Supply Change: Why A Modular Approach To Warehousing Could Be The Wave Of The Future
With the supply chain challenges that companies will inevitably face, the time is now to explore a more varied approach to warehousing.
Q2 2017
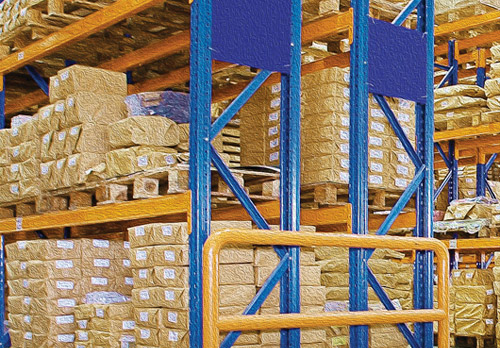
Is a meaningful transformation even possible in an arena where new-and-different demands must ultimately co-exist with brick-and-mortar realities? Thankfully the answer is yes — provided you’re willing to adjust your paradigm of what a workable warehousing framework looks like. To wit, maybe it’s time to consider adopting a more modular methodology for some of your warehousing activities.
What is modular warehousing?
Modular warehousing is a segmented yet strategic approach to distribution center (DC) design. It consists of (a) “deconstructing” a traditional warehouse by identifying its various essential functions and (b) developing a variety of scalable, agile modules for each function that can either be integrated with other functional modules within the same DC or serve as standalone yet virtually connected operations.
Although this practice could involve physical, pre-constructed brick-and-mortar components, most of the modules in question are more conceptual in nature, consisting of carefully designed, easily implemented plans that can be put into play in a wide variety of locales or settings — all working together to provide the wide variety of product assortments, value-added services, and order fulfillment lead times demanded by today’s highly segmented marketplace.
The beauty of the concept is that modules can be assembled and located in a wide variety of ways based on the current needs of various customer segments and then relocated, rearranged, or replaced as these requirements or other market conditions change. It also opens the door for some functions to be located in settings that previously might not have been considered. For example, instead of processing consumer product returns at a company’s main order fulfillment center, companies could instead weigh the pros and cons of setting up separate, localized returns processing centers near courier stores or post offices.
Modular warehousing is a segmented yet strategic approach to distribution center (DC) design. All of this is enabled by recent advancements in information technology that have provided supply chain professionals with unprecedented levels of visibility, optimization, and executional functionality. As a result of these things, numerous warehousing locations or activities can function as if they were co-located in one mega DC, even if they’re not.
How many modular plans/designs does each warehousing function merit — and who should be involved in putting them together?
It’s important to emphasize that just because functional modules are more focused and standardized than traditional warehouses, they are not uni-dimensional. In fact, to facilitate functional efficiency, users should be able to choose from a variety of standard designs for each module, because even at a deconstructed level, a one-size/one-scenario configuration will rarely fit all. Thus the standard selection of modules for a company’s small order pick-and-pack function might include several highly automated configurations for challenging labor markets, as well as several manual configurations for markets where quality labor is in plentiful supply. And, the standard selection of modules for a module that assembles retail point-of-sale displays might include designs for small-, medium-, and large-sized markets.
Material handling equipment (MHE), information technology, and automation/robotics firms can take lead roles in helping shippers and third-party logistics providers design the right set of modules for their businesses, as can supply chain engineers or industry consultants. And — as is the case with standard warehouses — real estate companies and developers can assist in identifying and improving the best sites for each module or collection of modules.
What kinds of warehousing functions might lend themselves to a modular approach?
Traditional warehouses still work well with situations that involve stable, more uniform, and less stringent customer demands — or where bigger means better. However, many of the practices that usually take place within a distinct, well-defined area of a warehouse could lend themselves to a modular treatment if your company is so inclined; in fact, your company may have been applying a modular approach to them without even realizing it. These include consumer return processing operations, value-added services (VAS) work centers, small order fulfillment for traditional brick-and-mortar stores, high-value goods fulfillment, non-conveyable merchandise fulfillment, after-market parts dispatch, and climate-controlled storage.
