Are Your Employees Ready to Work with Robots?
As manufacturers increasingly employ robots on the factory floor, they must communicate to their workforces how their roles will change and prepare them to work collaboratively with this new technology.
Workforce Q4 2019
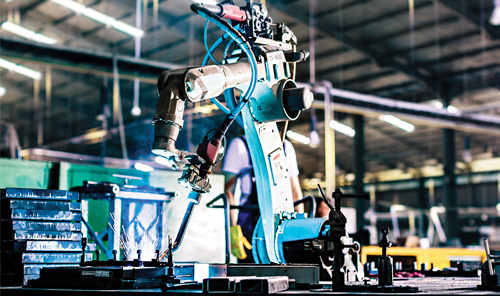
According to a report published by Reuters, U.S companies installed more robots than ever before in 2018. Shipments of robotic machinery hit a colossal 28,478 deliveries — that’s a 16 percent increase compared to the previous year. Deployment increased in almost every sector, including life sciences, food and consumer goods, and semiconductors and electronics.
As more sectors embrace manufacturing’s robotic revolution, it raises more questions about how to correctly deploy the technology. Unsurprisingly, there’s a lot of planning, organizing, and risk assessment required to integrate a new robot onto an existing production line. But, preparing for the impact robots can have on human workers is often overlooked. So, how can manufacturers prepare?
1. Remove automation anxiety.
There are plenty of scaremongering statistics deeming the rise of automation as the demise of the human employee. However, this simply isn’t true. Humans have a natural desire to create tools and machinery to reduce the need for physical labor. In fact, over the last few centuries, we have almost obliterated the need to complete physical tasks at all — or at least, we have made them significantly easier.
Manufacturing offers plenty of examples of this — from the invention of the printing press in the fifteenth century, right through to the intelligent robotics and automation we see gracing the floors of factories today. Despite our ubiquitous desire to reduce manual tasks, humans’ fear of automated technology is seemingly more prevalent than ever before.
During the last decade, fears of automation-driven job losses have surged — strange phenomenon, considering robotics have played an integral part of manufacturing since as early as the 1960s. Perhaps some of this concern is due to the rapid advancement in technology. Let’s face it; today’s automation goes far beyond mechanical muscle. There’s no denying that a human worker cannot compete with the strength, speed or stamina of a robot. However, only recently have the intelligence and decision-making skills of machinery advanced to a competitive level.
Smart factory software provides a good example. Modern platforms will include a distributed control system (DCS), alongside standard supervisory control and data acquisition (SCADA) software. When integrated with factory machinery, this software can collect and analyze data at a speed unattainable by a human worker, allowing it to make decisions based on real-time factory activity.
For instance, the software could identify opportunities to save energy during periods of machinery downtime. By cross-referencing production data with operational information of each machine in the factory, the software could easily point out periods in which certain machines could be switched off or turned on standby. A human employee could never process and analyze this much data at this speed. However, there’s no reason intelligent software and intelligent machines cannot work harmoniously with humans. Software can collect and analyze data quickly, but human minds are often required to make informed decisions on what’s right for the factory. Clearly, there’s no advantage to collecting production data without plans to act on it.
While robotics and intelligent machinery will replace some factory roles, this technology will not remove humans from the equation completely. To lessen the fear of automation anxiety in the workforce, it is vital that plant managers are transparent about the changing roles of humans. Admittedly, human workers might not be required for menial and manual tasks, but there’s certainly still space for humans in the factory.
To avoid internal gossip and scaremongering when deploying robots, plant managers should be clear about how the new investment will change requirements and expectations of human workers. But, let’s be realistic — if workers believe their role could be replaced by a robot, it probably can.
It is also important to reiterate to existing workers that deploying robots will eliminate tedious and manual tasks. 2. Reskill and retrain.
Manufacturers considering purchasing a robot should also consider investing in the training and upskilling of their existing employees. Reskilling existing workers will reduce the likelihood of redundancies and, therefore, improve the company’s reputation as an employer — a common problem when reducing the number of employees but increasing automation.
