Plastics: Relying on Innovation to Ride Out the Recession
The collapse of the auto industry has hit the plastics industry hard. But new medical products and greener plastics are keeping the industry moving forward.
June/July 09
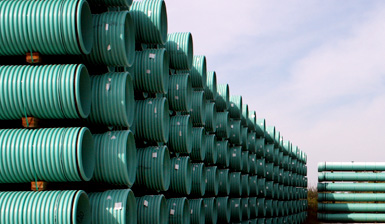
Polymer Transactions is a Cleveland, Ohio-based firm that tracks plastics industry movement such as acquisitions, consolidations, foreclosures, plant closings, and bankruptcies. "The current general economic snapshot certainly applies to the injection molding industry [the largest plastics processing segment], especially in certain market segments such as automotive, construction, major home appliances, and any other segments that manufacture `big ticket' items, the purchase of which can be postponed in a recession," says Bill Ridenour, Polymer Transactions' CEO. "Business values of publicly owned companies have also declined to 45 percent of their high, based on the Dow [Jones] Industrial Average highs and lows for the past 15 months, and senior lending for business financing has nearly dried up, especially for acquisition financing." He predicts that by 2010, the population of plastic processors will decline by as much as 20 percent, in spite of the many consumer markets and industry segments that are relatively immune from the recession.
Thomas E. Blaige, CEO and managing partner for Thomas Blaige & Company LLC in Chicago, notes in his recent report, 2009 Injection Molding M&A Market Update, that the "effects of global consolidation in the fragmented injection molding markets have resulted in an increase in the number of deals from 57 in 2002 to 105 in 2007 and to 104 in 2008." However, he projects that purchase prices will be attractive for those injection molders that "possess a defensible niche."
"Injection molding companies will continue to get squeezed as suppliers and customers continue to grow and gain leverage," says Blaige in the report. "Those with volume less than $100 million will continue to see their negotiating leverage decline, and suppliers are continuing to tighten credit and to week out non-core customers, reflecting a flight to quality." He also says that increasing raw material prices haven't done the industry any favors. Rising prices to processors and a reluctance of customers to accept price increases have generally meant shrinking margins and reduced profitability.
Auto Decline Hurts Industry
The economic slump that has impacted almost every segment of plastics processing has hurt many states that once counted on a strong plastics industry to serve other large OEMs in markets such as building and construction, automotive, medical, packaging, and almost every other segment where plastics are ubiquitous. Michigan has been hardest hit, with many Tier One and Tier Two suppliers being sucked into the eddy of a deepening auto recession.
The credit crunch has left smaller plastics processors and mold manufacturers in a bind, even as they seek to collect from their automotive customers. Many have shuttered their plants and walked away, unable to extend credit lines. Some companies have been lucky enough to sell their businesses. Monomoy Capital Partners LP, the owner of Fortis Plastics LLC of South Bend, Indiana, purchased the assets and operations of resin compounder Global Thermoplastics LP. This represented the fourth acquisition made by the New York-based private equity group in eight months. Monomoy started on its plastics binge in 2008 when it bought the custom molding divisions of Leggett & Platt Inc. and Atlantis Plastics Inc. and started Fortis. It then added Moll Industries Inc.'s Ramos, Arizipe, Mexico, plant in February 2009 to expand Fortis' reach.
Medical Market a Bright Spot
In spite of the doom and gloom of the automotive industry, there are bright spots for the plastics industry; medical products is one of them. Demand for medical plastics in the United States is forecast to expand 2.6 percent annually to five billion pounds in 2012, valued at $6.55 billion, according to The Freedonia Group, an Ohio-based industry research firm. The trend reflects a shift to an older demographic, resulting in a rising incidence of acute and chronic conditions and thus an increasing volume of patient activity that will broaden overall demand for medical devices, supplies, and packaging. Demand for commodity plastics - PVC, polypropylene, polyethylene, and polystyrene - used in the production and packaging of medical products is expected to rise 2.3 percent yearly to 4.3 billion pounds in 2012, valued at $4.6 billion.
The Freedonia Group report says engineering plastics accounted for 11 percent of the total volume of medical plastics in 2007, but a much higher 27 percent of total value. Demand for engineering plastics such as polycarbonate, which is expected to remain the leading engineering resin and exhibit the best growth prospects, is expected to expand 5.2 percent annually to 630 million pounds in 2012, reaching nearly $2 billion. Advances will be based on needs for higher performing materials in surgical instruments, diagnostic testing, drug delivery, geriatric care and preventative medicine.
Medical molding continues to be strong, particularly in the area of medical disposables, minimally invasive surgical devices and diagnostics equipment. MedPlast Group is a medical molder/contract manufacturer that was put together just over a year ago, and rapidly gained ground through a series of acquisitions, which is becoming a new paradigm in the molding business.
Led by Harold Faig, the group's CEO, investors put MedPlast together to meet the unique, ongoing needs of the medical market. The investors simultaneously purchased ATP's Engineered Rubber and Plastics Group and K&W Medical Specialties in April 2008, forming a world-class manufacturer in the medical device market under the umbrella of MedPlast. The newly created company has manufacturing facilities in Westfield, Massachusetts; Tempe, Arizona; Elkhorn, Wisconsin; West Berlin, New Jersey; and Monticello, Iowa. Between all five plants, MedPlast has over 750 employees.
Project Announcements
Palmetto Plastics Innovations Plans Hardeeville, South Carolina, Manufacturing Operations
04/11/2025
Denmark-Based Primo Plans Mobile, Alabama, Production Operations
04/07/2025
Italy-Based Serioplast Plans Shenandoah County, Virginia, Operations
02/09/2025
Letica Expands Fulton County, Kentucky, Operations
02/05/2025
Canada-Based Markdom Michigan Plastics Plans Charlotte, Michigan, Production Operations
01/13/2025
NUPI Americas Expands Early Branch, South Carolina, Production Operations
12/18/2024
Most Read
-
Run a Job Task Analysis
Q4 2024
-
39th Annual Corporate & 21st Annual Consultants Surveys: What Business Leaders and Consultants Are Saying About Site Selection
Q1 2025
-
The Location Economics of Advanced Nuclear
Q1 2025
-
Why Workforce Readiness Can’t Wait
Q1 2025
-
Power, Policy, and Site Selection in 2025
Q1 2025
-
Is It Time to Start Planning for Quantum Data Centers?
Q1 2025
-
Top States for Doing Business in 2024: A Continued Legacy of Excellence
Q3 2024