According to the Aerospace Industries Association (AIA) 2014 Year-End Review and Forecast, total aerospace industry sales in 2015 are estimated to come in at $240.4 billion, up 5.2 percent from 2014’s $228.4 billion. Aerospace exports continued to climb in 2014, up $8.1 billion to $118.9 billion, with most of the increase occurring in the civil sector.
Sales for large commercial aircraft, particularly Boeing’s 787, 737, and 737 MAX, are robust. U.S. operations for Embraer, Bombardier, Beechcraft, and Cessna are increasing as well. Military sales by contrast are flat; both the F-22 and, more recently, the C-17 Globemaster programs have ended, and while foreign military revenues are expected to play a larger role in the future, that increase will not make up for the net downturn in domestic spending.
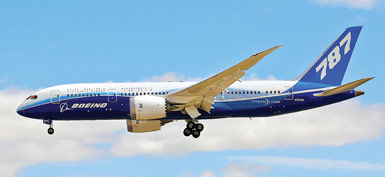
All this means that the U.S. aerospace workforce must become smaller, smarter, and even more productive. Research by the U.S. Bureau of Labor Statistics shows that aerospace manufacturing employment has been on the steady decline since 2012. Over the past three years, in fact, total employment has dropped from 498,600 to 479,900. The decrease has hit factory personnel particularly hard; the number of production workers has dropped 6.6 percent over this period versus 3.8 percent for all manufacturing employees. Current employment stands far below the high of 516,700 total workers reached in 2000.
At the same time that the workforce is shrinking, the need for skilled workers has never been greater. A private survey conducted by Advanced Technology Services (ATS) and ACNielsen shows that 41 percent of all skilled tradesmen in the U.S. will retire by 2017. An Industry Week survey, also commissioned by ATS, found that 39 percent of aerospace companies believe the labor shortage is having an “extreme” effect on their ability to grow their businesses. Aviation Week, in a 2012 study, reported that the average age of aerospace employees is 45 — and only 4.19 percent of all industry employees are between the ages of 22 and 25.
The need for aerospace manufacturers to do more with fewer employees is driving productivity initiatives like never before. The imperative for new solutions and smarter ways of working was summed up in the AIA’s Year-End Review: “Companies will need to become even more efficient to stay competitive. Whether it’s exploiting mature technologies in new and different ways, developing new approaches to existing problems, or exploring cutting-edge processes, technologies, and products, U.S. [aerospace] companies will need to devote even further energy to innovation in the future.”
If firms are searching for answers from their most experienced workers, they better ask quickly. Longtime aerospace workers are retiring in record numbers; the chart of employees reaching retirement age looks like a bow wave, with many crossing the 60-year-old milestone in the next couple of years. More will follow — and with them, a vast trove of technological and engineering knowledge.
Short- and Long-Term Strategies
Replacing this brain drain will require a combination of short-term and long-term strategies. The best way for aerospace companies to address their long-term needs is to work at changing the way the millennial generation views manufacturing jobs. The task can be daunting.
Last year the National Society of High School Scholars published their annual survey of the “emerging workforce,” defined as millennials aged 15 to 26. Among the 18,000 young people questioned, Google, Walt Disney, St. Jude’s Children’s Hospital, Apple, and the FBI topped the list of the 100 preferred companies to work for. Lockheed Martin (#45) and Northrop Grumman (#87) were the only aerospace manufacturers to make the list.

Trade schools are another category for outreach. Skills for America’s Future, a non-profit founded by now-Secretary of Commerce Penny Pritzker, is a resource well known for helping foster partnerships between employers and community colleges. Other ways to connect with trade school students include certificate programs, scholarships, internships, and work-study programs. These kinds of initiatives not only create a natural pipeline for recruitment, but also connect employers with the best students.
A private survey conducted by Advanced Technology Services (ATS) and ACNielsen shows that 41 percent of all skilled tradesmen in the U.S. will retire by 2017.
Many aerospace employers overlook military veterans as potential hires. The armed forces provide a broad variety of technical training in avionics, hydraulics, computers, electronics, calibration, mechanical engineering, and other key disciplines. Transition counselors, the VA, and community colleges close to military bases are great ways to make connections with these highly skilled individuals.
Finally, company-sponsored talent management and development programs can also give existing workers the specific skills required for changing manufacturing needs. “Trade schools on wheels” are gaining in popularity precisely because they can deliver highly customized training at the hours that make sense for employees and employers alike. One of the best reasons for formal training and development plans for technicians is consistency; teams and work groups all receive the same information at the same time, tailored to the company’s culture and business objectives.
Strategic Sourcing
Long-term solutions are certainly a necessity, yet for a large number of aerospace manufacturers, the productivity needle needs to move now. For these firms, strategic sourcing may be the answer. Partnering with outside service providers is nothing new — most companies contract their janitorial and grounds maintenance duties. Today, however, options exist in IT, HR, and building maintenance, as well as critical manufacturing and logistics functions. These outside sources can not only deliver skills and best practices, but also cost savings over time since they are contractually required to perform.
To maximize production efficiency, companies are wise to ask themselves what services they can reasonably source externally. Machine maintenance is an often-overlooked area that has benefitted in recent years from huge advances in technology and strategy. Especially for facilities moving to lean manufacturing techniques, maintenance is a key issue — and one that specialists can improve significantly.
For any factory to perform, production equipment must run smoothly, efficiently, within tight standards, and without expensive downtime. So important is maintenance to profitable operation, in fact, that it helps to frame the issue not simply as maintenance but as an equipment reliability program — a term that much better captures its true value.
There are service providers today who offer a multitude of solutions for contract technical services; these include process/production asset maintenance, calibration management programs, and repairable part management programs that can allow manufacturers to focus their shrinking technical talent on more critical areas. These specialists also use mobile technology in the plant to improve technician utilization and reduce the time required for tasks like conducting technical documentation searches, locating and acquiring spare parts, and work planning and scheduling.
Predictive maintenance (PdM) is perhaps the most advanced offering in the machine maintenance arsenal. Research has shown that PdM, a condition-based approach to equipment reliability, can eliminate as much as 30 percent of all routine preventive tasks. These and other proactive equipment reliability programs have been shown to result in major cost reductions, with some manufacturers tracking savings as high as 80 percent. Furthermore, a proactive approach results in a reliable, more productive manufacturing environment upon which other process efficiencies can be built.
Programs like PdM, as well as other strategic sourcing options, talent development, recruitment, and outreach programs will all be needed to meet the skilled worker needs of the future. The loss of experienced employees, lack of qualified job candidates, and the combined challenges of multi-year commercial backlogs and declining defense spending make such solutions imperative.
Critical Challenges
As companies deal with these issues, upstream suppliers and producers may be hardest hit. The AIA reports that “while larger companies continue to mitigate the effects of the [U.S. government] budget environment by diversifying, seeking new markets, and downsizing, smaller companies in the defense industrial base are bearing the brunt of the funding side and face critical challenges to keeping their businesses viable.”
It’s clear that for aerospace firms to thrive in the years ahead, fresh thinking, new technologies, and alternative business models will be essential. Most importantly, decision-makers will need to take informed risks in their approaches to problem-solving. By putting innovation first, aerospace manufacturers can ensure that no matter what global turbulence affects the industry, they’ll have the resources to fly through to calmer, clearer, and more favorable skies.