A “Nicer” Work Environment
Manufacturing talent today is becoming as demanding of their workplace as they are of their compensation.
- 21 percent of employees would take a 10 percent pay cut to work in a nicer environment (Staples Annual Workplace Survey).
- 69 percent of employees would be willing to give up other benefits to work in a well-designed space (CBRE study).
- 54 percent of employees agree that when it comes to considering a new job, office design is equally or more important than office location. That number increases to 64 percent among mid-level employees (Capital One study).
For example, when creating the master plan for AeroHub, an advanced manufacturing innovation district in Cincinnati, Ohio, use and activation of the campus was identified as a critical planning principle. Providing a denser physical setting for productive, informal and social relationships that foster ideas and problem-solving is key to success. Exceptional shared places can foster identity and provide the kind of dynamic environment necessary to attract the most critical component of innovation — talent.
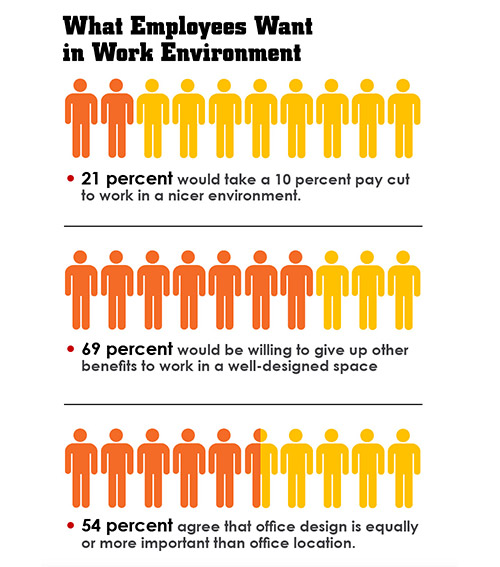
This newer generation of workers also wants to align with companies that share their values. According to a recent Glassdoor study, alignment with culture and values is the #1 factor for employee satisfaction.
Fostering innovation, wellness, and sustainability are often cited as key company values to which the new generation of workers connects. The representation of — or lack of — these values is often interpreted through the workplace design. A well-lit interior with both collaborative and private spaces along with exterior amenities — such as greenways, walking trails, and water features — offers benefits to the employees as well as improved aesthetics for neighboring properties. Architects can also introduce WELL building standards for improving health and human experience. LEED®, a building rating system from the U.S. Green Building Council, provides guidance for sustainable buildings.
As an example, emersion Design’s $23 million brownfield rehabilitation of a 1930’s aircraft hangar into a state-of-the-art advanced power and thermal laboratory and test facility was completed with a primary emphasis on sustainability and energy conservation. The project preserved an important historical structure with a conversion that accomplished LEED Gold certification and was the recipient of a Federal Energy & Water Management Award. The success of this project demonstrates that renovation and new construction offer opportunities to design and construct facilities that meet programmatic needs while creating an environment suited to attract the best talent.
Operational Efficiency, Flexibility
While manufacturing leaders want to incorporate innovative facility design to attract and retain young, technical talent, they also need to build a template for their operations and facilities that delivers operational efficiency and can adapt to ongoing change. Flexibility of the facility is imperative in a rapidly advancing manufacturing world.
Facilities should be designed so that they can be easily expanded or adjusted to meet changing production needs. Flexible manufacturing systems most often are highly automated facilities so accommodation of current and future technology support should be considered. The facility should also be designed to accommodate smooth process flow. This doesn’t necessarily have to consist of straight rows in a rectangular shaped building. An architect working with the manufacturing team can provide potential design options to support different process flows, materials storage and handling, product output and worker safety. The facility should be designed to minimize materials handling, avoid bottlenecks, minimize machine interference, ensure high employee morale and safety, and ensure flexibility, among other goals. Facility design must be considered very carefully to avoid redesign and renovations.
Critical items to consider when designing to achieve the above goals include:
- Space utilization: Width of traffic lanes and vertical space for storage are core considerations.
- Shipping and receiving: There always seems to be a shortage in this area so allow ample room.
- Ease of communication and support: Facilities should be laid out so that internal communication and interactions with vendors and customers can be easily done either in designated floor areas or easily accessible conversation rooms.
- Safety: The facility layout should support Occupational Safety and Health Administration (OSHA) guidelines.
Improved Loyalty, Productivity
By combining design aesthetics to attract talent with functionality for operational effectiveness, manufacturers can expect a notable impact. Countless studies have indicated that employee wellness impacted by workplace design has a major impact on loyalty and productivity.
For example, a study by the World Green Building Council recorded an 11 percent increase in productivity as a result of increased fresh air to the workstation and a reduction in pollutants. While another study by CABE/British Council for Offices showed even greater improvements. A well-lit and well-ventilated work space was found to decrease the number of absences and increase satisfaction by 24 percent. In turn, productivity went up by 16 percent. Truly, being comfortable while working decreases absences and boosts satisfaction, which, in turn, increases productivity.
This approach to more comprehensive design thinking can also support and reinforce the company brand. If the facility is aesthetically pleasing, it can reinforce the brand reputation as well as the inclination to protect it by maintaining a clean and attractive workplace.
Campus-like environments, distinctive architectural elements, and collaborative workplaces ultimately distinguish new and renovated facilities that attract top talent, improve job satisfaction, and deliver optimum productivity. Manufacturers who understand this evolution in facility design will enjoy a rapid return on their investment and distinguish themselves from trailing competitors who are slow to embrace this concept.