It’s no surprise that transportation equipment output is heavily dependent on economic conditions, federal contracts, and hot sectors with an obvious transportation need (for example, shipping oil from North Dakota by rail).
The U.S. industry is highly concentrated — about 50 large manufacturers produce about three-quarters of all transportation equipment revenue. Motor vehicles and parts account for 65 percent of the total revenue, followed by aviation/aerospace (25 percent), rail (about 5 percent), and ships (about 5 percent). Top manufacturing states include California, Michigan, Indiana, and Texas.
To date, most of this equipment is sold to highly industrialized countries with well-developed economies in North America and Europe. New markets, however, are starting to emerge in rapidly developing countries that have a strong need to deliver freight. The American Trucking Association’s (ATA) U.S. Freight Forecast to 2024 predicts an overall increase in freight volumes for all modes of more than 20 percent — much of that will be moved by truck. Another encouraging sign: U.S. durable goods manufacturers’ shipments of transportation equipment, an indicator of transportation equipment production, rose 4.5 percent year- to-date in January 2014 — proving that the transportation manufacturing industry is on the move.
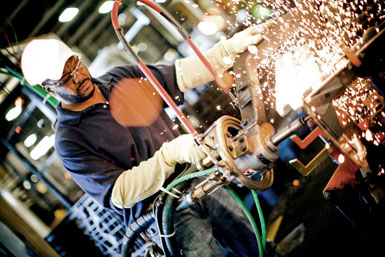
According to the International Organization of Motor Vehicle Manufacturers (OICA), the U.S. automotive industry grew 6.9 percent in 2013 — one of the strongest gains in the world (only Spain, Romania, Indonesia, Brazil, and Austria were higher). U.S. sales reached 15.6 million cars in 2013, up 7.6 percent compared to 2012. Much of this manufacturing growth is located in the southeastern United States.
“Kia, Hyundai, Porsche, BMW, Volkswagen, Toyota, and Mercedes are continuing to bring jobs into the Southeast,” says Adam Beckerman, partner-in-charge of the Manufacturing and Distribution Group for Habif Arogeti & Wynne LLP, an accounting and business consulting firm. “This region offers a friendly business environment, good transportation hubs, favorable climate, and skilled workforce.”
Tennessee is a good example: General Motors, Nissan North America, and Volkswagen Group of America all have major operations here and are supported by more than 1,000 suppliers and related businesses. “About 100,000 Tennesseans are employed in auto manufacturing jobs,” says Tom Brewer, president of the Tennessee Automotive Manufacturers Association. “In 2013, Tennessee announced the addition of 7,661 new automotive industry jobs, three new site locations, $1.7 billion in planned investments, and 43 site expansions.”
Interestingly, Mexico also showed solid growth of 1.7 percent in 2013. In fact, IHS Automotive projects that by 2020 Mexico will have the capacity to build one in every four vehicles in North America. Bloomberg reports that Mexico’s automotive industry is expected to reach 1.69 million cars in 2014, making it the second-largest provider of cars to the U.S., surpassing Japan and trailing only Canada. Truck manufacturing is also on the rise. According to the ATA, nearly 70 percent of all freight tonnage in the U.S. is moved by truck. Shipping nearly nine billion tons of freight annually requires about three million heavy duty Class-8 trucks.
Key drivers for improved truck sales are increased manufacturing output of consumer goods and the growing need for trucks in emerging countries. In addition, “the average age of fleet vehicles is still fairly high,” states Robert Woodall, director of Sales and Marketing for Peterbilt Motors Company. “As economic conditions improve and freight strengthens, fleets should begin replacing older equipment with new trucks, and even add capacity to their operations.”
Signs of growth are already evident. For example, Volvo Group North America’s heavy-duty truck deliveries jumped 55 percent in February 2014 from a year ago; worldwide heavy duty truck deliveries for all Volvo brands rose 35 percent.
Trailer orders also got off to a hot start in January, surging 28 percent year-over-year, according to ACT Research Company (ACT). “Seven of the 10 trailer categories showed year over- year growth in January,” says Frank Maly, ACT’s director of Transportation Analysis & Research.
Wabash National Corporation, a leading manufacturer of truck trailers, is helping its trucking customers improve efficiency and reduce fleet costs. “We are focusing on improving fuel economy through trailer aerodynamic devices,” says Dick Giromini, president and CEO. “As an industry, we must continue to identify and develop lightweight, high-strength materials to further reduce truck and trailer weights and improve fuel efficiency.”
Aviation and Aerospace
The U.S. aerospace and defense industry has been dealing with some tough challenges — including sequestration and reduced military contracts. Sales were about the same ($220 billion) in 2012 and 2013. According to the Aerospace Industries Association, even with these economic pressures, U.S. aerospace exports grew in 2013 — especially for civil aircraft. A top performer in this category is Bombardier, which recently closed a $5.2 billion deal for 245 business jets. Strong sales like these have allowed the company to invest billions of dollars in R&D over the last several years.
