Employment in Alabama’s automotive manufacturing sector now approaches 40,000, surging from just a few thousand in the days before Mercedes. Around 27,000 of these jobs are in Alabama’s growing automotive supplier network, which now numbers more than 200 companies. Both employment and production will expand further when the Mazda-Toyota partnership opens a $1.6 billion joint venture assembly plant in Huntsville. Other southern and southwestern states have also attracted foreign automakers and their component suppliers, including Kentucky, Georgia, Tennessee, South Carolina, and Texas.
Cluster Development
Of course, a sizable share of automotive components is made by foreign manufacturers, many of whom have also set up operations in the U.S. To a large degree, foreign auto manufacturers’ move to the U.S. is driven by the need to be close to their customers. Vehicle assembly is largely a regional business because of shipping costs, according to Mark Gottfredson, a partner with the consulting firm Bain & Company and director of Bain’s automotive practice. And the automakers want to source components from suppliers who are in relative proximity, which consequently drives cluster development in areas where foreign automakers have built their assembly plants.
Foreign automakers and suppliers have also been attracted to the U.S. because of the nation’s highly educated workforce and the longstanding “culture of innovation,” Gottfredson says. “Many companies are dissatisfied in their own countries because they don’t have those innovation capabilities,” he notes.
The need for technology expertise is also driving some relocation of suppliers within the U.S., according to Gottfredson. Some foreign auto suppliers that initially opened plants in parts of the U.S. with right-to-work laws and lower labor costs are now having difficulty in finding enough technology-trained workers and are looking to other U.S. locations with better-qualified workforces, Gottfredson says.
California’s Silicon Valley has been called “the new Detroit” because it’s attracting foreign-based companies seeking tech expertise and partnerships. As foreign automotive component-makers continue to locate in the U.S., it’s a good bet that they will gradually reshape the U.S. auto-making cluster map.
Foreign Auto Suppliers Continue to Invest in the U.S.
In order to be near assembly operations and to help further develop vehicle technologies, foreign suppliers to the U.S. auto industry are setting up facilities across the nation.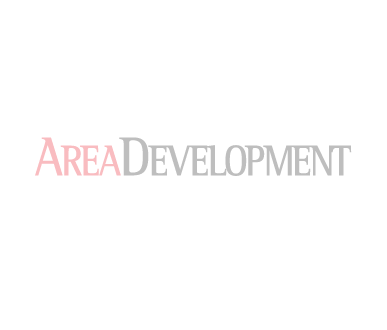
-
Denso
Maryville, TNIn 2017, Japan-based Denso Corp., which develops AI-based vehicle electrification and safety systems, announced it was investing $1 billion and creating 1,000 jobs to expand its 194-acre manufacturing campus in Maryville, Tenn., a suburb of Knoxville.
-
Denso
Southfield, MIDenso has also invested $75.5 million in its Southfield, Michigan, headquarters and $500,000 in its Dublin, Ohio, facilities.
-
Delphi
Pittsburgh, PAIn 2017, Delphi, which has been testing autonomous Audi SUVs in Pittsburgh, announced its partnership with BMW, Intel, and Mobileye to develop autonomous vehicle systems.
-
Aptiv
Boston, MAUK-based Aptiv’s new technology center in Boston’s Seaport district will expand the company’s U.S. engineering footprint and further establish it as a leader in the future of vehicle technology. Aptiv also has technology centers in Pittsburgh, Las Vegas, and Mountain View, Ca., focused on automated mobility-on-demand (AMoD) and data management development.
-
Webasto Roof Systems
Plymouth Township, MIGerman auto supplier Webasto Roof Systems is expanding its operations in Michigan with a new 300,000-square-foot manufacturing facility in Plymouth Township. The company plans to invest nearly $48 million and create 441 new jobs, after winning several contracts from Ford Motor Co. and Fiat Chrysler Automobiles NV.
-
Nokian Tyres
Dayton, TNNext year, Finnish tire manufacturer Nokian Tyres plans to begin production at its first U.S. plant, in Dayton, Tenn. The $360 million facility will produce up to four million tires a year.
-
Triangle Tire
Tarboro, NCChina’s Triangle Tire is investing $580 million in Tarboro, N.C.
-
Sentury Tire
LaGrange, GASentury Tire is investing $530 million in LaGrange, Ga.
-
Hankook Tire
Clarksville, TNSouth Korea’s Hankook Tire is investing $800 million in Clarksville, Tenn.
-
Kumho Tire
Macon, GAKumho Tire is, investing $450 million in Macon, Ga.
-
Giti Tire
in Richburg, SCGiti Tire from Singapore is investing $560 million in Richburg, S.C.
The Trump administration’s tariff policies are also leading some companies to consider reshoring operations to the U.S. from other nations, Gottfredson adds. The new United States-Canada-Mexico agreement, containing some more stringent rules-of origin-requirements, has significantly impacted automotive manufacturers, he points out. The new trade deal requires automakers to build at least 75 percent of a car’s value in North America to remain duty-free within the region, up from the previous 62.5 percent. Car companies also have to ensure 40 to 45 percent of the vehicle is made by workers earning at least $16 an hour, a provision designed to bring more manufacturing to the U.S. The deal also limits annual auto imports from Canada and Mexico at a combined 5.2 million, well above the 4.1 million vehicles that were shipped into the U.S. last year from the two countries. Cars that don’t comply with the new rules will be subject to a 2.5 percent tariff. The deal exempts light trucks such as pickups from the caps.
