Workforce Development Issues in a Changing Automotive Industry
Automotive Site Guide 2012
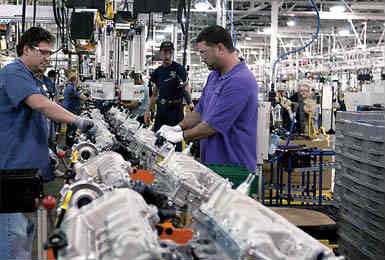
One component, in particular, that is being impacted is the workforce. More sophisticated processes mean a greater degree of understanding and technical skills than in the past. Rapid changes in both product development and assembly processes require a level of flexibility and teamwork that is constantly evolving. Even new materials such as carbon fiber, stamped aluminum, and the introduction of other lightweight metals introduce an element of craftsmanship - in conjunction with increased technical skills - that warrants a different type of worker associate.
As the automotive industry evolves, so will its need for a more skilled and productive workforce, for both incumbents and new plant startups. The investigations into what constitutes a highly competitive and productive workforce that can meet the long-term needs of the manufacturer require analysis at multiple levels.
Supply Side Analysis/Available Skills
The first step in understanding workforce in a given area is to create a demographic profile of the region that describes the general characteristics of the prospect location. An OEM typically seeks a metro region with a population exceeding 250,000. On the other hand, the size of communities sought by suppliers depends on the complexity of the component manufactured and the skill levels required to assemble it - as well as the company's willingness to train the existing workforce. PACCAR is currently assembling engines in Columbus, Mississippi, in a community of almost 25,000, while Toyota and Navistar are assembling engines in Huntsville, Alabama, in a community that has a population of just over 180,000 - two totally different workforce development strategies.
Once the demographic information is prepared, it is then necessary to disaggregate this information into workforce characteristics by job classifications, particularly as they relate to the manufacturing sector, in order to assess potential skills availability. The U.S. Bureau of Labor Statistics can provide this information by job classification as well as wages for both counties and metropolitan regions.
Next, it is essential to understand the types of companies and the products manufactured, as well as whether they are competitors or not. A review of this information will provide a basic understanding of availability and cost. Further investigations through interviews and primary data sources will provide much greater granularity and precision.
Of course, it is important to understand where the company's workforce development strategy is focused to make the best of this data. If there is a need to recruit and hire a highly skilled workforce capable of manufacturing to specific levels with minimum levels of training, then gravitating to areas where similar manufacturing operations occur is a possible path. In contrast, if the schedule allows the time necessary to train the workforce, then a greater emphasis could be placed on underemployment and trainability - which favors a smaller metropolitan region. In either case, the company's culture and skills will be a critically important part of the workforce development strategy. Integrating strategy and execution when recruiting, screening, hiring, and training the workforce is a fundamental step in the success of the enterprise.1
Startup Training/Filling the Gap
There are two approaches to workforce development, and it's helpful to understand which approach is being emphasized in the area of interest. One approach is place-based and attempts to address the needs of people who live in the region. It considers the supply side of the equation and is primarily focused on the characteristics of people in the region or community where the training program will be located. In essence, its intent is to help workers prepare for gainful employment. The other approach is sector-based and focuses on matching workers' skills to meet the needs of an industry already in the region - or one that could be recruited. Thus, the former focuses on the deficiencies of the particular workforce in question and attempts to improve the overall level of opportunity from the perspective of the workforce applicant, while the latter attempts to develop the skills that industry in the region needs.
It is important to know which type of workforce development the area of interest is promoting. While the place-based approach is laudable in that it helps the citizenry of the region, if there is not a match for prospective industries considering the area of interest, it provides little help for the company engaged in site selection - although there are exceptions. And even the sector-based approach misses the mark unless there is a match for the skills development programs that are ongoing. A rational mix of the two approaches that proactively addresses the needs of the citizenry but is flexible enough to respond to recruitment opportunities is the best strategy.
As mentioned previously, the company's hiring and recruitment strategy is an integral part of assessing the inherent capabilities of the regional workforce as they relate to training. For many companies, the sheer scope of the undertaking is taxing from both an economic and available resource standpoint. Many companies look to the local community and state to assist in workforce development; however, not all states and communities are created equal.
In some locations the entire spectrum of recruitment, screening, and training is provided free of charge. Naturally, the economic impact of the project to the respective location will determine how much post-employment training is provided and for how long; nevertheless, it is important to fully explore the opportunities that are available and appreciate the impact they can have on the company's bottom line. Care should be taken to fully understand what is being offered and what restrictions, if any, are being imposed. In general, those programs that have federal funding involved will be more restrictive on the use of funds. Aggressive state training programs, on the other hand, have little, if any, restrictions on employment offerings to prospective workers.
Educational Infrastructure/Building the Pipeline
The route to employment, as a student progresses from high school to postsecondary education, should provide multiple pathways for success. When considering a prospective location the company should first look at K-12 education, particularly at the high school level, to determine whether there is a program that inspires students' interest in science, technology, engineering, and math (STEM). Is it a meaningful program that tries to attract students early and feed their interest in manufacturing - or is it simply a fulfillment of federal program requirements for funding? In addition, it is also enlightening to investigate how supportive the region is of education in general by examining the tax rolls and the ease (or difficulty) with which adequate funding for education is maintained (or raised as needed). In addition, do the NAM-endorsed Manufacturing Skills Certification System credentials or any certificates commonly recognized in the industry have a place in these K-12 programs that feed into either manufacturing employment or postsecondary education? Finally, is there a spirit of cooperation that encourages close cooperation between industry and academia?
Community colleges play an increasingly critical role in the recipe for success by aligning their curricula to the skills that manufacturers need. Four-year universities have an important role in preparing a competitive manufacturing workforce as well. Do the community colleges and universities have a collaborative relationship with the private sector, or do they totally disassociate themselves from the local, regional, and state economy? Another question worth asking is whether there is a system that encourages enrollment in college and that takes full advantage of technology-driven instruction, providing more than one pathway to higher education. A prominent example used by many communities is the "School-to-Work" program where students can receive college credit while in high school performing apprenticeships, internships, or taking classes at the local community college.
Next: Life-Long Learning/ Continuous Skills Development
Project Announcements
Mutares Plans Auburn Hills, Michigan, Manufacturing Operations
08/01/2025
British-Based McLaren Plans Baltimore, Maryland, Vehicle Processing Operations
08/01/2025
Adient Plans Normal, Illinois, Production Operations
07/29/2025
Sumitomo Electric Wiring Systems Plans Simpson County, Kentucky, Manufacturing Operations
07/10/2025
TMG & Haartz Solutions Plans Bostic, North Carolina, Manufacturing Operations
07/02/2025
Torc Robotics Plans Ann Arbor, Michigan, Engineering Operations
06/27/2025
Most Read
-
What We’re Getting Wrong About Gen Z’s Future in the Skilled Trades
Q3 2025
-
A New Course for U.S. Shipbuilding
Q3 2025
-
Optimizing Your Rail-Served Transportation Network: Strategy Before Steel
Q2 2025
-
In Focus: AI Is Changing Incentives Math
Q2 2025
-
How to Choose the Right Site for Your Factory in 2025’s Volatile Landscape
Q2 2025
-
Reshoring Reality Check from Construction
Q3 2025
-
20th Annual Area Development Gold and Silver Shovel Awards
Q2 2025