Dernberger: Yes, there has been a surge in demand for contingent workers in the U.S. In fact, contingent jobs comprise about 2 percent of all U.S. jobs today. In the grand scheme of the entire job market, that’s a small percentage, but it amounts to an all-time high of three million contingent jobs.
AD: What types of companies traditionally use contingent workers?
Dernberger: Historically, contingent workers were most prevalent in the service sector or in clerical work, but we’ve seen a radical transition. In 1990, 42 percent of the U.S. contingent workforce consisted of clerical workers, while 28 percent were manufacturing and industrial workers. By 2000, those percentages had flipped, with 47 percent of the contingent workforce consisting of manufacturing and industrial workers, a trend that has remained consistent.
AD: Why do you think there’s been an increase in temporary workers being utilized by manufacturers?
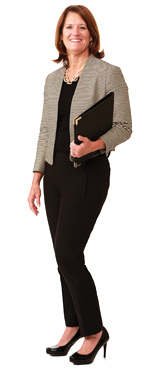
AD: Are temporary workers being used in skilled or unskilled manufacturing jobs — or both?
Dernberger: Both. We see strong demand for contingent jobs in both skilled and unskilled roles. Due to manufacturers’ increased sophistication with processes and technology, many of the typical positions now require further education. Therefore, contingent workers in the manufacturing sector need more training than in the past, whether it’s training on company requirements, welding, forklift driving, or SAP. This requires more of an investment of a company’s time and money.
AD: What are the advantages of employing temps in manufacturing positions?
Dernberger: From the employer’s point of view, contingent employees allow businesses to hire seasonally or on a project basis, flexing their workforce to meet demand. They save money by outsourcing recruiting, screening, and interviewing job candidates, as well as the overhead costs associated with employees, all of which are taken on by the staffing partner. In some instances, especially those labeled as “temp-to-hire” positions, the contingent employee’s time in the role serves as a trial period during which the employer can see if that worker is a good fit - in terms of skillset and culture.
AD: How does the worker benefit from being hired on a contingent basis?
Dernberger: This approach affords the worker the same opportunity to test the waters, while having the flexibility to seek other positions if a job is not a fit. This is particularly attractive for people looking to make a career change or expand their skillset. For experienced workers, contingent positions offer flexibility with commitment and schedule, the opportunity for ongoing work and income, and a chance to keep skills sharp and current. For candidates new to the job market, contingent work makes it possible to establish a foundation of experience, learn the latest skills, work in a variety of roles/companies and build a professional network.
AD: If temporary workers transition to permanent manufacturing employees, at what juncture does that occur?
Dernberger: There are several factors that can motive an employer to offer a contingent employee a permanent role. First, employers don’t want to lose top talent, and they recognize that permanent positions tend to be more attractive to job-seekers and result in better retention. Second, employers want to be sure they have a long-term need for employees before taking on more permanent staff. Employers don’t hire in anticipation of growth, both for their own sake and to protect employees from downsizing that could have been prevented with careful planning. Finally, some roles are temp-to-hire from the start, and the temporary period serves as an on-the-job interview. After a short time, typically 30 to 45 days, a permanent employment offer is extended to someone that proved to be a good fit.
AD: What challenges do manufacturers who employ temps face and how are they being addressed?
Dernberger: An important challenge is ensuring the right skills fit. There is an increasing awareness that for domestic manufacturing to prosper, a different set of skills is necessary to meet companies’ current and future needs. Most of [today’s manufacturing] jobs are for skilled production workers in roles like machinists, operators, craft workers, distributors and technicians. These jobs require extensive training and are difficult to fill. Therefore, a key priority in 2015 will be for employers to shift from hiring employees with specific skillsets to focusing on creating an ongoing learning and career culture. Employers must empower employees to become partners in a continuous life-long learning and development process. This will allow employees to keep learning and take on multiple roles in order to bring value to the business more quickly.
AD: What is required for a company to effectively employ a contingent workforce?
Dernberger: In my experience, there are three components to a successful contingent program: rate of pay, hire-in options, and workforce culture (how people are treated). If any one of these components is lacking, then the other two should be more robust to compensate.
There are two models that are successful: (1) a consistent percentage of the workforce is contingent — for example, a manufacturer keeps the workforce 20 percent contingent at all times, allowing flexibility to ebb and flow as business demands change; (2) companies that are confident in their long-term production forecast will engage an organization like Manpower as an extension of their human resources department to recruit, assess, screen, interview, onboard, and place candidates. Clients look to these contingent workers as their candidates for direct hire.
AD: Is there anything else you’d like to add to the discussion?
Dernberger: Due to the aging North American workforce and a lack of younger talent to fill the pipeline, a “double squeeze” exists in manufacturing resulting in skills shortages at both entry and senior levels. Because of declines in domestic manufacturing, productivity gains, and a weak economy, many companies hired few manufacturing workers of any type over the last couple of decades, so young talent is sparse. In addition, many seasoned employees are nearing retirement. This generational shift will lead to even greater demand for new manufacturing workers for the jobs that remain.