Front Line: Electrification of Industrial Processes
Reducing the use of fossil fuels in industrial processes will help cut costs while reducing GHG emissions.
Q4 2023
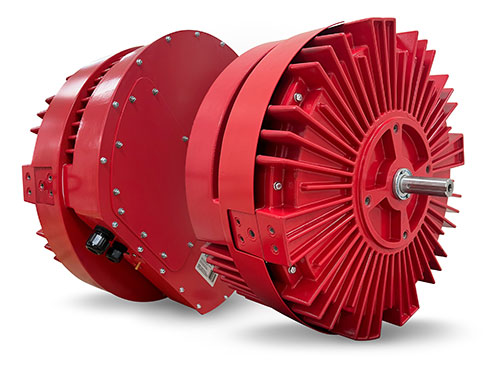
Globally, industry (all of the companies involved in manufacturing and the production of physical goods) consumes more energy than any other sector: 149 million terajoules in 2017, according to a recent report from McKinsey. Relatively little of that energy consisted of electricity: about 20 percent. Most of the electricity consumed by industry is used to power equipment such as pumps, robotic arms, and conveyor belts, the report says. As the prices of renewable electricity and electric equipment continue to drop, industrial companies can capture cost-saving and GHG-emission-reduction opportunities by planning the electrification of their operations.
McKinsey projects that renewables could produce more than half of the world’s electricity by 2035, at lower prices than fossil-fuel generation. The resulting lowering of electricity prices — along with the falling cost of electric equipment and more stringent greenhouse-gas (GHG) emission regulation — is expected to boost consumption of electricity in sectors, such as passenger vehicles and space heating, where fossil fuels have long been the standard energy source.
The financial and environmental benefits for industrial companies of using electricity instead of fossil fuels in their processes are increasing. Generally, electrically driven equipment is only slightly more energy-efficient than the conventional option, but it has lower maintenance costs, and, in the case of the industrial boiler, the investment cost of the electrical equipment is lower, according to McKinsey. Also, using zero-carbon electricity, can significantly lower an industrial company’s greenhouse gas emissions.
The financial and environmental benefits for industrial companies of using electricity instead of fossil fuels in their processes are increasing. Of all the fuel that industrial companies use for energy, McKinsey estimates that almost 50 percent could be replaced with electricity, using current technologies. This includes all energy required to generate heat for industrial processes up to approximately 1,000 degrees Celsius. That could be accomplished by replacing a piece of equipment powered by conventional fuel — such as a furnace or boiler — with a piece of electric equipment.
Makers of electric motors have been making significant advancements in energy efficiency. For example, Infinitum Electric, a startup based in Round Rock, Texas, makes electric motors that are half the size and weight of standard motors. Infinitum investors include Caterpillar and Rockwell Automation. Infinitum founder and chief executive Ben Schuler says one of the keys is using variable frequency drives, “which permit the motor to adjust speed to meet the actual power demand of an application and save energy.”
Schuler cited data from the U.S. Department of Energy, projecting that implementing advanced motor technology in the U.S. industrial and commercial sectors can save 127 terawatt-hours per year (TWh/yr.), resulting in cost savings of $14.7 billion and reductions of 90.2 MMT of CO2. “That’s equivalent to the annual electricity use of all households in California and North Carolina combined,” Schuler says.
To help industry adapt to electrification, Minneapolis-based manufacturer Thermo King has partnered with the University of Minnesota’s Technological Leadership Institute (TLI) to develop a program to “train engineering and adjacent employees on electrical engineering basics at a detailed design level” says Grant Ovsak, leader of Thermo King Americas’ Electrification Center of Excellence. The program’s ultimate goal is to enable development in converting fossil-fuel power-based systems to electrified power-based systems. “This is an important step in helping move the nation, and the world, to green power sources like hybrid or all-electric through education,” Ovsak says.
“The refrigerated transportation industry is going through the same transition as the automotive industry as we work to move toward more sustainable power sources,” Ovsak explains. He predicts that, as the Infrastructure Investment and Jobs Act and other transportation funding grows in impact, that will increase demand for transitioning away from fossil-fuel systems to hybrid and fully electric designs. TLI and Thermo King hope other industrial companies will benefit from training programs similar to theirs in order to accelerate the move away from fossil fuels.
Project Announcements
MR6 Tech Services Plans Huguley, Alabama, Manufacturing Operations
07/29/2025
Adient Plans Normal, Illinois, Production Operations
07/29/2025
UK-Based WB Alloys Plans Danville, Virginia, Manufacturing Operations
07/29/2025
L3Harris Technologies Expands Camden, Arkansas, Production Operations
07/25/2025
Baltimore Fabrication Expands York County, Pennsylvania, Manufacturing Operations
07/25/2025
Mueller Streamline Expands Wynne, Arkansas, Manufacturing Operations
07/25/2025
Most Read
-
20th Annual Area Development Gold and Silver Shovel Awards
Q2 2025
-
In Focus: AI Is Changing Incentives Math
Q2 2025
-
Optimizing Your Rail-Served Transportation Network: Strategy Before Steel
Q2 2025
-
How to Choose the Right Site for Your Factory in 2025’s Volatile Landscape
Q2 2025
-
From Silicon to Server: Mapping the Data Center Supply Chain
Q2 2025
-
Tariffs, Talent, and U.S. Expansion
Q3 2025
-
First Person: David Robey, Co-CEO of QTS Data Centers
Q2 2025