A Disciplined Road Map for Industrial Site Selection
By gaining real data in the pre-capital planning stage, a business can achieve a solid basis for making critical operational and locational decisions.
Q2 2020
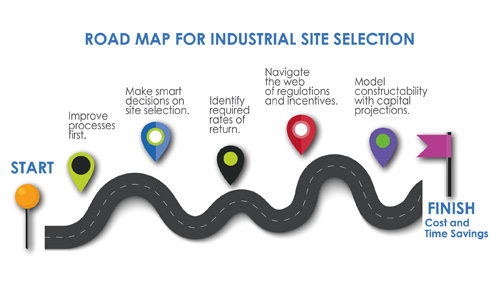
Plant owners and managers may agree on the need for new production lines, more distribution capacity, new automation processes, and more staff. But this is also when additional rigor is most urgently needed to analyze the best-case business scenarios for that next step. It’s when a pre-capital plan with disciplined site selection criteria is most needed.
All this delivers cost and time savings.
It takes time and effort to begin drilling into the details of industrial or manufacturing operations and even material-handling and supply-chain processes. It becomes quickly apparent that a whole network of processes must be reviewed. Marshaling the resources needed to help a manufacturer identify and analyze the full scope of potential process efficiencies can involve a number of disciplines, ranging from engineering and technology specialists to finance, legal, environmental, and government relations.
These initial steps of pre-capital planning aim to assess a business’ objectives and existing capabilities mapped against broader macro trends within a given industry and the economy. The focus is on gaining real data that can provide a solid basis for critical decisions on the best course forward.
Time is of the essence. Industries like food and consumer products, among many others, are driven by rapid changes in consumer tastes and expectations, not to mention interruptions to supply chains brought on by unexpected events such as the recent coronavirus pandemic. That means pre-capital planning needs to occur on a very accelerated cycle, which presents another strong argument for engaging an outside team of experts with the resources and base of knowledge who can quickly gather relevant data and present options within a matter of weeks.
Improve processes first.
Before any business makes a seven- or eight-figure capital investment, it is simply prudent to first look at the full range of potential process improvements that may be made, either at an existing facility or new facility. If some of the manufacturer’s goals can be met via simpler and less costly process improvements, the pre-capital exercise is often the right time to identify them. Perhaps reductions in “minor stops” and “breakdowns” on production lines can be achieved with better maintenance and focused improvement events.
It is simply prudent to first look at the full range of potential process improvements that may be made, either at an existing facility or new facility. Nearly every manufacturing or industrial facility has mountains of data. However, managers often have neither the time nor resources necessary to analyze it to reveal sources of problems and opportunities for improvement. The focused efforts of an outside multi-discipline team can identify the reasons processes are being interrupted and recommend solutions ranging from new technology, automation, robotics or simply improved maintenance and processes among front-line production personnel. Processes optimized at existing facilities can easily be captured and transferred to new facilities.
Make smart decisions on site selection.
Pre-capital planning is an essential discipline that dovetails with site selection. It is imperative that the critical step of investing in a new facility be guided by facts and data and not be just a guess. In starting the site evaluation process, the first question always should be: “What are the infrastructure needs?” Next question: “What are the business drivers?” And, the following questions: “Does the new facility need to be close to existing or new markets, or will it gain cost advantages by moving closer to supply sources? Will more immediate access to certain labor pools create additional advantages?”
Plant owners and operators who try and tackle these questions independently without access to all available data and expertise of a range of experts face a heightened risk of making crucial mistakes. Proper due diligence requires rigorous analysis and short-cutting this step can result in erroneous conclusions and costly mistakes that may only show up much later in the business cycle.
Identify required rates of return.
Though site selection can be complex, it becomes a more straightforward process if it is preceded by pre-capital planning that establishes a list of factors that can be evaluated on both a quantitative basis and a qualitative basis.
Pre-capital planning is an essential discipline that dovetails with site selection. Though each owner/operator will have their own proprietary criteria for site selection, based on business needs and objectives, cost is almost always near the top of the list. Industries such as food processing, for example, have high financial hurdles for any capital investment, usually in the neighborhood of a 20 percent internal rate of return (IRR) on a payback timeline that can be as short as three years or even sooner.
