Manufacturing Workforce Certifications Will Help to Close the Skills Gap
Promoting the pursuit of in-demand manufacturing certifications will result in a win-win situation for both the manufacturer and the community in which it chooses to locate.
Workforce Q4 2017
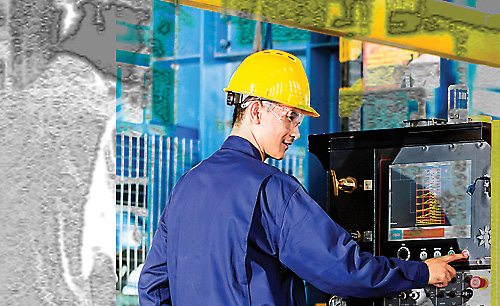
Today, recruiting and keeping skilled talent in manufacturing is a daunting challenge. The sector suffers from a skills gap as mature manufacturing workers are retiring, and the numbers of younger workers necessary to fill the empty positions — workers with the proper skills to do the job in today’s high-tech operations — have not kept up.
Compounding the skills gap is the perception among young people — and those that guide them — that manufacturing facilities are dark, dirty, and dangerous rust-belt dungeons of days gone by. These individuals are unfortunately unaware of the fact that most forward-thinking manufacturing facilities are clean, bright, efficient workplaces that use some of the most cutting-edge technological advances available — and offer some of the best career opportunities around today for bright young people willing to work hard.
Whatever the nature of the manufacturing skills gap, as with all challenges there are remedies. One of these involves promoting the acquisition of certifications among a community’s workforce. The more individuals who possess the certifications manufacturers seek, the more attractive the community workforce is to an organization that’s assessing that community as a potential home for a new facility.
Manufacturing Certifications Today
What types of certifications are valuable to manufacturers today? Three of the most popular are those for set-up technicians, control technicians, and multi-skilled maintenance technicians. Set-up technicians’ responsibilities include setting up machines (and new jobs on those machines) so operators can initiate production cycles and ensure ongoing, efficient operations. Control technicians specialize in automated controls in process industries, and as automation continues to revolutionize manufacturing these individuals will continue to remain in high demand. Multi-skilled maintenance technicians — those who possess skill sets involving a number of maintenance disciplines — are in especially high demand these days.
It has been popular in the recent past for manufacturers to invest heavily in engineers and financial personnel. Now they’ve had to recalibrate their thought process concerning the vital need for maintenance as it relates to efficiency, productivity, and revenue.
The Road to Certification
How does a community promote the pursuit of in-demand certifications so its workforce is attractive to potential incoming manufacturing employers? Building worker skills is best undertaken as a multi-pronged endeavor. Encouraging the development of appropriate courses and curriculum at nearby vocational and technical schools is a great start. Working with local high schools and counselors to counter incorrect perceptions and promote opportunities in manufacturing is another valuable effort.
There is no doubt that the manufacturing skills gap is a challenge to both employers seeking to locate a new facility, and communities looking to encourage manufacturing growth in their areas. Encouraging manufacturers to offer blended learning programs is another strong way to widen the workforce potential. Blended learning programs start with well-defined assessment testing of individuals that is then reported on in detail. The resulting analyses look at skills gaps not only by individual but also value stream, facility, and disciplines. Once specific insufficiencies are identified, a process-driven blended learning development plan can be outlined and implemented, with gate reviews, benchmarked milestones, and deadlines that are designed with both the individual’s and manufacturer’s needs in mind.
Certified Success
There is no doubt that the manufacturing skills gap is a challenge to both employers seeking to locate a new facility, and communities looking to encourage manufacturing growth in their areas. The development of an attractive, appropriately skilled workforce is a vital piece of the complex puzzle. However, with a little forethought and effort regarding the certifications that are most in demand today, both manufacturers and the communities they seek to call home can eventually enjoy success in the form of a highly productive facility and economic growth and prosperity in the area.
Project Announcements
MR6 Tech Services Plans Huguley, Alabama, Manufacturing Operations
07/29/2025
Adient Plans Normal, Illinois, Production Operations
07/29/2025
UK-Based WB Alloys Plans Danville, Virginia, Manufacturing Operations
07/29/2025
L3Harris Technologies Expands Camden, Arkansas, Production Operations
07/25/2025
Baltimore Fabrication Expands York County, Pennsylvania, Manufacturing Operations
07/25/2025
Mueller Streamline Expands Wynne, Arkansas, Manufacturing Operations
07/25/2025
Most Read
-
20th Annual Area Development Gold and Silver Shovel Awards
Q2 2025
-
In Focus: AI Is Changing Incentives Math
Q2 2025
-
Optimizing Your Rail-Served Transportation Network: Strategy Before Steel
Q2 2025
-
How to Choose the Right Site for Your Factory in 2025’s Volatile Landscape
Q2 2025
-
From Silicon to Server: Mapping the Data Center Supply Chain
Q2 2025
-
Tariffs, Talent, and U.S. Expansion
Q3 2025
-
First Person: David Robey, Co-CEO of QTS Data Centers
Q2 2025