Labor Trumps Other Factors in the Location Decision
Is the decision to relocate an operation from a community realistic - or just an attempt to receive benefits or incentives to remain?
June/July 10
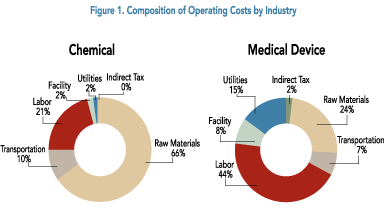
Such ratings are consistent with Jones Lang LaSalle's experience when helping guide companies to location decisions. Labor is typically rated highly for a number of reasons, including the significance of labor as one of the largest geographically variable costs, the impact of labor quality on plant productivity and output, and the constraints imposed on operations should labor not be available in appropriate volume and/or skill. These and other considerations are discussed below.
Composition of Operating Costs
Labor is often one of the more notable operating costs for manufacturing operations and, as stated, one of the most significant geographically variable costs. While the contribution to the total cost of operations varies by industry and type of manufacturing operation (i.e., capital/process-intensive versus labor-intensive), labor often represents the second-largest geographically variable cost. The variable nature of labor costs makes it a key consideration when determining where to locate facilities.
As a general rule, the financial dimension of location optimization can commonly be reduced to a trade-off between labor and supply-chain costs, where a company often seeks to achieve significantly reduced labor costs for nominally incremental supply-chain costs. This paradigm can be seen in North America, where companies install operations in Mexico to serve the U.S. market, and in Europe, where the candidacy of Eastern European countries for direct investment is tied to the tolerance of the supply chain in supporting the revenue markets in Western Europe.
Figure 1 illustrates the contribution of labor to the before-tax (before "income" tax) operating cost of a manufacturing facility for hypothetical companies in the chemicals and in the medical device industries. (It should be noted that income tax has a notable bearing on the selection of locations in the medical device industry and has a notable impact on the overall cost profile when viewed from an after-tax perspective.) The importance of labor to the ongoing cost of operations is evident in both examples, with labor representing 21 percent of before-tax operating costs for the chemical company and 44 percent for the medical device company.
Labor Cost Differentials
Despite escalations in the cost of labor in some of the world's emerging economies, there remains a notable difference in the cost of labor between the U.S. and emerging economies. At a country level, differentials can be attributed to the level of development and industrialization, labor regulations, and prevailing employee benefits practices. Within a country, the differences are often attributed to city size, composition of the economic base, and prevalence of unions. These factors combine to create a highly variable labor environment across political borders at the country, state/provincial, and municipal levels.
Within the United States, the difference in the cost of labor between high- and low-cost locations can easily range from 10 percent to 25 percent, a figure of relevance to a location decision. Labor differentials, however, are best highlighted when comparing high- and low-cost countries. Figure 2 illustrates the difference in fully loaded labor costs for skilled (two-plus years experience) and unskilled (less than six months experience) labor between the United States and Thailand and China - two of the leading destinations for foreign direct investment in Asia. Such a comparison indicates that costs in the United States are 10 to 15 times higher than in the Asian countries.
The impact of the difference can be seen in the number of companies with products represented by high labor content electing to install manufacturing capacity in such low-cost Asian locations. In an era of significant margin and cost containment pressures, the case for considering locations with low-cost foreign labor is compelling and will likely remain so until fuel costs increase to such a level that the costs of transporting materials and finished product erode the desirability of manufacturing locations that are geographically distant from where sales are generated.
Project Announcements
MR6 Tech Services Plans Huguley, Alabama, Manufacturing Operations
07/29/2025
Adient Plans Normal, Illinois, Production Operations
07/29/2025
UK-Based WB Alloys Plans Danville, Virginia, Manufacturing Operations
07/29/2025
L3Harris Technologies Expands Camden, Arkansas, Production Operations
07/25/2025
Baltimore Fabrication Expands York County, Pennsylvania, Manufacturing Operations
07/25/2025
Mueller Streamline Expands Wynne, Arkansas, Manufacturing Operations
07/25/2025
Most Read
-
20th Annual Area Development Gold and Silver Shovel Awards
Q2 2025
-
In Focus: AI Is Changing Incentives Math
Q2 2025
-
Optimizing Your Rail-Served Transportation Network: Strategy Before Steel
Q2 2025
-
How to Choose the Right Site for Your Factory in 2025’s Volatile Landscape
Q2 2025
-
From Silicon to Server: Mapping the Data Center Supply Chain
Q2 2025
-
Tariffs, Talent, and U.S. Expansion
Q3 2025
-
First Person: David Robey, Co-CEO of QTS Data Centers
Q2 2025