On the Hunt for a Productive New Biomanufacturing Site?
Real estate and facility strategy can fuel efficiency, scale, and speed to market for your new biomanufacturing operation
Q4 2021
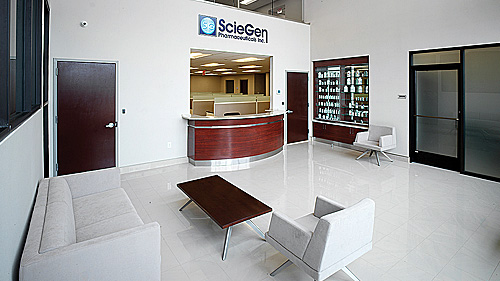
Expansion may well be urgent, considering growing pressure for warp-speed innovation and production. Today’s biologics are supporting a global patient base that’s only going to increase. Thanks to continuing breakthroughs in medicine, more people live longer lives — and seek out more therapies as they age. Meanwhile, millennials are reaching their earning potential, and many prioritize spending on personalized care.
Worldwide pharmaceutical sales are predicted to escalate at a compound annual growth rate (CAGR) of 7.4 percent through 2026, to nearly $1.4 trillion in sales, according to JLL’s 2021 Life Sciences Real Estate Outlook. This represents a major spike in the next six years compared with the previous six, when sales grew at just 2.9 percent. Notably, much of this growth is expected from biotechnology-driven therapeutics sales, which on their own are on pace to grow at a momentous 10.1 percent through 2026.
In addition to meeting rising demand for general biologics therapies, the industry response to COVID-19 will have lasting impact, too. Urgent vaccine production is driving a reinvention of life sciences manufacturing and creating a ripple effect of accelerated production. Since the pandemic began, 600 tests, drugs, and devices were granted emergency-use authorizations, a previously seldom-used regulatory pathway, with many expected to gain Phase II approval over the next three years. Additionally, broad-based support for reshoring of manufacturing will likely increase potential speed to market and profitability into the future.
Critical Key Steps
To keep up with all the momentum, biotech innovators need access to well-located, compliance-forward, talent-friendly manufacturing facilities. Following are three critical key steps to accelerate opening — and position the location for longer-term agility and innovation.
Step 1:
Foster innovation with tech-fueled site selection.
Choosing the right location is critical to efficiency, compliance, and talent considerations alike. You’ll need to weigh a range of competing criteria, including proximity to research and development (R&D) facilities, supply partners, and labor pool.
For example, choosing a Good Manufacturing Practices (GMP) facility near R&D operations can shorten the supply chain and allow for collaboration between researchers and manufacturing staff that will develop and refine processes, particularly for small-batch, clinical trial manufacturing. Generally, it’s also important to look for facilities with generous, clear heights; ample utilities; and backup power; as well as easy access to major transportation infrastructure.
Today’s biologics are supporting a global patient base that’s only going to increase. Yet, it’s challenging to find ready-to-use biopharmaceutical production space in the U.S. — especially near the most advanced clusters in Boston and San Francisco. According to JLL research, long-term employment increases, industry and demographic shifts, record funding, tight vacancies, and rising rents are all signs of space limitations in the life sciences real estate market.
Fortunately, advanced data and analytics tools can bring accuracy and speed to your search, helping you elevate worthy location options and avoid costly missteps. By visualizing multiple sites against your criteria, you can assess the pros and cons of any location, from macroeconomic data and tax incentives, to prospective path, to ownership and flexibility.
If your initial searches aren’t promising, it may be worthwhile to consider adaptive reuse. Building a new facility in the right location is complex and time-consuming — a mismatch for fostering innovation. Leasing and adapting an existing GMP space can help your organization expand production faster, leaving more resources for R&D.
Consider, for inspiration, the Seattle developers who are converting a former T-Mobile data center space in the crowded Bothell submarket. Other creative adaptive re-use stories include repurposing a former ice-skating rink, a printing press facility, vacant malls, and big-box stores.
Once you’ve narrowed down the right location, turn to a project management team to help accelerate facility buildout from design and site plan review through implementation. An experienced project manager can help navigate the entire process, from facility system decisions like electricals and HEPA filtration, to procurement and contracts, to commissioning and validating production processes.
Step 2:
Design flexible space for the people who will use it.
Biomanufacturing facilities are first and foremost a workplace. The people who work there day in and day out will perform better if they are supported by the space to do their best work.
Integrate human experience into design strategy from the outset. You might begin by providing space for employee well-being features, such as natural light, outdoor views, plants, and high-quality indoor air. Most leading life sciences organizations have already recognized these advantages in other facilities, but today’s in-demand biomanufacturing specialists are also uninspired by the windowless and cramped settings of traditional manufacturing facilities.
Create flexibility in your buildout throughout, to support a quality work environment while also strengthening organizational agility. After all, research priorities can change rapidly, as can manufacturing technologies.
