Front Line: Vocational Training Alliances in Tough Times
Companies and communities must continue to invest in and destigmatize vocational training in order to bridge the manufacturing skills gap.
Q4 2020
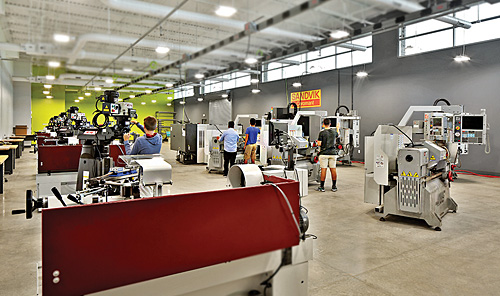
A 2018 report by Deloitte and the Manufacturing Instituteestimated the manufacturing industry would have as many as 2.4 million jobs to fill by 2028. Last year, the National Association of Manufacturers (NAM) reported in 3rd Quarter 2019 that the top concern among manufacturers was the inability to attract and retain a quality workforce.
Stephen Gold, president/CEO of the Manufacturers Alliance for Productivity and Innovation (MAPI), recently wrote in IndustryWeek that the skills gap today isn’t so much about a lack of STEM majors, but companies foregoing investment in training and four decades of stigmatizing vocational education. Yet, some communities and corporations are trying to address this problem by working together to create vocational training programs to attract more students to advanced manufacturing.
One example is Tri-County Technical College in Pendleton, S.C. Grayson Kelly, vice president of Institutional Advancement and Business Relations at the college, says its program is unique as it co-locates business and industry with K-12 education through the Hamilton Career and Technology Center in Westminster, S.C., and postsecondary education through Tri-County Technical College.
“High school students have the opportunity to get a head start on college by taking courses for dual-credit,” he explains. “By the time they graduate from high school, they will have earned a certificate from Tri-County and be well on their way to earning their associate degree.”
These same students also can participate in work-based learning at neighboring businesses, which can lead to meaningful careers that pay family-sustaining wages. “For businesses, this is an opportunity to create a crucial recruitment pipeline, decrease turnover and help influence, mold, and shape potential future employees,” Kelly adds.
Vocational training is becoming more important than ever to deliver an agile, skilled talent pipeline that makes it possible for companies to attract and retain a workforce that meets their unique requirements. Elli Bowen, vice president of Business Development, KC SmartPort Kansas City has also implemented efforts to address growing worker needs in tech and logistics positions.
“Vocational training is becoming more important than ever to deliver an agile, skilled talent pipeline that makes it possible for companies to attract and retain a workforce that meets their unique requirements,” states Elli Bowen, vice president of Business Development at KC SmartPort.
Examples include KC Tech Academy, an industry-led, two-year competency-based training program currently offered to high school juniors and seniors in select school districts in the Kansas City region, and Skilled KC Technical Institute, which focuses on careers in high demand but in short supply in the Kansas City region. Skilled KC’s first three programs (advanced manufacturing, software development, and biotechnology lab technician) were launched on Sept. 8, 2020.
Columbus, Ohio, offers yet another example of a robust program. Jeff Spain, director of the Manufacturing Extension Partnership (MEP), Columbus State Community College (CSCC), explains that CSCC “ties existing curriculum to corporate workforce needs and tries to generate a talent pool that can address the innovative changes we see develop within manufacturing each year.”
One program that has thrived during COVID is CSCC’s Modern Manufacturing Work Study (MMWS.) Spain describes it as an “earn and learn” program that combines classroom and lab-learning with the opportunity for a paid work-study position at a local industry partner. CSCC has awarded more than 50,000 degrees and has a near $1 billion dollar annual impact on the local economy.
Project Announcements
MR6 Tech Services Plans Huguley, Alabama, Manufacturing Operations
07/29/2025
Adient Plans Normal, Illinois, Production Operations
07/29/2025
UK-Based WB Alloys Plans Danville, Virginia, Manufacturing Operations
07/29/2025
L3Harris Technologies Expands Camden, Arkansas, Production Operations
07/25/2025
Baltimore Fabrication Expands York County, Pennsylvania, Manufacturing Operations
07/25/2025
Mueller Streamline Expands Wynne, Arkansas, Manufacturing Operations
07/25/2025
Most Read
-
20th Annual Area Development Gold and Silver Shovel Awards
Q2 2025
-
In Focus: AI Is Changing Incentives Math
Q2 2025
-
Optimizing Your Rail-Served Transportation Network: Strategy Before Steel
Q2 2025
-
How to Choose the Right Site for Your Factory in 2025’s Volatile Landscape
Q2 2025
-
From Silicon to Server: Mapping the Data Center Supply Chain
Q2 2025
-
Tariffs, Talent, and U.S. Expansion
Q3 2025
-
First Person: David Robey, Co-CEO of QTS Data Centers
Q2 2025