Restarting Delayed Capital Projects
A collaborative approach to re-evaluation of delayed capital projects is in everyone’s best interest.
Q4 2020
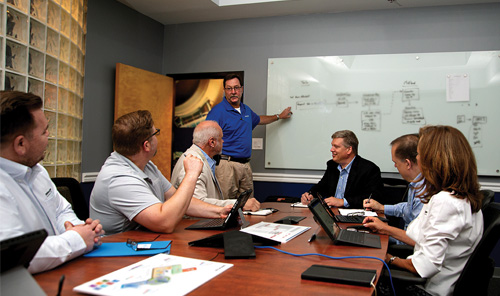
A study conducted by Independent Project Analysis (IPA) in spring 2020 revealed that 76 percent of companies surveyed were “planning to delay projects due to the COVID-19 pandemic’s effects.” Moreover, respondents said, on average, that they had suspended approximately 15 to 20 percent of their projects with anticipated suspension times lasting for at least 10 to 20 weeks.
With those suspension periods now largely drawing to a close, companies must decide how — and if — to resume their delayed projects. IPA concludes from its research that “projects stopped and restarted in execution incur 4 percent greater cost growth than projects that continued uninterrupted, and projects stopped and recommenced during construction experience 11 percent more cost growth compared to projects that halt and resume in the middle of detailed engineering.”
To mitigate losses, owners must carefully re-evaluate the factors that will determine a project’s success. Previous plans, facility requirements, safety approaches, supply chains, workforce availability, schedules, benchmarks, and more should all be assessed and reconsidered.
Communication, Collaboration, Flexibility: The Underpinnings
The stakes are high when restarting a delayed project, and additional action steps are required beyond those taken during typical capital project execution. This is no small demand, considering that “typical” capital projects are already complex. Despite the added complications of a resumed project, the underpinnings of success are the same: communication, collaboration, rigorous data analysis, and flexibility.
Project stakeholders from all sides must work together. While anxieties spurred by the economic and health crises could understandably provoke quick reactions, causing firms to conservatively address risks and protect their own interests, in fact it is more imperative than ever to function as a team, gather as much upfront information as possible, and follow through with systematic deployment. Capital costs that were assessed at project outset should be revisited.
This includes engaging contractors early in the re-evaluation process. By applying the principles of early contractor involvement, or ECI, contractors and owners can achieve greater certainty in terms of estimation/cost, project planning, safety, communication, constructability, and risk management. This approach also reduces errors and changes in later project phases.
Action Steps for Re-Evaluating Delayed Projects
The first question the team should ask is, does the project still meet the business’s needs, considering that market factors may have shifted? If anything, the COVID-19 pandemic accelerated market shifts based on behaviors of consumers and businesses. This has impacted how customers find, select, purchase, and receive products. A key step in re-evaluating delayed projects is assessing the market drivers in specific industry segments and how disruptions or shifts will impact demand. More important, these shifts will impact how industrial facilities are utilized.
Fundamental tradeoffs may need to be made between cost and schedule as new goals and timelines are assessed and negotiated. Make sure the team understands how cost or schedule will be impacted by new safety and COVID procedures. While added safety protocols on active job sites have slowed the overall pace of work in order to accommodate new social-distancing norms, project teams must maintain the perspective that a lack of stringent site safety protocols could lead to far lengthier site closures due to mass infection among craft personnel, or loss of key management assets.
Capital costs that were assessed at project outset should be revisited. Costs for contractors, labor, materials, critical process equipment, fabrication, and more may have changed. Supply chains and lead times for materials and equipment may have also been dramatically affected by the pandemic. Owners and project representatives should communicate with all contractors, suppliers, and vendors one-on-one, confirming that they are still available to handle the project and re-examining variables. Identify, for example, scheduling issues such as whether any milestones have been missed.
It is also important to assess where contracts and financials stand, including construction work that has been completed and/or paid for. Performing a site assessment is critical for viewing construction status first-hand. Additionally, the team should re-assess where the project stands with regard to permitting.
