These highly flexible, technologically advanced shops are small by industrial real estate standards, seldom occupying more than 10,000 square feet. Nonetheless, their presence is partially responsible for the resurgence of U.S. manufacturing output over the past decade, providing a necessary link in the development of electric sports cars, military-grade drones, consumer electronics. and other cutting-edge products.
To understand maker-tech companies and the real estate that best serves them, it helps to have an appreciation for the way high-speed data connectivity and additive manufacturing or 3-D printing have slashed time-to-market expectations and disrupted traditional product-development practices.
Fewer People, More Output
U.S. factories reached peak employment at 19.4 million jobs in 1979 before a gradual decline that accelerated after 2000. Manufacturing as a share of the overall workforce, however, had been dropping since the end of the Korean War. Almost one in three Americans, or 32.1 percent of the working population, held manufacturing jobs in 1953, compared with 8.5 percent of workers today, according to the Bureau of Labor Statistics.
However, manufacturers are hiring. The sector’s job count of 12.6 million in February 2018 was up by more than one million from early 2010, when manufacturing employment reached a historic low following the Great Recession. But the percentage of factory jobs relative to the overall economy has remained static in recent years, and job growth in other sectors has far overshadowed manufacturing employment gains in the past decade.
Productivity is a different story. While manufacturing output in some industries including textiles, apparel, and leather goods has declined precipitously since the late 20th century, output has shown healthy growth in aerospace, fabricated metal products, machinery, motor vehicles and parts, and computers and electronics. Overall manufacturing output increased 42 percent from 1987 to 2008, when it contracted during the Great Recession. By the end of 2017, output had recovered the ground lost in the recession, and it continues to increase.
In other words, U.S. factories are relying on automation and robots to produce more and higher-value goods. While they are accomplishing this with fewer workers, they now must seek out labor possessing the necessary education and skills to maintain and repair automated equipment.
The emphasis for many U.S. manufacturers today is generating profits through responsiveness to ever-shifting consumer preferences or industrial requirements, and speed-to-market with new or modified items catering to those needs. This runs contrary to the idea of competing for sales and profit by achieving the lowest cost, which was the principal force behind offshoring the manufacture of many household and personal goods in years past.
Harnessing Maker-Tech for Strategic Advantage
In many industries, the time-tested model of rolling out a product, collecting user feedback, and introducing a few improvements in the next year’s model has become too slow and cumbersome to retain a company’s market share. The faster a manufacturer can incorporate improvements, the better its chances to capture sales while the iron is hot.
A manufacturer of limited-production automobiles, for example, may surround its assembly plant with suppliers within a half-day’s drive, and many of those providers will fall under the maker-tech umbrella. When the central company’s engineers want to improve a car part such as a motor bracket, they may transmit their design to an advanced manufacturing firm capable of producing the part. After working out details of the new component with engineers, the supplier may use a form of 3-D printing to mock up a plastic version of the bracket and have it delivered to the client on the same day.
Once the automaker confirms that the design fits its requirements, a metal fabrication shop — which may be part of the same firm that produced the plastic mock-up — can machine a working version of the bracket out of steel, aluminum, or even an advanced composite and ship that to the customer for testing. After testing, the same producer can make necessary adjustments and either transmit the design and a finished sample to a small-batch manufacturer or produce the new parts in volume on a flexible manufacturing line.
This example shows that multidisciplinary industrial providers help speed the innovation process to deliver a final product in a matter of weeks or even days. Compare that to the months that were once required to ship designs and prototypes to distant manufacturers, design and outfit production lines, and make and then ship a final product. Even if the end goal is mass production at a dedicated manufacturing site, a dynamic maker-tech shop can reduce the time required to begin production.
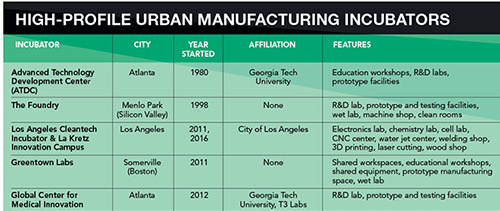
SOURCE: Transwestern
Maker-tech firms often work as problem-solvers for larger organizations, and therefore must be accessible to the clients and potential clients they plan to service. They may form clusters or ecosystems around a major employer, such as an automaker, or around a regionally dominant industry, such as oil and gas.
A good rule of thumb is to focus site selection in submarkets within a four-hour drive of suppliers and clients or prospects. Potential sites should offer easy highway access and proximity to an airport within a one-hour drive, if not closer.
Labor is a critical factor in site selection and a challenge in many markets. Like a software provider or electronics designer, maker-tech firms need a ready supply of skilled labor. But unlike more siloed employers, a single advanced manufacturer may require experts in software, hardware, machining, welding, and assorted fabrication methods, as well as a reliable source of new workers to replace those who move on. Even if the company doesn’t employ those specialists directly, it may need working relationships with nearby firms that can provide those skills.
Hence, the site search must identify skilled labor pools continually replenished by area universities and trade schools. This will narrow the list of options to communities with existing brain clusters serving the targeted industry. These thriving hubs exist in only a handful of major U.S. markets, with examples including the San Francisco Bay Area, Boston, New York, and Atlanta.
Buildings must offer excellent power and gas service and a robust shell. Advanced manufacturers are unlikely to choose low-cost locations off the beaten path because the disadvantages of accessing a remote facility will outweigh any benefits to be gained in the form of below-market rent.
Maker-tech firms often work as problem-solvers for larger organizations, and therefore must be accessible to the clients and potential clients they plan to service. Standard ethernet broadband access may be inadequate for firms that need to rapidly transmit massive design files and supporting data. For those users, properties with access to dark fiber may offer a solution. Dark fiber is unused fiberoptic cabling that many telecommunications providers now install alongside their lines for future use, which can sometimes be leased or purchased for exclusive use as part of a fast and secure wide area network. At a minimum, maker-tech firms will seek the highest commercially available bandwidth to the site.
Building out a space for an advanced manufacturer may cost $50 to $100 per square foot, compared to about $20 per square foot for more traditional manufacturing. This reflects the variety of activities it may expect to perform in the building, from computer-aided design in an office setting to welding and machining in the next room or a building nearby. The particular use may require advanced mechanicals to heat and cool the space as well as equipment. Some operations will require specific fire-suppression systems or elaborate plumbing work.
Office, industrial, and even retail activities taking place at the same property are not only unusual by traditional real estate standards, they may also clash with longstanding zoning rules in some communities. In-place zoning may preclude some usage combinations and require rezoning or a special designation to serve the manufacturer’s needs.
A few progressive municipalities have recognized the importance of maker-tech space and accommodate its existence through local ordinances. Options can include building-by-building zoning or sub-zoning areas within a single structure for various uses. Special zoning may become less of a concern over time, however, as more communities come to recognize the vital role that maker-tech plays in product development and manufacturing.