While certain dynamics such as economic prosperity or recession, political unrest, fuel prices, and new technology will have some effect on short-term trends, this inevitability of the aggregate industry trend now requires aviation industry manufacturers and suppliers to gain a deeper understanding of the various factors associated in a location decision to increase or consolidate capacity.
Since 2009, the U.S. has announced roughly 500 aviation-related projects, valued at roughly $11 billion in investment and 53,000 jobs, an average of a little more than 100 jobs and $23 million in investment per project.
The site selection process of a large facility (roughly defined as over $100 million in CAPEX and hundreds of new jobs) will normally take a year or more and require a core project team comprised of a handful of key personnel. The time commitments of this team are primarily in addition to their normal job duties and, in almost all instances, will ultimately require several of the key team members to relocate to the new facility once chosen. However, more than 90 percent of the siting projects in the industry are not this size, but smaller. Since 2009, the U.S. has announced roughly 500 aviation-related projects, valued at roughly $11 billion in investment and 53,000 jobs, thereby making the average project size during this timeframe a little more than 100 jobs and $23 million in investment.
A Decision Analysis
A general framework for factors affecting the average size project can be defined by breaking the decision analysis into four main areas:
Physical site requirements — The overall analysis includes cost to develop the site to not only be “shovel-ready” but also “ready for project requirements.” While it should be fairly easy to calculate the cost of the real estate acquisition, the underlying costs associated with development of an actual site for a company’s particular needs may be exponentially greater.
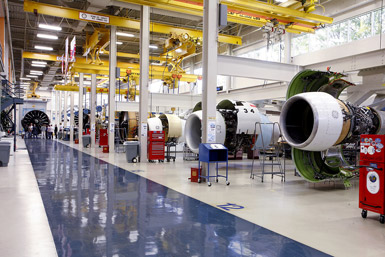
With this in mind, it is up to the project team to first determine total site prep costs based on items that are not simply limited to acreage needed, but also include the additional costs to make the site suitable for the development necessary for the project. While a particular parcel may have a purchase or lease cost identified, the team must also evaluate other costs. The team also needs to identify clearing, fill, and soil stabilization needs based on an actual, not perceived, layout, in addition to ancillary costs associated with identifying and removing encumbrances that may or may not have been identified, even with a single owner parcel, by an ALTA survey. Once these costs are determined, connectivity costs to connect to transportation and utility infrastructure must also be identified to determine total site costs.
It is in the best interest of the company to not attempt to receive or negotiate an incentive early on in the process, but rather to wait until all costs are evaluated, starting with the requirements of the physical site. A best practice state or local EDO will have funds available to help the company perform the due diligence, and have an in-house ombudsman with specific aviation industry experience to shepherd the project through its particular needs. In addition, the EDO should also be able to help identify creative ways that may or may not be in its normal incentive toolkit to help alleviate start-up costs, with recent real-life examples on how it has done this for partners the company is familiar with in its industry.
It is in the best interest of the company to not attempt to receive or negotiate an incentive early on in the process, but rather to wait until all costs are evaluated, starting with the requirements of the physical site.
Workforce and training support — A general rule of thumb is that, from an available workforce standpoint, a region can absorb a project that creates up to 1 percent of the existing industry workforce. While a myriad of factors can affect this general rule, once a company’s human resources professionals are comfortable with existing short-listed sites, it should consider other regional attributes that support development of a skilled labor pool.
For most regions, there are numbers of programs that can provide some support funds necessary to recruit, screen, and train a workforce to meet company needs. However, in many instances, these funds may not be managed by the economic developers, but rather educational institutions, departments of labor, or workforce investment boards. Several of these programs, however, are generally targeted to incumbent companies, rather than companies new to the region.
The most recent best practices adopted by several states — such as Georgia, Alabama, and Louisiana — have targeted programs that absorb most or all of the costs associated with development of the necessary skills, in addition to providing grants for specific aerospace training equipment needs, such as flight simulators, or dedicated space either on-site or at a local community college. For larger projects, development and funding for housing equipment purchases and staffing for university-led research, in collaboration with long-term cluster-based activities, can be made available. On occasion, the funds necessary for these endeavors can be utilized from existing public capital and educational programs; therefore, these can be considered by the company’s project team over and above the “offer” provided by the public economic development entities.
Long term incentive and tax structure — While it is commonplace to identify and determine the overall net present value of the total cost of operations for the project, it is quite another to identify risk or hidden opportunities associated with the state or region under consideration. Besides evaluating the long-term availability of incentives, a company should evaluate the potential to utilize programs that may be brand new and available but haven’t been used in a particular region, or perhaps can be modified to fit its particular project needs.
In undertaking an analysis of a project’s costs, the project team shouldn’t neglect to include the cost of living and lifestyle choices of a potential location. In addition to the states mentioned earlier, Florida, Mississippi, Colorado, Ohio, Missouri, Connecticut, Washington, and South Carolina have all passed recent legislation to support aviation-related projects. On the local level, several localities now have or are considering the capability to eliminate property taxes in perpetuity though various legal structures designed to promote development. Conversely, several states have either reduced state incentives and/or are facing impending fiscal situations in which they likely will have to reduce or even eliminate programs.
It is imperative of the project team to gain an understanding of not only the current availability of incentives, but also the sustainability of existing programs. An analysis of taxes and incentives in general, in addition to an analysis of a state’s historical trends and the impact of future large public fiscal notes associated with items such as retirement, transportation infrastructure needs, public education costs/performance, and healthcare costs as a percentage of the overall public financial budget should also be considered in the siting decision.
Quality of life and employee cost of living analysis — A company’s business is built upon ideas; ideas can only come from people so, therefore, people are a company’s greatest resource. Locating in an environment that can maximize employee discretionary spending — while concurrently providing a safe, healthy, and wide array of diverse social, sporting, recreational, and cultural activities — can be deemed as important as any overall tax and incentive environment offered by a state and local partnership. However, on many siting projects, this analysis is done after the corporate financial considerations are evaluated, or in some cases, not weighted heavily in the overall final decision, since these costs do not fit inside corporate financial statements or aren’t used in reporting corporate performance to financial markets.
In the United States, aggregate employee costs average between 65 percent and 70 percent of overall corporate costs. Since quality-of-life/cost-of-living analyses can be evaluated separate from site location costs, and are most likely evaluated by internal skillsets normally not included in the initial formation of the core project team, it is in the best interest of the overall project that this analysis be done in conjunction with, and as a core part of, the site analysis. Most importantly, the results of this analysis should be given enough weight that these factors alone can be the deciding factor once the overall corporate financial and risk analysis is performed.
A Long-Term Decision
If current trends continue, a conservative estimate reveals there will be more than 1,000 announcements of aviation-related projects in the United States over the next decade. The best location decisions will be made by project teams that not only look at the current overall costs, but also have a deep understanding of hidden site development costs, in addition to the long-term political/financial stability that can be provided in a region that allows the company’s employees to be happy and prosper. While there never will be a “perfect” site, by utilizing the criteria mentioned above, in addition to a sound overall project cost analysis, the project team will be well prepared to make the long-term generational decision for its organization.