Managing Supply Chain Disruptions From the Baltimore Bridge Collapse
Supply chain disruptions from the Baltimore bridge collapse prompt innovative solutions and renewed focus on resilience, as companies leverage lessons from the pandemic to navigate the crisis and ensure continuity in one of the busiest ports in the U.S.
Q2 2024
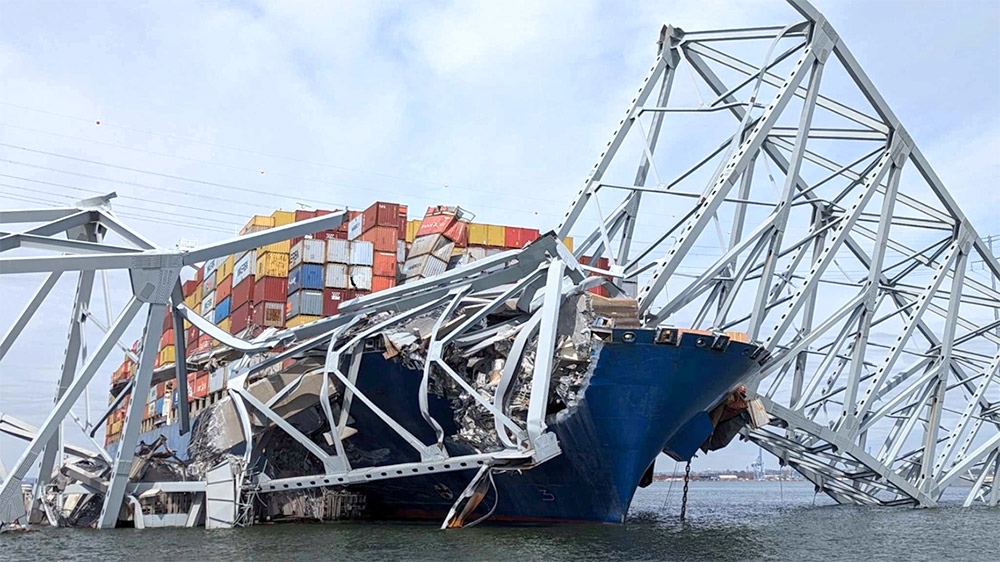
As a key port of call for bulk commodities, automobiles, construction and agricultural equipment, ripple effects were to be felt by a multitude of companies that depend on the Port of Baltimore for meeting customer demands and maintaining their operations. Supply chain managers and shippers were once again sent into crisis management mode to find solutions.
In 2021, contingency planning gained unprecedented significance when supply chain managers and executives faced the supply chain issues of the pandemic and the obstruction of the Suez Canal by a cargo ship. These pivotal events necessitated the development of comprehensive preparation and mitigation plans for future interruptions.
Brewster Smith, head of supply chain solutions with Colliers says, "firms should draft and annually review a 'Disaster Recovery and Business Continuity Plan,' which provides the tactical and logistical instructions for all employees to follow in the context of natural disasters, terrorism, infrastructure disablement and any other asymmetric disruptions." Within the plan, a 'Risk Assessment Model', senior management would document the top five to ten risk events and then develop a response protocol and associated training requirements corresponding to each event.
In the aftermath of the Francis Scott Key bridge collapse, companies with contingency and crisis management plans put them into action. Communication, quick decision-making and adaptability were critical to keep businesses operating and minimize exposure to their day-to-day operations.
Due to transportation routes being blocked, companies were forced to find solutions in rerouting their products and learn just how effective and resilient their contingency plans were. Utilizing alternate modes of transportation which included rail and additional trucking became essential to continue the flow of goods to their destination points. (Due to the type of cargo involved at the Port of Baltimore, air transport was not an effective mode of transport.) While these alternatives come with price hikes and delays in lead times, they allow supply chains to move and meet commitments.
