Logistics and Warehousing Adjusts to a Shifting Economy
While the global recession has dampened business for many industries, logistics and warehousing has found growth in adaptation.
Apr/May 10
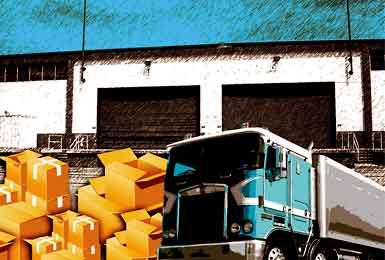
Depending on how sophisticated your logistics processes and strategies are, proximity to the customers or warehouse facilities you must reach every day could limit your site options.
For executives charged with choosing facilities, your options expand if you can figure out how to get more from your logistics functions. The good news is that logistics technology is advancing, and much of the thinking associated with it is progressing just as quickly. Still, decision-makers must ask the right questions, access the right resources, and know how to recognize both.
"One of the things we've realized is that automation - not just in machinery but in systems and supply chains - has reduced the need for inventory, which takes up square footage, by as little as 20 percent and as much as 60 to 70 percent what it used to be," said Jim Ward, CEO of Grand Rapids, Michigan-based Supply Chain Solutions, a third-party logistics provider and supply chain consulting firm.
Plotting a Route
Kuna FoodService, a Dupo, Illinois-based food distribution company, needed to choose a new facility location in 2008, and was interested in property in and around its headquarters near St. Louis. But Kuna officials wanted to look at more than just the cost of the land, according to John Schuler, the company's general manager. They wanted to know how each location would affect distribution costs.
Kuna enlisted Direct Route, a software system developed by Appian Logistics, to solve the problem. Direct Route analyzed several prospective routing scenarios of the company's 22 trucks, which deliver to customers in Illinois and four adjacent states. The site with the best results was in Illinois, just outside St. Louis. By automating routes originating from that site, the company eliminated 15 percent of all routes, and saved $4,000 a month in the process.
The company purchased that site and began operating from its new, 90,000-square-foot facility in July 2008.
"We found out one site might be 20 miles out of the way, but maybe it's got a better path," Schuler said. "We had six sites we looked at to see how we could save costs."
The system even analyzed which routes would make it easier for trucks to use main lanes on interstates, and factored that into the calculated savings.
Considering Flexibility
Need has driven better inventory management - especially given the poor economic climate - resulting in more choices when selecting facility sites, according to Ward at Supply Chain Solutions.
"What we're seeing working with manufacturing companies is that they're holding less inventory for a lot of reasons," Ward said. "They're trying to keep from having so much inventory, carrying costs, product changes - just the infrastructure and the cost around having the inventory sitting somewhere. But also the fact that today we want to buy this and tomorrow we want to buy something else, so you really need to build in the agility."
Companies are showing a preference for just enough on-site space to house their core inventory, Ward said. If a company's business is seasonal, or if inventory tends to fluctuate, companies usually opt for off-site warehousing.
"We've got a client right now that just got a deal with a major retailer, and they've got a one-time new product offering," Ward said. "They're going to have to uptick by five times their normal space."
Supply Chain Solutions is handling the short-term excess inventory at an Ontario, California, facility. When that need has been fulfilled, Ward said, it's likely that another customer will have a similar request.
Recessionary Benefits
Companies also want to make limited-time commitments to their facilities when they can. Interestingly, the faltering economy is working in favor of companies that need more flexibility and lower lease rates from their facilities. Since commercial real estate was overbuilt prior to the 2008 market meltdown, it's a buyer's market, and leasing agents are in no position to demand long-term agreements.
"Right now, strategically, you can get facilities with flex space in a shorter term at great rates," Ward said.
Supply Chain Solutions saw this market need several years ago, and invested in warehouses with multiple resources and services to handle clients' excess inventory in the event of an economic downturn. That business is booming.
Project Announcements
ValorFlex Packaging Plans Bowling Green, Kentucky, Production Operations
06/30/2025
Neuro.io Plans Terrebonne Parish, Louisiana, Operations
06/30/2025
Germany-Based MTU Maintenance Expands Fort Worth, Texas, MRO Operations
06/30/2025
Cascade Die Casting Group Expands High Point, North Carolina, Manufacturing Operations
06/30/2025
BuildOps Plans Raleigh, North Carolina, Operations
06/30/2025
Point Blank Enterprises Plans Wakulla County, Florida, Operations
06/30/2025
Most Read
-
20th Annual Area Development Gold and Silver Shovel Awards
Q2 2025
-
First Person: Joe Capes, CEO, LiquidStack
Q2 2025
-
The Legal Limits of DEI in Incentives Agreements, Hiring, and Contracting
Q2 2025
-
From Silicon to Server: Mapping the Data Center Supply Chain
Q2 2025
-
39th Annual Corporate & 21st Annual Consultants Surveys: What Business Leaders and Consultants Are Saying About Site Selection
Q1 2025
-
Rethinking Life Sciences Site Selection in a Resilient and Dynamic Market
Q2 2025
-
Top States for Doing Business in 2024: A Continued Legacy of Excellence
Q3 2024