Such robots, so far at least, are the stuff of science fiction. The reality of robotics is something altogether different. And the impact they are starting to have in supply-chain logistics is just now being felt. Why? Because up until just recently, robots were expensive, hard to teach, blind, stationary, and commanded only the most rudimentary intelligence. But that archetype is rapidly changing, and the impact they will have on logistics networks could be profound.
Robotics in Action
Two years ago, I finished up a construction project with one of our global accounts. In this case, the client needed to build a 350,000-square-foot, -20 degrees Fahrenheit freezer to serve as a distribution center for the ice cream it produces at the same site. As you might imagine, building such a facility is both complex and costly. And while there were many firsts for me on that assignment, the one most relevant to this article was the use of two robotic technologies: (1) Automated Guided Vehicles (AGVs) and (2) Swiss Log’s PowerStore and Pallet Shuttle systems.
In summary, as finished product comes off the line, it is boxed, palletized, wrapped in plastic, then moved — all using automation — and placed on one of two AGVs. These devices, roughly five feet wide and eight feet long, transport the product roughly 50 feet to an induction lift, which starts the product on its way into the freezer. The AGVs have sensors all around them and know to stop if a human or other obstruction is in the way. In addition, they know to automatically return to their wireless charging station when they get tired, know how much product is coming their way, and know how to plan their work accordingly. No, they are not fluent in over six millions languages like the Star Wars’ character C-3PO, but they never need an oil bath and don’t complain as often as he did either.
Then once in the warehouse (and remember, it’s -20 in there!), the PowerStore and Pallet Shuttle systems take the pallets and carefully place them into the racking for storage and later shipping. Could humans do these things? Sure. In fact, recent studies show that roughly 80 percent of current distribution centers/warehouses operate today with no automation at all. Just a bunch of people chasing product, driving fork trucks, and manually filling bins. But keep in mind, unlike their carbon-based cousins, robots don’t get sick, they never miss a shift because the bus was late or their car wouldn’t start, don’t go on strike, don’t have kids in daycare they need to go get, etc. So there are clear benefits to using automation, assuming the business case is there. And that business case is getting easier to make.
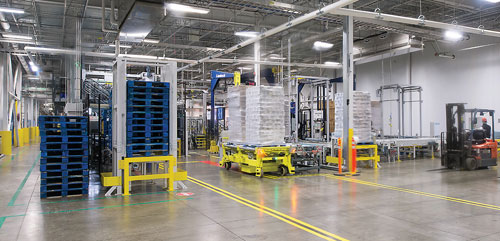
Currently, the sort of robotic technology mentioned above would be expected in both manufacturing and distribution settings. But can advanced technology impact decisions about where to set up shop? Consider the following data a colleague in the logistics industry shared with me. He said, regarding labor in the logistic food chain:
- 1980: 100 percent humans, 0 percent robots
- 2010: 80 percent humans, 20 percent robots
- 2020: 20 percent humans, 80 percent robots
For now, the important point to keep in mind is this: as economies grow, more workers are needed. Basic economics, right? But the population in the western world is shrinking. Add to that the ambitions of the millennial generation and it’s easy to understand why finding people willing to work in a distribution center (DC) or factory is an extremely difficult challenge.
Robotics will continue to evolve in both agility and intelligence while reducing in cost. When Cushman & Wakefield site selection consultants help our clients find the ideal location for their factory or distribution center, one of the key metrics they use is a demographic study. Why is that important? Because the demographic study helps our clients understand the composition of a potential workforce in a given area. This is then used to help determine the potential pool of workers who might be willing to work in their DC and how much those workers will cost.
There are a number of reasons you don’t see DCs or factories in cities like Manhattan or San Francisco. Two of the most important factors are land costs and labor costs. But imagine for a minute what it would mean to a given manufacturer if, instead of trying to hire and retain hourly labor in a third-tier market, they could instead make a one-time capital spend on robotic technology. In such a case, the only true “employees” would be the facilities people and engineers needed to train and keep said robots operating. Would that be a material change to the location dynamics? Industry consensus suggests it will.
The e-Commerce Effect
There is another key trend that is also causing those involved in logistics to lose sleep and to question anew their logistics network strategy: e-Commerce.
Not long ago, retailers shipped their goods by the pallet load. Not anymore. Instead, the growing trend on the part of consumers to order their goods online necessarily means logistics networks are working with “eaches,” which are an expensive proposition for most retailers.
Add to that the ambitions of the millennial generation and it’s easy to understand why finding people willing to work in a distribution center (DC) or factory is an extremely difficult challenge. Consider the following: A global, well-known brand is spending millions of dollars to evolve their existing DCs into omni-channel fulfillment centers to address this very need. They say it is not at all unusual for their customers to order three sizes of the very same shoes. So in their DC, their workers pick those three shoeboxes and send them through a sorter where they will eventually land at a shipping station. And, if all goes right, a few days later they show up at the customer’s address. He or she tries on the shoes, picks the one pair that fits the best, and sends back the two that don’t. Is this a problem? For the consumer, it is not. But for the online retailer it’s a nightmare. For generations their logistics networks all flowed one way: from factory to retailer to customer. But now, there is a huge and ever-growing reverse network needed for returns.
Rather than shoes, this time imagine the retailer sells women’s blouses. They ship three identical blouses to their customer’s home, she tries all three, keeps the one that fits best and sends the others back. But now, the retailer needs to repackage and restock the two blouses their customer did not want. When done, the blouses both need to look never-before-worn so they can be shipped to the next customer who also orders three different sizes. The labor associated with this new paradigm is a huge issue for almost all retailers and is one they all are grappling to solve.
What’s Coming?
So with all this in mind, let’s peek around the corner just a little bit for a glimpse of what most see coming. First, robotics will continue to evolve in both agility and intelligence while reducing in cost. This will enable the robots to perform routine, repetitive work done in DCs and manufacturing plants while freeing up human capital to handle the more complex tasks. This will mean DCs will need fewer, but smarter and more highly compensated people.
At a recent presentation, there was a panel of speakers, all of whom were industrial-focused developers. One of the speakers said, “The easy sites are gone.” And the others on the panel agreed. But what if you take the availability of labor outside the location equation? Does that open a whole new set of possible sites? Is there a day coming when DCs will be predominantly automated? Many think it will. And when that happens, the human workforce at that site will be relegated to folding and repackaging your returns. But only until robots are trained to do that, too.