Fuel Economy and Greenhouse Gas Regulation
Corporate Average Fuel Economy (CAFE) regulations were first enacted by Congress in 1975 as a policy to increase fuel economy of passenger cars and light-duty trucks. In 2009, new national fuel economy and greenhouse gas (GHG) standards for vehicles were proposed in the U.S. These new regulations harmonize the National Highway Traffic Safety Administration (NHTSA) CAFE standards and the U.S. Environmental Protection Agency (EPA) GHG regulations. NHTSA is tasked with regulating fuel economy and EPA is tasked with regulating GHG emissions — though they are closely related, meeting one regulation does not guarantee meeting the other regulation. With harmonization, automakers will be able to satisfy both sets of regulations.
The first phase of the regulations, which covers vehicle model years 2012 through 2016, will increase the combined required CAFE for light-duty vehicles (trucks and passenger cars) to an estimated 35.5 miles per gallon (mpg) by the end of that period. This level of fuel economy is a substantial increase from the previous mandates, which in 2011 required a combined light-duty vehicle CAFE of 24.1 mpg. Similarly, the second phase, which covers vehicle model years 2017 through 2025, will increase the CAFE requirement for light-duty vehicles to an estimated 54.5 mpg by the end of that period.
The national fuel economy and GHG standards have already had an effect on the design of new vehicles and are poised to have an even greater influence on vehicle innovation in the near future. For the first time, the combined CAFE for passenger cars and light duty-trucks exceeds 30 mpg.
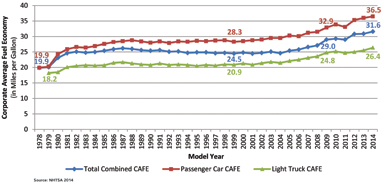
Vehicle weight is a considerable factor in vehicle fuel economy; it is estimated that a 10 percent reduction in vehicle mass can result in a fuel economy improvement of up to 5 to 7 percent. Though achieving greater fuel economy is a main driver for many lightweighting material and process technologies, there are other benefits. Weight reduction is also appealing to automakers because it tends to increase other performance factors valued by consumers: ride and handling, braking, and acceleration. Another key motivation for using new and more highly engineered materials is to improve vehicle safety and crashworthiness.
By switching to lightweighting materials — such as high-strength steel, aluminum, magnesium, and composites — and adopting new forming (e.g., hot stamping and high-integrity casting) and advanced joining (e.g., adhesives, friction stir welding, fasteners, and laser welding) technologies, automakers will be able to significantly reduce the weight of new vehicles. By 2025, automakers are expected to reduce the average vehicle mass by 10 percent or greater versus their 2010 counterparts.
From 1995 to 2010, there were substantial changes in the materials used to create vehicles. During that time period, there was increased use of advanced high-strength steel (AHSS), composites, and aluminum, as well as a decrease in the use of iron castings and regular (mild) steel. As automakers continue to implement lightweighting strategies, these material trends will persist and may even accelerate.
Government and industry are heavily investing to support lightweighting. The states of Michigan and Ohio have leading research efforts in materials lightweighting. The recently announced American Lightweight Materials Manufacturing Innovation Institute (ALMMII), a public-private partnership and a National Network for Manufacturing Innovation (NNMI) institute, will have its main office in Detroit, Michigan, and will conduct significant activities in Columbus, Ohio. The federal government’s $70 million contribution to ALMMII will be matched with at least $78 million in private funds. ALMMII will focus on the use of lightweight metals in transportation applications.
In February 2014, the federal government announced that it would be accepting applications for the creation of another relevant NNMI institute, which would be focused on advanced composites manufacturing (primarily focused on carbon fiber and glass fiber reinforced composites). As with ALMMII, the federal government will support the institute with $70 million to be matched with private funds.
Lightweight materials and new forming and advanced joining technologies will significantly reduce the weight of new vehicles.
Advanced High-Strength Steel (AHSS) - New AHSS implementations are developed every year. By using high-strength steel over mild steel, companies can create thinner components (decreasing vehicle weight) while achieving the same crash performance, although the adoption of high-strength steel poses some challenges to the manufacturing and assembly processes. Third-generation steels are being developed that are ultra-high strength and more formable than other AHSS. Unlike some AHSS materials, third-generation steels do not require a special forming process, such as hot stamping, and are able be cold-formed like mild steel, thus using much of the existing steel-based infrastructure in the industry. Third-generation steels are currently under development, but could be used in vehicles in the near future. These third-generation steels are seen as a threat to other lightweight materials, such as aluminum, due to their potential to provide lightweighting with very little cost penalty.