When construction is resumed, the team should not expect business-as-usual on the job site. The pandemic and economic challenges have impacted numerous contractors in different ways. Before restarting a project, owners should review and address the previously selected contractors to verify their availability and financial stability. Changes in the project scope and schedule could impact the proposed project team. As many contractors have downsized, key members of the project team may no longer be available. Craft availability continues to be a critical challenge, as regional labor pools are subject to myriad state and local regulations pertaining to COVID (travel, lodging, etc.), potentially impairing a contractor’s ability to ramp up to meet schedule commitments in a timely manner.
New contract terms and conditions, as well as project documentation, may be required to address COVID-19-related liability. A re-examination of all parties’ insurance policies and coverage is advisable. Additionally, in upcoming months, firms would do well to watch court decisions that are being handed down interpreting a previously little-used contract clause known as force majeure (defined as unforeseeable circumstances that prevent someone from fulfilling a contract). These court decisions will determine the extent to which the pandemic will be considered a force majeure event that mitigates some contractual obligations.
When construction has resumed, the team should not expect business-as-usual on the job site. Experts predict that restrictions will be lifted gradually, probably with inconsistencies between geographic areas and possibly with some new waves of lockdowns and disruptions. To the extent possible, these changes should be enumerated and planned for during the project re-evaluation stage.
For example, social distancing, sanitizing, disinfecting, and cleaning requirements will certainly require new provisions in place for job-site safety and may reduce job-site productivity. Safety managers will need to include training and screenings for their safety programs and site-specific plans. Site security measures should be ready to put into place should the site experience another full shutdown.
Maintaining flexibility and adaptability is critical; while it is impossible to foresee exactly what will affect the project as time goes on, multiple “if/then” scenarios can be established and accommodated. Perform cost-benefit analyses that can be used in the event of new slowdowns to inform which aspects of the project should be fully stopped and which can be merely slowed.
New contract terms and conditions may be required to address COVID-10 related liability. Standard workflows should be reexamined to see where efficiencies can be gained — with efficiencies being defined not only according to traditional measures, but also keeping in mind new kinds of costs imposed by social distancing and the like. For example, there may be an opportunity for off-site assembly or prefabricated components to eliminate job-site congestion and tighten the construction schedule. Similarly, now is a good time to fully leverage cloud-based solutions and remote collaboration platforms.
Even after construction has resumed, the team should continue to track all of the indicators it used when assessing the project for restart, because the availability and stability of resources may continue to fluctuate. For example, supply lines may remain unpredictable, companies may see spikes in worker absenteeism, and financially challenged contractor companies may continue to experience staffing changes. A successful project outcome will depend on the team performing ongoing risk assessment and management, considering the likelihood a given scenario will play out and paying special attention to scenarios that would have the most severe impact.
Now more than ever, a collaborative approach to project planning, including the re-evaluation of delayed capital projects, is in everyone’s best interest. Working together on data collection and analysis, risk management and more will help teams fully understand the new challenges brought about by COVID-19 — and will help them meet those challenges.
Project Announcements
Alltech Expands Jessamine County, Kentucky, Manufacturing Operations
07/30/2025
Liatris Expands Rockville, Maryland, Manufacturing Operations
07/30/2025
China-Based Eco King Solutions Plans Robbinsville, North Carolina, Production Operations
07/30/2025
Hood Container Upgrades West Feliciana Parish, Louisiana, Operations
07/29/2025
MR6 Tech Services Plans Huguley, Alabama, Manufacturing Operations
07/29/2025
Adient Plans Normal, Illinois, Production Operations
07/29/2025
Most Read
-
20th Annual Area Development Gold and Silver Shovel Awards
Q2 2025
-
In Focus: AI Is Changing Incentives Math
Q2 2025
-
Optimizing Your Rail-Served Transportation Network: Strategy Before Steel
Q2 2025
-
How to Choose the Right Site for Your Factory in 2025’s Volatile Landscape
Q2 2025
-
From Silicon to Server: Mapping the Data Center Supply Chain
Q2 2025
-
Tariffs, Talent, and U.S. Expansion
Q3 2025
-
First Person: David Robey, Co-CEO of QTS Data Centers
Q2 2025