The Baltimore bridge tragedy is an abrupt reminder of how vulnerable global supply chains are and the importance of being prepared when faced with unexpected events and disruptions. In addition to utilizing different modes of transportation for moving products, the utilization of alternate routes and ports serves as another means to lessen the impact of disorder and create flexibility within the supply chain. The recent capital investments to most of the ports along the East Coast served as essential to take and transfer cargo bound for the Port of Baltimore. According to the state of Maryland, the Port of Baltimore handles the majority of the U.S. East Coast market’s share of roll on/roll off cargo annually which is expensive to move, accommodate and requires special care. Therefore, having the flexibility to reroute such cargo to ports in Savannah, Norfolk and New York was imperative in keeping commerce active and moving.
Collaboration is a foundation for resilience. When companies, industry associations, governmental agencies and communities decide to forgo differences and work together in sharing and supporting each other through crisis, both pain and strain are alleviated, and it serves to expedite the restoration process.
Innovation was spurred in the aftermath of the bridge collapse as new and creative solutions were sought to overcome and navigate challenges. As technology continues to advance, such as real-time ocean traffic monitoring, issues now can be resolved quickly albeit at monetary costs and delays. Interoperability, which entails the seamless exchange of information among stakeholders in a supply chain network, is another innovative way whereby problems can be resolved promptly. An additional approach within the realm of innovation is utilizing generative AI in tracking the possession of cargo through the supply chain network. According to a report by Accenture, "This rising technology has potential for the entire supply chain, from design and planning, to sourcing and manufacturing to fulfillment and service." Future innovations will continue to lay the groundwork for supply chains to be more resilient and flexible.
Communication, quick decision-making and adaptability were critical to keep businesses operating and minimize exposure to their day-to-day operations. Resiliency in supply and demand management can also lessen impacts from unforeseen events. In an expert brief by the Council on Foreign Relations, the author cites several ways to strengthen resilience within the supply chain from the supply side: "Unexpected supply disruptions can be cushioned by maintaining an appropriate level of excess inventory, creating emergency stockpiles or strategic reserves, diversifying supplier sources and manufacturing facilities and preserving spare production capacity."
As contingency plans have taken shape and the immediate crisis subsided, supply chain professionals will now turn their attention to future planning and preparedness. Having conducted evaluations to assess how effectively their plans worked and then identifying areas for improvement will provide invaluable insight going forward. The lessons learned should be incorporated into future risk management strategies and plans.
The Baltimore bridge tragedy is an abrupt reminder of how vulnerable global supply chains are and the importance of being prepared when faced with unexpected events and disruptions. While causing significant impacts, it challenged companies to continue to better their plans in resiliency, collaboration and innovation. Insights gleaned from the bridge collapse offer valuable lessons in improving these plans, whereby companies will emerge stronger and have a blueprint for navigating future disruptions with agile supply chains.
Project Announcements
ValorFlex Packaging Plans Bowling Green, Kentucky, Production Operations
06/30/2025
Neuro.io Plans Terrebonne Parish, Louisiana, Operations
06/30/2025
Germany-Based MTU Maintenance Expands Fort Worth, Texas, MRO Operations
06/30/2025
Cascade Die Casting Group Expands High Point, North Carolina, Manufacturing Operations
06/30/2025
BuildOps Plans Raleigh, North Carolina, Operations
06/30/2025
Point Blank Enterprises Plans Wakulla County, Florida, Operations
06/30/2025
Most Read
-
20th Annual Area Development Gold and Silver Shovel Awards
Q2 2025
-
First Person: Joe Capes, CEO, LiquidStack
Q2 2025
-
The Legal Limits of DEI in Incentives Agreements, Hiring, and Contracting
Q2 2025
-
From Silicon to Server: Mapping the Data Center Supply Chain
Q2 2025
-
39th Annual Corporate & 21st Annual Consultants Surveys: What Business Leaders and Consultants Are Saying About Site Selection
Q1 2025
-
Rethinking Life Sciences Site Selection in a Resilient and Dynamic Market
Q2 2025
-
Top States for Doing Business in 2024: A Continued Legacy of Excellence
Q3 2024