Network: Strategy Before Steel
Q2 2025
-
In Focus: AI Is Changing Incentives Math
Q2 2025
-
How to Choose the Right Site for Your Factory in 2025’s Volatile Landscape
Q2 2025
-
Reshoring Reality Check from Construction
Q3 2025
-
20th Annual Area Development Gold and Silver Shovel Awards
Q2 2025