Radical Transformation in the Food & Beverage Industry
Food processing, packaging, and delivery are all being disrupted by changes in technology, consumer preferences, and government regulations.
Q4 2019
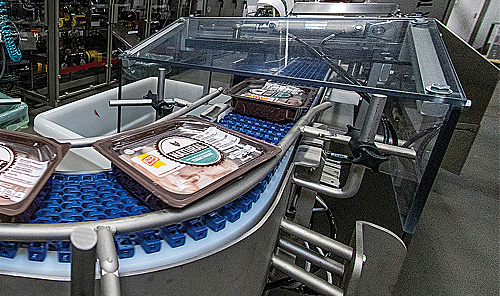
This is just one of the many factors facing the food and beverage industry today. The sector is always changing, but it is experiencing a true evolution with food production, packaging, and delivery all undergoing rapid changes. Food processors are learning to adapt and keep up with consumer trends, millennial demands, and regulation shifts while also taking necessary steps to prepare for the next round of changes. Though change often corresponds with challenges, this industry revolution ultimately coincides with growth in the sector.
Defining Modern Food Processing
The food industry is at a very pivotal time. It’s technical, advanced, and fast. Still, the modern food landscape requires more. Modern food processing is being built around three simple concepts — speed, efficiency, and customization.
“Consumer tastes are evolving faster than ever before, and we can see with the spread of social media and other technologies that companies can measure the relative success or demand for a new product at an increasingly fast pace,” says Walker Mattox, president of GraySolutions, a Gray company. “As a result, manufacturers must have the necessary processing and manufacturing capabilities to respond.”
What Do Consumers Want?
In this age of information in which we live, awareness is everywhere, including the food supply. Consumers have more insight into the food they eat than ever before, and therefore expect more from food processors, suppliers, and farmers. And, like it or not, these expectations are a direct reflection of how consumers shop and make purchases.
Consumer trends are putting increased pressure on the entire industry. As processors respond to current demands and prepare to be proactive for the future, they must think about specialized processing, packaging, and equipment. Some are looking to new facilities, and others are looking to expand current operations.
Consumer demand for varied product selections means that production and packaging lines need to be designed for maximum flexibility. Consumer demand for varied product selections means that production and packaging lines need to be designed for maximum flexibility. When this flexibility is designed into a facility, all adjacent spaces need to be thoroughly evaluated to understand the ripple effect. Line changeover operations or multiple packaging lines for various products greatly affect people flow, maintenance needs, egress requirements, and equipment accessibility — translating to comprehensive plant design studies.
Similarly, a ready-to-eat (RTE) facility needs a comprehensive assessment to ensure that all cross-contamination risks are studied relating to the flow of people, product, air, and waste stream. Gray recently designed and built a new 382,000-square-foot ready-to-eat (RTE) meat processing and packaging facility for Kraft Heinz. Instead of segregating raw and RTE employees within a central administrative office complex for this project, we worked with the customer to implement a total separation strategy that resulted in two separate offices for raw and RTE on opposite ends of the facility.
Another form of flexibility consumers are demanding concerns food packaging. The single-serve packaging category continues to grow due to increased business and the need for more convenient food offerings. However, consumers don’t want to sacrifice taste, meaning the quality cannot be compromised.
As part of the growing awareness for how foods and beverages are processed, consumers are also demanding operational changes pertaining to efficiencies and increased uptimes. For processors, this means specialized, often custom, equipment that escalates profitability and minimizes energy usage and the overall footprint. Ultimately, manufacturers need fully integrated solutions to meet current and future demands.
Why Food Safety Is Always Paramount
While efficiency, flexibility, and automation are all key catalysts for modern food processing, food safety remains at the core and is the driving force behind many major investments in the food space. The romaine lettuce recall provided even further validation of the importance of food safety, and it’s clear the marketplace is very punitive to companies and brands having product recalls.
While efficiency, flexibility, and automation are all key catalysts for modern food processing, food safety remains at the core and is the driving force behind many major investments in the food space. Driven largely by the implementation of the Food Safety Modernization Act (FSMA) and consumer demands, modern food safety is all about verification and information. As a result, automation integration is bringing about increased improvements in food safety.
With the advancement of the Industrial Internet of Things (IIoT), companies can collect and store data on their cleaning processes, Hazard Analysis and Critical Control Point (HACCP) programs, and a myriad of other safety and quality programs. This helps to better manage operational schedules, resources, labor, maintenance, and, of course, food safety.
“Manufacturers want their food processes protected from foreign materials in the plant environment and within the actual process equipment through sanitary design and proven sanitation procedures,” points out Gregg Coleman, president of InLine Engineers, a Gray company. “Processors drive quality in their process through documented and verified procedures at all operational units and critical control points.”