Location and proximity to markets and supply chains can directly impact IRR. Energy costs can also be important in certain regions as well as power interconnections. Condition of roads, sewers, and high-quality water supplies also must be assessed, along with available pools of skilled labor. Projected taxes and availability of tax incentives also must be considered.
Despite these factors, it is still strongly recommended that owners and developers consider total lifecycle costs in evaluating potential plant sites. Low upfront development costs often are offset by high long-term expenses. For example, water quality will be a major consideration for many process manufacturing facilities. Selecting a site with marginal water quality simply because it is low-cost may require construction of advanced water treatment facilities that offset any upfront cost savings. Similarly, locations with low utility rates may also present issues with power quality and reliability, resulting in the need to construct backup generation on site.
Projecting operations and maintenance expenses, long-term depreciation rates, and expected energy cost fluctuations can be helpful exercises because they force a longer-term view. The amount of detail provided in the site assessment is a marker for how successful a cost-savings assessment will be.
High financial hurdle rates are the best argument possible to engage a broad team with expertise in disciplines ranging from master planning; environmental assessments; permitting; and land acquisition to civil, structural, electrical, and mechanical engineering; architecture; and construction.
Navigate the web of regulations and incentives.
Tax incentives or other inducements such as promised infrastructure improvements can come into play in many site selection exercises. These can be important, but owners and developers must not be enticed into weighting them more highly than they should be. Regulatory and permitting requirements should also be weighed in the balance before determining if incentives are enough to offset any of these potential hurdles.
It is strongly recommended that owners and developers consider total lifecycle costs in evaluating potential plant sites. Major constraints are always a first consideration for any given site. For example, are there wetlands and mitigation requirements that might come into play? If the site is in a floodplain, are there constructability issues or adequate protection from levees and other nearby infrastructure? Are there constraints on zoning, land use, stormwater management, building heights, setbacks, and parking? Will the business encounter environmental concerns such as endangered species, historic or cultural preservation, air quality or noise constraints? And, through it all, working to alleviate any concerns of local, state, and federal government agencies, as well as concerned public stakeholder groups, is a necessary step. The list can be immense before a project is ready to be “greenlighted.”
Model constructability with capital projections.
It’s no secret that selecting the right site for your manufacturing or distribution facility is part of a broader puzzle. Understanding how all the pieces fit together will help you efficiently maximize production resources, labor resources, and land requirements.
By making a careful analysis of internal and external factors through a deliberate capital planning process, you can often identify meaningful process improvements that will save money over the long term. Then, utilizing this framework in a disciplined site selection process, while also utilizing a team with broad-based expertise, can give you peace of mind that you have made a wise investment of hard-earned capital.
Project Announcements
Busch Vacuum Solutions Plans Tempe, Arizona, Operations
08/18/2025
Made Scientific Establishes Princeton, New Jersey, Manufacturing-Headquarters Operations
08/18/2025
Comcast Establishes West Palm Beach, Florida, Operations
08/17/2025
Buttonwood Farm Expands Fortuna, Missouri, Egg Production Operations
08/15/2025
MerryGoRound Plans Pittsylvania County, Virginia, Fulfillment Operations
08/14/2025
Hartman Cabinetry Plans Jonesburg, Missouri, Operations
08/14/2025
Most Read
-
What We’re Getting Wrong About Gen Z’s Future in the Skilled Trades
Q3 2025
-
A New Course for U.S. Shipbuilding
Q3 2025
-
Optimizing Your Rail-Served Transportation Network: Strategy Before Steel
Q2 2025
-
In Focus: AI Is Changing Incentives Math
Q2 2025
-
How to Choose the Right Site for Your Factory in 2025’s Volatile Landscape
Q2 2025
-
Reshoring Reality Check from Construction
Q3 2025
-
The New Math Behind Mexico and U.S. Manufacturing Decisions
Q2 2025