Deploying robots, or any automation machinery for that matter, will create a new requirement for engineers with programming and maintenance skills. As opposed to employing a new programmer, manufacturers should consider training an existing production operative to take on this role — perhaps a worker whose role the robot will replace or reduce.
Several industrial robot manufacturers and suppliers will provide free training on how to correctly program and maintain their machinery, so it is worth looking into this before investing in external courses. Alternatively, should manufacturers purchase a robot from an industrial parts supplier, they will benefit from access to the company’s global network of automation manufacturers, allowing them to choose the right parts for them.
It is also important to reiterate to existing workers that deploying robots will eliminate tedious and manual tasks. By nature, humans want to create and to invent and solve problems — not complete repetitive movements such as box opening, bin-picking or basic assembly processes. This is particularly prevalent for workers with engineering backgrounds.
Communicating this benefit with staff is essential. Manufacturers need to be clear that, rather than engineering humans out of a job, robots can be used to allow operators to take on more challenging opportunities — but only, of course, if plant managers allow it.
3. Reveal the benefits.
Providing transparency and training to staff will alleviate some resistance toward automated technology but, post-deployment, there is more work to be done. Without providing evidence of the benefits of automation, it is likely that human workers will still harbor resentment toward the investment — particularly if there have been cuts in other areas.
Most manufacturers will have key performance indicators (KPIs) and targets for productivity and quality improvements when deploying robots in a factory, so why not share this data with staff? Naturally, production operatives may not be interested in profit margins and financial benefits, as compared to C-level executives. However, positive information and data related to productivity increases, improvements in product quality, and injury reduction should be shared with staff.
Injury prevention, for example, is one of the most emotive advantages of incorporating automation in a factory. By removing humans from potentially dangerous tasks, the likelihood of injury will be reduced. Sharing this data with staff can be done through a simple internal communication process, such as a newsletter or an intranet system. Alternatively, manufacturers could produce datasheets and case studies illustrating these advantages of automation deployment.
Changing employee culture is one of the biggest challenges when deploying robots in particular. Critically, the efforts of senior management cannot stop once the robot has been integrated. Manufacturers should aim for workers to respect and care for the machines they are working alongside. Therefore, highlighting the advantages of this machinery on an ongoing basis is integral to establishing a culture that embraces automated technology, rather than resents it.
This will become even more important as manufacturers begin to deploy collaborative robots or cobots — a new type of robot that can operate alongside human workers. Due to the reduced speed and power of these machines, compared to industrial robots, cobots can currently operate at the same workstations as production operatives, often working on the same tasks, at the same time.
Cobots operate safely by using sensors to identify when a human worker comes in dangerously close contact. When it detects a human presence, the cobot will slow down or stop operations to ensure the worker remains safe. While this feature stops workers coming into direct contact with the robot, cobots are the most obvious example of humans and robots working in extremely close collaboration, increasing the need for an automation-friendly culture in the workplace.
Science fiction might portray robots as the arch nemesis of humans, but we know that isn’t the case. As a growing number of U.S. manufacturers invest in robots, plant managers cannot overlook the importance of company culture when integrating this technology.
Project Announcements
Wyandot Snacks Expands Marion, Ohio, Production Operations
08/29/2025
Trane Technologies Expands Fort Smith, Arkansas, Operations
08/29/2025
BioMADE Plans Boone, Iowa, Bioindustrial Manufacturing Operations
08/29/2025
Choice Fabricators Expands Rainbow City, Alabama, Production Operations
08/29/2025
Ranovus Expands Ottawa, Ontario, Semiconductor Operations
08/29/2025
Belgium-Based Stow Group Plans Gordon County, Georgia, Manufacturing Operations
08/28/2025
Most Read
-
Tariffs, Talent, and U.S. Expansion
Q3 2025
-
What We’re Getting Wrong About Gen Z’s Future in the Skilled Trades
Q3 2025
-
Data Center Demand Stabilizes Amid Changing Market Forces
Q3 2025
-
A New Course for U.S. Shipbuilding
Q3 2025
-
Optimizing Your Rail-Served Transportation Network: Strategy Before Steel
Q2 2025
-
In Focus: AI Is Changing Incentives Math
Q2 2025
-
Rewriting the Rules of Warehouse ROI
Q3 2025