The quality and quantity of the available skilled workforce is critical to attract corporate expansion projects for U.S. economic development. For more rapid reshoring to take place, the U.S. needs a higher skilled and larger workforce. Recruiting that workforce also requires that reshoring be visibly successful. Ultimately, reshoring and skilled workforce go hand in hand — you simply can’t have one without the other.
The U.S. Workforce Skills Gap
The U.S. will need to fill approximately 3.5 million manufacturing jobs over the next 10 years. However, it is estimated that there will be a talent shortage of two million skilled workers, according to a recent study from Deloitte and The Manufacturing Institute. According to the research, 84 percent of manufacturing executives agreed that there is a talent shortage in U.S. manufacturing; 82 percent feel the shortage impacts their ability to meet demand, while 78 percent say it impacts the implementation of new technologies that increase productivity and competitiveness.
A study done by Accenture PLC and The Manufacturing Institute similarly found that 75 percent of manufacturers were having trouble finding skilled production workers. According to Reshoring Initiative data, skilled workforce availability and training ranked number two in the reasons given by companies for reshoring and foreign direct investment (FDI). Also, when companies reshored and failed to find the needed workforce, the transition was painful.
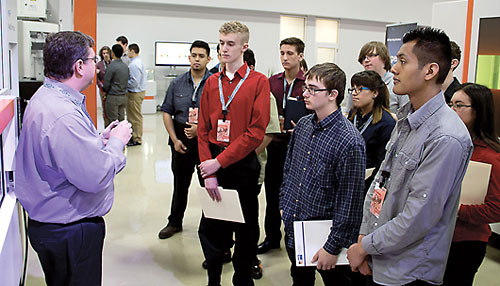
The importance of changing the perception that training is not as important as degrees can’t be stressed enough. Case in point: In 2012 I was invited to the Department of Labor (DOL) to recommend to DOL how to prepare the skilled manufacturing workforce needed to support reshoring. I pointed out that the DOL’s website was biased toward education at the expense of training. At the time, the Bureau of Labor Statistics (BLS) website showed the relationship between income and degree level and that was headed “Education Pays.” I recommended that the title be changed to “Education and Training Pay” and that the income of workers that have passed an apprenticeship or have a strong portfolio of NIMS, MSSC or AWS certificates be shown along with the income of degree-holders. DOL immediately accepted the need to revise the site, eliminated the “selling” of education from the heading, and added text about “apprenticeships and other on-the-job training.”
Minneapolis-based Dunwoody College of Technology’s Machine Tool Technology AAS degree program’s experience confirmed the gap in statistics. Of 22 graduating students, 21 were already fully employed in the industry, as compared to 53 percent of college grads who were unemployed or underemployed. Dunwoody received over 450 requests to hire the class of 2012 as well as complaints from 50 companies wanting to hire graduates proficient in machine tool technology, but finding none available.
Community and technical college and apprenticeship programs can set regions apart in the short-term. The Misperceptions About Manufacturing
The cause of the growing skills gap is twofold: baby boomer retirement and students and parents who have misperceptions about the stability and growth potential of manufacturing careers, thus limiting the flow of recruits. Many believe there is no future in manufacturing and that all the work will continue to be sent offshore and, therefore, manufacturing is a risky career choice. Too many students are attending four-year universities, resulting in 40 percent of non-technical university graduates being in jobs that do not require a university degree. The major obstacles to manufacturing recruitment are:
- Perception that training is not as important as degrees;
- Perception of ongoing manufacturing decline due to offshoring;
- Perception that vocations/trades training is lower prestige/income than a four-year university degree; and
- An historic belief that manufacturing is dirty, dark, dangerous, and boring.
Closing the Gap
A recent Harvard Business School study cited in a New York Times article, suggests the U.S. is facing a critical shortage of workers with technical skills because “employers are more inclined to invest in technology or hire part-time workers than spend money on training programs…[and] companies have lagged in collaborating with community colleges to develop training programs.”
Skills and talent issues have always been, and continue to be, an issue for site selection, but the gap is viewed as more critical in the U.S. than in Europe or Asia Phil Schneider, a site selection consultant Location decisions will be determined by the ability to demonstrate an abundant, quality, and sustainable supply of skilled technical workers. Those areas that can develop and sustain evolving skill sets are poised for sustained growth. Community and technical college and apprenticeship programs can set regions apart in the short-term, while communities address long-term structural gaps in the primary education system.
There is a new wisdom about education and training. Apprenticeships are the new gold standard. The trend is towards implementing programs like those that are so successful in Switzerland and Germany. These are apprenticeship programs with strong academic and technical training that are designed to create innovative team skills and skilled use of CNC, computers, 3D, and CAD. Students enjoy a practical foundation, earning a professional credential and earnings that begin now, without the enormous university degree student debt.
Creating a stronger skilled workforce is key to reshoring and the country’s manufacturing growth. Manufacturing is central to a vibrant economy. America needs a coordinated effort between our public educational system, government, and business leaders to provide the proper alignment between jobs and skills development in order to shape our workforce and drive our economy.
There is some good news on the skilled workforce front. NIMS and MSSC, the two-metalworking credentialing programs, have been increasing their rate of awards by about 15 percent per year for 10 or more years. Apprenticeship programs are accelerating, often in the German or Swiss model. In Switzerland about 70 percent of students go into apprenticeships at the age of 16. Those countries have trade surpluses of about 3 percent of GDP vs. the U.S. 3 percent trade deficit. The difference is about eight million well-paid manufacturing jobs, maybe 15 to 20 million total jobs.
Switzerland has an official agreement with the U.S. Labor and Commerce departments to help the U.S. develop training programs. Swiss companies’ U.S. operations, including Daetwyler and Hydromat, have very effective programs. Others, such as SMTS (Swiss Machine Tool Society) members GF Machining Solutions, BIG Kaiser, and Rollomatic are actively helping high school and community colleges strengthen recruitment and training.
The Reshoring Initiative also offers communities and companies a variety of resources to help develop the local skilled workforce. Reshoring is a fast and efficient way to strengthen the U.S. economy, foster a skilled workforce, and benefit manufacturing companies by reducing total costs, improving balance sheets, and supporting innovation.