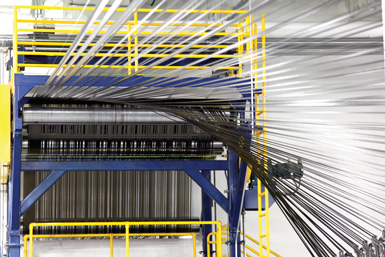
In January 2014, Ford unveiled its 2015 F-150, which is the first high-volume aluminum-bodied vehicle to go into production. The new model is 700 pounds lighter than the outgoing F-150. Ford is investing $359 million to retool the Dearborn Rouge River plant body shop, paint shop, and final assembly to accommodate the change. Following Ford’s lead, other automakers are considering introducing aluminum-bodied vehicles. According to a recent report from Ducker Worldwide, 18 percent of new vehicles will have all aluminum bodies by 2025, up from less than 1 percent of new vehicles today. In the U.S., high-volume pickup trucks are expected to lead this transformation to aluminum. Responding to increased demand for aluminum, suppliers are working to increase capacity. Alcoa, one of the world’s largest producers of aluminum, is investing $300 million to build a new production line in Davenport, Iowa, and $275 million to add more capacity at a plant in Alcoa, Tennessee. Novelis, another producer of rolled aluminum, has invested $120 million to add new capacity at a plant in Oswego, New York. Other companies such as Constellium NV, Aleris Corp., and Wise Metals Group are looking into making U.S. investments.
Composites - Composites also have great potential for a variety of applications, as they can be customized by varying the mix of polymers and reinforcement fibers to meet the specifications of particular components. Advancements in colors, feel (soft skin feel), resistance to ultraviolet rays, and proper management of thermal expansion properties have enabled the use of composites for many components both inside and outside the vehicle (fascias, lids, air foils, knobs, and other components). A significant portion of the interior seating and trim involves plastic, rubber, and composites.
Automakers have examined using composite body panels in their vehicles and, with its excellent strength-to-weight ratio, there has been particular interest in using carbon-fiber–reinforced composites in vehicle bodies. Such materials have already been used in Formula 1 racecars, supercars (e.g., Bugatti Veyron), and airplanes (e.g., Boeing 787). Carbon fiber-reinforced composites are also used in the BMW i3, which was released in November 2013, and in the BMW i8, which was released in June 2014. The raw material is produced in Japan and sent to SGL Automotive Carbon Fibers (a joint venture plant owned by BMW and SGL Group) in Moses Lake, Washington, where it is converted into carbon fiber strands. The carbon fiber strands are sent to Germany, where they are woven and processed into automotive parts before being shipped to the BMW factory in Leipzig for final assembly. In May 2014, SGL Automotive Carbon Fibers announced that, due to the high automotive demand for carbon fiber, the Moses Lake plant would undergo a $200 million expansion, tripling its capacity and making it the largest carbon fiber plant in the world.
Forming, Joining, and Modeling - In addition to the materials themselves, much of the advancement in the automotive materials relates to manufacturing and design methods. Some of the biggest developments in materials technology involve application technologies such as joining (e.g., resistance spot welding, fasteners, adhesives, weld bond adhesive, laser welding) and fabrication (hot forming, thin-wall die casting, composite molds, and aluminum forming) techniques. Material assessment is also important, and computer-aided engineering (CAE) is used to model new materials (e.g., mold flow analysis, formability, and crash simulations).
Economic Development Opportunities
Opportunities to attract investment abound in the current market. To meet fuel economy and GHG emissions regulations, automakers will continue to change the material makeup of their products. The inclusion of these materials in vehicles will require new investments on the assembly line, as automakers retool and recalibrate their facilities to handle new materials. Meanwhile, automotive suppliers, in an attempt to keep up with higher demand from the automakers, will continue to expand their existing plants as well as building entirely new facilities, just as BMW’s demand for carbon fiber and Ford’s demand for aluminum have already led to new investments in U.S. plants supplying those materials.
Though lightweighting is creating some new opportunities in the material supplier space, there are many more opportunities in the overall material supply chain. As materials change, all the parts of the supply chain must also change. For instance, the areas of design engineering, prototype development, tooling, fabrication, and joining will see many opportunities as automakers continue the push for vehicle lightweighting. Economic developers will continue to focus on assisting existing companies that are transitioning to work with new materials that require more complex engineering, enhanced skills, and R&D support.