Any distribution practice that is customer-facing — like customer pick-up — could also be a good modular warehousing match, as could any process that is decidedly different from the rest of a company’s supply chain flow, such as product returns or disposal. In addition, any process that calls for high proximity to customers (same-day delivery, futuristic drone delivery, and 3D printing hubs come to mind) could be an ideal fit.
The beauty of the concept is that modules can be assembled and located in a wide variety of ways based on the current needs of various customer segments and then relocated, rearranged, or replaced as these requirements or other market conditions change. What kinds of rules should guide warehousing module design?
Many of the rules that apply to traditional warehouses apply to the development of warehouse modules, too, especially in terms of engineering and connectivity.
For example, in order to ensure their consistent efficacy from location to location and venue to venue, modules will need to be carefully optimized and tested via simulations and proof-of-concept pilots in the field. Additionally, because they may be located remotely — and thus may not have the benefit of an on-site warehouse manager’s supervision — the use of visibility tools like tracking and tracing sensors, VR (virtual reality), and other technologies that enable managers to “walk the floor” virtually will be even more imperative.
The bottom line? Even if modules are designed to fit into smaller spaces or operate on a smaller or more temporary scale, their success or failure could still have big and enduring implications — and they’ll need to be monitored and evaluated accordingly.
What types of real estate — besides the traditional industrial warehousing space — could warehouse modules work in?
Part of the inspiration and proof of concept for warehouse modules comes from the fact that many retail operations have already begun serving as extensions of companies’ delivery networks. Numerous store back rooms have in essence become their companies’ local fulfillment and returns centers, and logic suggests that it wouldn’t be difficult to establish other warehousing modules within them, too.
Many warehouse modules could also find a hospitable environment in some of the once successful but now empty shopping malls that are located across the country, especially since these facilities possess several distribution-friendly attributes such as good transportation access, ample square footage, and substantial paved areas that could serve as effective truck-staging areas. Other promising candidates for warehousing modules include unused portions of companies’ manufacturing plants, abandoned industrial zones near urban areas, underutilized areas of office buildings, or within portions of other companies’ warehousing operations.
What’s the final takeaway for companies with traditional warehouses?
Due to the fact that your company may already have its hands full trying to run its day-to-day distribution network or accommodate myriad big-box warehousing demands, it may be tempting to table thoughts of exploring modular warehousing until after several early adopters have demonstrated its viability. However, bear in mind that exploring a more varied approach to warehousing now may be exactly what the industry needs in order to address the many supply chain challenges that are inevitably coming – and probably headed our way sooner rather than later. Plus, it’s important to remember that the very fact that warehousing has been operating with a business-as-usual mentality for so long may be precisely why it might be time to adopt a new approach.
Project Announcements
Land ‘N’ Sea Distributing Expands Norfolk, Virginia, Operations
08/13/2025
BuildEx Modular Plans Fayetteville, Tennessee, Manufacturing-Distribution Operations
08/11/2025
Orise Distribution Expands St. Louis, Missouri, Operations
08/11/2025
Canada-Based Mancuso Chemicals Plans Pachuta, Mississippi, Logistics-Distribution Operations
08/11/2025
Coastal Group Establishes Foristell, Missouri, Logistics-Warehousing Operations
08/01/2025
Amazon Plans Little Rock, Arkansas, Logistics Operations
08/01/2025
Most Read
-
What We’re Getting Wrong About Gen Z’s Future in the Skilled Trades
Q3 2025
-
A New Course for U.S. Shipbuilding
Q3 2025
-
Optimizing Your Rail-Served Transportation Network: Strategy Before Steel
Q2 2025
-
In Focus: AI Is Changing Incentives Math
Q2 2025
-
How to Choose the Right Site for Your Factory in 2025’s Volatile Landscape
Q2 2025
-
Reshoring Reality Check from Construction
Q3 2025
-
20th Annual Area Development Gold and Silver Shovel Awards
Q2 2025