The Wall Street Journal reported last fall that, soon after the U.S. and Canada announced the new trade deal, executives at several foreign automakers — including German-based multinationals Daimler and BMW — said they were considering revising their supply chains to source more auto parts made in the U.S., Canada, and Mexico.
Meanwhile, President Trump’s policy of negotiating tariffs with individual nations, such as China, has benefited other Southeast Asian countries. An automaker might ask, “Does the supplier have a plant in Vietnam they can move production to?” Gottfredson says. “We can track that U.S. trade with China has been decreasing, due to tariffs, and increasing with Vietnam, Thailand, and Indonesia.”
Automakers want to source components from suppliers who are in proximity, which consequently drives cluster development in areas where foreign automakers have built their assembly plants. Another factor that “tends to create more local suppliers” is exchange rate volatility, according to Gottfredson. “If you’re making parts in another country — like Vietnam, China, Mexico, or Eastern Europe — exchange rates matter a lot.” For example, “If you move to Mexico for a 50 percent wage-rate advantage, and wages make up 30 percent of your product, that gives you a 15 percent cost reduction per part. But if the U.S.-Mexico exchange rate moves negatively — if the peso strengthens against the dollar more than 15 percent — you just lost all of your cost advantage,” Gottfredson explains.
FDI By Automotive Suppliers
Among foreign-based automotive suppliers, one of the biggest investors in U.S. facilities has been Japan-based Denso Corp., which develops artificial intelligence-based vehicle electrification and safety systems. In 2017, Denso announced it was investing $1 billion and creating 1,000 jobs to expand its 194-acre manufacturing campus in Maryville, Tenn., a suburb of Knoxville. The company also invested $75.5 million in its Southfield, Michigan, headquarters and $500,000 in its Dublin, Ohio, facilities that year. And in 2018, Denso invested $10 million in Metawave Corp., a U.S. startup company that develops cutting-edge, millimeter-wave radar-sensing technologies to detect vehicles and pedestrians. Toyota AI Ventures and Hyundai Motor Co. are other strategic investors in the company.
Another high-tech, foreign-based supplier investing heavily in the U.S. is UK-based Delphi. In 2017, Delphi, which has been testing autonomous Audi SUVs in Pittsburgh, announced its partnership with BMW, Intel, and Mobileye to develop autonomous vehicle systems. The partners plan to begin production by 2021. Delphi also has a separate initiative with Mobileye to create a turnkey model for autonomous driving by 2019.
In late 2017, the UK-based Aptiv announced that it had opened a new technology center in Boston’s Seaport district, expanding the company’s U.S. engineering footprint and further establishing itself as a leader in the future of vehicle technology. Aptiv also has technology centers in Pittsburgh, Las Vegas, and Mountain View, Ca., focused on automated mobility-on-demand (AMoD) and data management development.
Foreign automakers and suppliers have also been attracted to the U.S. because of the nation’s highly educated workforce and the longstanding “culture of innovation. Mark Gottfredson, partner, Bain & Company Meanwhile, in the state that has historically led the U.S. automotive industry — Michigan (which still leads the nation in automotive manufacturing employment, with 180,000 jobs based on 2016 data) — the industrial landscape is being reshaped by tech-centric component manufacturers. German auto supplier Webasto Roof Systems is expanding its operations in Michigan with a new 300,000-square-foot manufacturing facility in Plymouth Township. The company plans to invest nearly $48 million and create 441 new jobs, after winning several contracts from Ford Motor Co. and Fiat Chrysler Automobiles NV. The facility will produce automotive roof systems with capacity to expand to other product lines in the future, says Edis Tokovic, Webasto Roofing Systems’ director of Advanced Manufacturing Engineering and Operations Excellence.
Foreign Tire Makers Investing In the U.S.
In recent months, one of the most active supplier sectors has been foreign tire makers opening their first plants in the U.S. Six foreign tire makers have announced projects with a total investment of $3.28 billion in the past three years. Analysts say rising material costs are a factor. By locating in the U.S., manufacturers can greatly reduce transportation costs, to help offset higher material costs. Seeking non-union labor and lower material costs, the tire makers have been drawn to the southern U.S.
For example, next year, Finnish tire manufacturer Nokian Tyres plans to begin production at its first U.S. plant, in Dayton, Tenn. The $360 million facility will produce up to four million tires a year. Other tire makers investing in the U.S. include China’s Triangle Tire, investing $580 million in Tarboro, N.C., and Sentury Tire, investing $530 million in LaGrange, Ga.; South Korea’s Hankook Tire, investing $800 million in Clarksville, Tenn., and Kumho Tire, investing $450 million in Macon, Ga.; and Giti Tire from Singapore, investing $560 million in Richburg, S.C.