Choosing the right location is critical to efficiency, compliance, and talent considerations alike. To avert functional obsolescence, incorporate flexible design principles that allow for new configurations and foster more agile operations, like “plug-and-play” equipment, moveable workbenches, and retractable electrical coils. Other strategies include adding thick floor slabs in corridors to support movement of heavy equipment in and out without damaging the floor.
Space configuration can also play a role in improving the human experience at work. As biomanufacturing becomes more collaborative, laboratory researchers, engineers, and data scientists alike will increasingly work alongside each other at intervals through the pre-clinical manufacturing process. Often this cross-section of colleagues requires a mix of collaboration-oriented workspaces that they can claim as needed. Positioned in lower floors near entrances and exits, these collaborative areas can also help facilitate flexible working patterns while showcasing a culture of collaboration. By offering inviting, well-lit spaces with video-conferencing capabilities, whiteboards, and open seating, your organization can show it values idea exchange and multidisciplinary innovation.
Other ways to leverage workplace design to support recruitment and retention include on-site cafeterias, huddle booths, informal lounges, and other casual socialization areas — balanced by their opposites: quiet rooms and/or a library for heads-down work.
Step 3:
Boost productivity with leading facilities management.
Biopharmaceutical manufacturing has traditionally been resource- and cost-intensive, in part due to its low yields and relatively high level of waste. With facility management (FM) best practices, however, organizations can make significant gains in efficiency.
Effective FM teams can start with the basics, solving facilities distractions and making repairs as they come up to create a reliable environment that supports core employee productivity. They can also perform mundane, yet critical, operational tasks such as providing a steady supply of clean glassware and research or testing inventory so that their teams don’t have to. But they can go further, too. With preventative maintenance practices, FM experts can avert costly replacements, extending equipment life — and long-term value.
Importantly, experienced life sciences facility managers know that manufacturing facilities for breakthrough therapies need more specialized knowledge than is needed for facilities in other manufacturing sectors. In fact, for biologics, cell and gene therapy, and other emerging biotechnology modalities, manufacturing facilities demand the same kinds of compliance, quality control, and maintenance strategies as are required in R&D environments.
To avert functional obsolescence, incorporate flexible design principles that allow for new configurations and foster more agile operations. To produce, test, and improve development of today’s increasingly sophisticated class of drugs, companies need access to compliant, GMP facilities. They need to know their facilities are in continual compliance with FDA regulations governing safety, sanitation, and quality-control procedures from production and processing through packaging. By partnering with a trusted facilities management provider, biomanufacturing leaders can stay laser-focused on their core work, entrusting their partner with the critical matter of compliance.
Worthy FM service providers can add further value by contributing a deep bench of skilled workforce. Leading providers will have invested in talent, technologies, and best practices to manage the most challenging, highly specialized lab and manufacturing environments across the life sciences industry. They may also be able to offer substantial pricing discounts on supplies and services through their own vetted supplier networks. If you’re considering enlisting a third-party facility management company, look for parties with a deep track record in facilitating regulatory compliance, operational consistency, and quality assurance in diverse, sophisticated facilities.
To support quality and optimize uptime, enlist select FM leaders early in the process to create standard operating procedures for safety, calibration, quality assurance, and other critical areas well before production begins — and to maintain 99 percent uptime and rigorous regulatory compliance from thereon out.
An accelerated site launch is only the beginning.
In the coming months and years, biotechnology companies can expect to see more demand for their products — if they step up to the opportunity now. Breakthrough treatments will always be needed, and a growing global population guarantees demand will only continue to increase.
Whether you’re preparing to launch a site to support clinical trials, or for full-scale to-market production, providing the right facility — in the right location and with the right strategy — will help advance the global effort to improve quality of life for people around the world.
Project Announcements
Swiss-Based Galderma Plans Miami, Florida, Headquarters Operations
06/19/2025
Sentio BioSciences Expands Maryland Heights, Missouri, Production Operations
06/14/2025
IONETIX Corporation Expands Lansing, Michigan, Operations
06/05/2025
Zoetis Establishes Louisville, Kentucky, Diagnostics Reference Operations
06/05/2025
SJ Incorporation Plans Cascade, Maryland, Production Operations
05/27/2025
Merck Plans Wilmington, Delaware, Biologics Operations
05/23/2025
Most Read
-
20th Annual Area Development Gold and Silver Shovel Awards
Q2 2025
-
First Person: Joe Capes, CEO, LiquidStack
Q2 2025
-
The Legal Limits of DEI in Incentives Agreements, Hiring, and Contracting
Q2 2025
-
From Silicon to Server: Mapping the Data Center Supply Chain
Q2 2025
-
39th Annual Corporate & 21st Annual Consultants Surveys: What Business Leaders and Consultants Are Saying About Site Selection
Q1 2025
-
Rethinking Life Sciences Site Selection in a Resilient and Dynamic Market
Q2 2025
-
Top States for Doing Business in 2024: A Continued Legacy of Excellence
Q3 2024