Any successful manufacturing cluster relies on close collaboration between OEMs and critical vendors and suppliers. South Carolina, for example, has more than 200 aerospace companies, anchored by Boeing’s North Charleston aircraft manufacturing plant. Recently, Toray Industries, a key supplier for Boeing, announced it would build a $1 billion facility in Spartanburg County. It will manufacture carbon fiber composites and other advanced materials for Boeing aircraft. The project represents one of the largest initial capital investments in South Carolina’s history — “a real game-changer for the Upstate and all of South Carolina,” says Governor Nikki Haley.
Aerospace manufacturing often struggles to meet order deadlines, in part because of cumbersome supply chains. Improved performance, according to Accenture, a management consulting firm, is better integration across the supply chain and managing the efficiency of the full process, from design through delivery. “As aerospace supply chains become more diverse, with additional partners involved beyond the original equipment manufacturers, digital integration of the supply chain is going to be a critical differentiator in performance,” explains Accenture Senior Manager Craig Gottlieb.
The global transportation equipment manufacturing industry generates about $4 trillion in annual revenues — $750 billion of that coming
from the U.S.
Railroads
Rail equipment manufacturers sell to Class-I railroads and railroad leasing companies, which in turn ship industrial products, including heavy machinery, coal, timber, oil, and coal. As the economy recovers, and demand for rail transportation and equipment continues to rise, railroads are investing millions of dollars in track and equipment upgrades.
One of the greatest boons to railcar manufacturing is the urgent need for transporting oil from the shale plays in Texas and North Dakota. Tank cars currently comprise about 84 percent of the backlogs for rail cars — a reflection of the huge influence of oil production.
“The demand for oil by rail, along with the safety issues, is having an impact on the design of tank cars and their short-term demand,” says Ben Chapman, assistant vice president for Norfolk Southern. “The federal mandate for PTC (Positive Train Control) continues to require a large capital investment for our signaling system and interoperability with the locomotives. Norfolk Southern continues to reinvest in its freight car and locomotive fleet to ensure we can meet the projected demands of our customers,” continues Chapman. “In 2014, we expect to invest more than $575 million in equipment upgrades and purchases. Locomotive suppliers are also testing natural gas locomotives powered by liquefied natural gas.”
Passenger cars are also in demand. A recent RailwayAge survey showed that 1,175 passenger cars were delivered in 2013, with an existing backlog of 5,167 cars — a number that has steadily climbed in recent years. Orders for another 2,600 cars are expected to be placed in 2014. “Big transit agencies, such as the New York City MTA, the Chicago Transit Authority, San Francisco’s BART, the Toronto Transit Commission (TTC), and Washington’s Metropolitan Area Transit Authority (WMATA) were in the midst of big-number deliveries for their respective rapid transit systems,” states RailwayAge. Rapid-transit newcomers like Miami-Dade Transit and Honolulu’s Authority for Rapid Transportation (HART) are also expecting new equipment in 2014.
Locomotive and railroad equipment manufacturers are also looking overseas for growth opportunities — especially in China. “Emerging economies are growing at much faster rates than western economies, presenting potential markets for the industry,” says IBISWorld industry analyst Lauren Setar. She indicates these shifts to emerging economies should boost U.S. industry growth prospects over the next five years.
Shipbuilding
The federal government is the largest buyer of U.S.-built military ships. U.S. shipyards also build ships for fishing fleets, cruise lines, barge operators, and cargo-shipping companies. More than 40,000 vessels transport more than one billion tons of cargo in the U.S. every year, with a total market value of $400 billion.
A 2013 report by the U.S. Department of Transportation’s Maritime Administration (MARAD), using 2011 data, indicated that U.S. shipyards support $36 billion in gross domestic product. About 60 percent of that revenue comes from military shipbuilding and 22 percent from commercial shipbuilding. The top five states for shipbuilding are Virginia, California, Louisiana, Texas, and Mississippi — other shipyards are located along the Great Lakes and the Mississippi and Ohio rivers.
Just as it has stimulated growth in the rail sector, oil from booming oil shale reservoirs across the country has created a manufacturing rush for big oil tankers to transport oil to refineries. Currently more than one dozen oil tankers and hundreds of smaller tugs and barges are on order at U.S. shipyards.
For example, Aker Philadelphia Shipyard (APSI) is currently constructing two 115,000-deadweight-ton (dwt) crude oil carriers for SeaRiver Maritime, a subsidiary of ExxonMobil. The shipyard has also started building multiple tankers for Crowley Maritime Corporation, with a total contract value of approximately $500 million. When completed in 2015, the first Crowley vessel will be 600 feet long and capable of carrying 50,000 tons of crude oil or refined petroleum products.
“We are excited to partner with Crowley to provide long-term transportation options for the growing U.S. petroleum market,” says Kristian Rokke, president and CEO of APSI. “We have a strong history of building similar product tankers, which are all playing a fundamental role in moving our nation’s energy.”