Traceability has become progressively important to ensure the safety of the food supply, especially in recall scenarios. Advancements in traceability allow food processors to have visibility into the source of their food from farm to table. Manufacturers are also adding sensor data into traceability data, not just to track critical control points, but also to confirm temperatures for product storage, specifically in cold storage facilities. The verification of these temperatures can lead to better quality and improved customer satisfaction, not to mention overall food safety.
In today’s landscape, companies are moving beyond exploring what new technology can do and are instead determining how they can integrate it. If not, they will fall behind others in the space that are making the technology investment toward stronger food safety measures.
Challenges Ahead
There’s no way around it — food and beverage companies face growing uncertainty ahead. From a global perspective, trade tensions are expected to continue for the foreseeable future impacting both supply and demand. The labor market, both with rising wages and tight availability of workers, is also cause for manufacturers to look toward innovative solutions to stay relative and compete in the global marketplace.
Still, keeping up with food safety and consumer demand is arguably the greatest challenge for food and beverage processors. Many of the changes in regulation and food safety are driven heavily by consumers.
Tackling big data and understanding how to adopt blockchain and IIoT also weigh heavy on all companies, but food processors must embrace the challenge. Traditionally, food processors have adopted technologies behind their counterparts in other industries. Food processors that decide to invest now will see a greater pay off from these technologies as they permeate the marketplace.
Other areas hitting the industry are distribution (logistics) and supply chain infrastructure. While all of these challenges have the potential to make or break some operations, they also present numerous opportunities for companies to consider strategic investments in their future.
Looking Into the Future
Future food processing will continually hold food safety in the highest regard, always looking to improve sanitary procedures and conditions in operations to reduce any potential risks. While the actual production processes may not change significantly, Coleman believes there will be a greater awareness of energy consumption and waste reduction.
According to Brian Bernard of Spec Engineering, a Gray company, there will be two distinct areas of focus in the near future. For starters, there will continually be a rise of more locally sourced products to consumers, with a focus on wholesome and natural ingredients. Secondly, large-scale processors of protein (e.g., plant-based) and sustainable ingredients derived from agriculture and processing will increasingly work together.
“Automation and digital technology adoption will be the largest shifts in food processing from its current state,” says Mattox. “Similar to other sectors, the food industry is dealing with labor shortages across the world. Some processors are looking at automation to alleviate their labor concerns in order to expand capacity. Processors will continue to invest in automation in order to meet evolving consumer tastes.”
He continues: “Processors will also begin investing in two very specific processing models — one for mass production and another platform to deliver highly customized products. Companies that are strategic in this investment model will have the upper hand as the market evolves.”
Even with all the automated elements, processors must remember that food is very personal to consumers. From the research and shopping to the actual cooking and consumption of food, consumers truly make an experience out of food. The processing challenge lies in balancing customization, technology, safety, and quality to ensure personalization expectations are met.
Additionally, smaller companies can penetrate broad markets easier today than ever before, and smaller producers are now faced with the challenges of their larger, older competitors. Despite changes, the future of the food and beverage industry holds promise and opportunity for every facet — lab-grown plant and animal proteins, ready-to-prepare meals on your doorstep, healthy-eating trends that change with the seasons, and a transparent and traceable food supply. The food and beverage industry has never been more exciting — or more challenging. The next few years are sure to bring radical transformation.
About Gray
Gray is a fully integrated service provider deeply rooted in engineering, architecture and construction services. As a family-owned company, Gray focuses on the food and beverage, manufacturing, automotive, distribution, and commercial markets for domestic and international customers. In recent years, Gray has made a strong claim in the food and beverage market with the addition of InLine Engineers for trusted engineering expertise in complete end-to-end process and packaging line functionality, Spec Engineering for prefabrication of various process equipment assemblies and enhanced process equipment component engineering, and also formed Gray Solutions for complete digital solutions.
Project Announcements
Buttonwood Farm Expands Fortuna, Missouri, Egg Production Operations
08/15/2025
Pilgrim’s Plans LaFayette, Georgia, Operations
08/12/2025
Canada-Based Vibrant Health Products Plans Rossville, Tennessee, Manufacturing Operations
08/01/2025
Turkish-Based Kervan USA Expands Lehigh Valley, Pennsylvania, Operations
07/24/2025
Lactalis USA Upgrades Walton-Buffalo, New York, Production Operations
07/18/2025
Fine Organic Industries Limited Plans Jonesville, South Carolina, Operations
07/14/2025
Most Read
-
Tariffs, Talent, and U.S. Expansion
Q3 2025
-
What We’re Getting Wrong About Gen Z’s Future in the Skilled Trades
Q3 2025
-
Data Center Demand Stabilizes Amid Changing Market Forces
Q3 2025
-
A New Course for U.S. Shipbuilding
Q3 2025
-
Optimizing Your Rail-Served Transportation Network: Strategy Before Steel
Q2 2025
-
In Focus: AI Is Changing Incentives Math
Q2 2025
-
Rewriting the Rules of Warehouse ROI
Q3 2025