One of the biggest up-front costs for any expansion or relocation project is occupancy and construction. Fortunately, it is a one-time cost that can be amortized over a long period of time, which lessens the financial impact. These costs can also vary significantly from city to city, or region to region. If all other factors are about even between competing locations, then occupancy and constructions costs can be the deciding factor in selecting the final site.
Historically, manufacturing companies tend to construct their own new facilities, given their industry specialization and the often-proprietary nature of their technology and production processes. Companies looking for offices or distribution facilities focus more on finding existing space that meets their workforce and occupancy requirements.
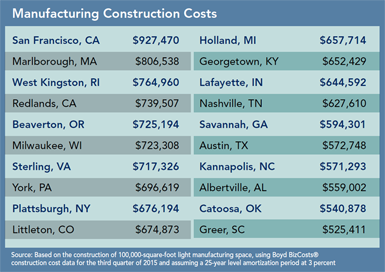
Labor and Materials Costs Up
Labor costs and material costs both of which are showing modest growth during the 2014-2015 period (under 2 percent) are the key drivers that control construction costs, followed by contractor overhead costs. Material price increases in 2015 are led by gypsum board prices, up some 23 percent from last year, followed by lumber and PVC piping (both about a 6 percent increase). Labor costs are affected by higher-than-market union wage scales; more restrictive contract work rules can further increase overall construction costs.
Manufacturing is one of the most robust sectors for new commercial construction. This is the first year since we began tracking U.S. construction activity in the 1990s that manufacturing spending during the past year has led all sectors, with almost $100 billion in new projects. John Boyd, principal with The Boyd Company This is where states with right-to-work legislation definitely have an advantage, says Boyd. Also, the August 2015 National Labor Relations Board decision backed by unions that blurs the lines between employer and contractor will likely have an inflationary impact on costs, especially for already expensive liability insurance, considering the many contractor and sub-contractor relationships in the construction industry.
According to The Boyd Company, hot construction markets are registering the highest rates of construction-cost increases in 2015 including San Francisco at 6.4 percent, Washington, D.C. (5.9 percent), Chicago (5.3 percent), and New York (5.1 percent).
Manufacturing is one of the most robust sectors for new commercial construction. This is the first year since we began tracking U.S. construction activity in the 1990s that manufacturing spending during the past year has led all sectors, with almost $100 billion in new projects, says Boyd. Another growth sector we are experiencing is retail construction, where demand for new brick-and-mortar stores is rebounding, especially in the New York City, Long Island, South Florida, and southern California markets.
Note that construction costs within a metropolitan areas submarkets for example, downtown, midtown, and multiple suburban markets can vary as much or more than comparisons with other metro areas, adds Boyd. New York, Chicago, San Francisco, and Phoenix are good examples of cities with wide variations. Seattle and St. Louis are examples with small variations among their submarkets.