Manufacturing’s Last “KISS”
Although those in the aerospace and other industries once believed that the simplest solution to a production problem was undoubtedly the optimal one, it often creates inefficiency in design and production that makes for a competitive disadvantage in today’s global marketplace.
2022 Auto/Aero Site Guide
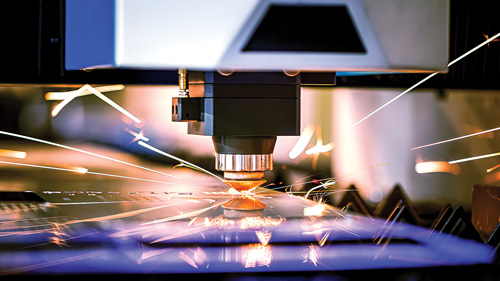
The gentleman, a retired attack submarine commander, had a divine organizational chart on his wall showing God above Christ and the Holy Spirit, with Fast-Attack Submarine Commander drawn in as an intervening authority between the Creator and the rest of the Holy Trinity. He was clearly a Theory-X manager in today’s vernacular, but we all loved him regardless. The Vietnam era guys wore their emotions on their sleeves, but no one ever had your back more than an ex-military program manager. However, any correlation between him and “KISS,” other than as part of the occasional expletive phrase, seemed utterly non-cohesive.
When I didn’t respond immediately and looked a bit confused, he turned his attention up from his production scheduling manifest and smiled. Mr. Troan, he said, “There are two answers to this question, one is yes, the other is no; one is right, the other wrong...and you have 30 seconds to make up your mind.” When I still failed to respond, it was he who looked a bit confused, asking, “What’s wrong Mr. Troan?” I replied, “Sir, yes sir, nothing…with due respect, by my watch I still have 25 seconds left to figure this out.”
The “Keep It Simple Stupid” Solution
Kidding aside, later an old ME explained to me that the Captain was looking for the K.I.S.S., or Keep It Simple Stupid solution to the problem, under the assumption that the simplest solution to his production problem was undoubtedly the optimal one. The term and concept have their origins in the aerospace industry, in particular, in the person of Kelly Johnson. Johnson was a vaunted aerospace designer in the 1930s–1960s, recognized as the honorary fifth father to Lockheed Martin Corporation, behind the Loughead Brothers (Alan, Malcolm, and Victor — pronounced Lockheed) and Glenn L. Martin. His story is a familiar one. He was one of nine children, birthed to a poor Michigan immigrant farmer, who worked his way through the University of Michigan School of Engineering, only to find himself an unemployed engineering graduate at the onset of the Great Depression. He longed to design aircraft, and so on a whim, he and a friend took the train to Los Angeles to try and get work in the early aircraft industry that was growing in Southern California.
At that time, the Lougheads’ aircraft company had just been bought out of receivership by a group of investors who saw promise in some of the 1909 company’s technology and patents. Meanwhile, Glenn Martin was literally living in his production facility (he had an apartment/office in the facility), busy constructing the first of the China Clippers, a project to build an airliner that could serve China from San Francisco that nearly bankrupted Martin Aircraft.
The term K.I.S.S. — Keep It Simple Stupid concept — has its origins in the aerospace industry. After a number of unsuccessful interviews with the owners of the new Lockheed Aircraft Company, the financiers finally gave in to hiring Kelly as one of the rejuvenated company’s first design engineers. Kelly made a name for himself quickly. At the ripe old age of 28, he successfully redesigned an early Lockheed all metal airliner airframe to function as an antisubmarine warfare platform and sold 200 of them to the British Ministry of Defense, by accosting their delegation at the train station and begging them to consider the Lockheed design. Johnson went on to design the P38 Lightning Fighter, the Lockheed Constellation, and the U2 and SR-71 Reconnaissance Aircraft among other significant design challenges, and finished his career with the conceptual work on the first stealth fighter, the F-117 Nighthawk.
Wikipedia cites Kelly Johnson as the original purveyor of the KISS principal, and he also references the term and concept in his autobiography published in 1989, so we can reasonably attribute the acronym to Johnson. The problem is that Johnson never designed anything that was in any way simple or utilized simplistic design. Take, for example, his design for a high-speed, long-range fighter in World War II, the P-38 Lightning versus North American Aviation’s P-51 Mustang.
The P-38 uses two engines on twin booms with a third fuselage for the pilot, a twin rudder tail configuration, and tricycle landing gear. The P-51 uses a standard configuration with a tail wheel and a “big-assed” high-output Rolls Royce Merlin engine to match/exceed the range and speed of the P-38. Granted Johnson started his design ahead of North American, but there is no way you can justify the P-38 as a KISS design versus the P-51.
The complexity of his aircraft only accelerated after the P-38, as he dealt with first “air compression” and then “mach sound barrier waves” pushing aircraft speeds through mach-1 up to mach-3+ with the SR-71 Blackbird. Then he finished his career exploring the roots of stealth aircraft resulting in the F-117 black jet, which used an origami-like airframe design to evade radar (pilots nicknamed it “the Wabbly Goblin” because its flight characteristics were so complex).
A Misinterpreted Concept
Johnson was legendary, and by the 1950s, his KISS Acronym was catching on in the military and the aerospace industry in general. By 1965, program managers from cereal box companies to automobile manufacturers were expounding on the value of KISS solutions for engineering and production problems, and the popularity of the KISS solution continues to the present day.
The problem with implementing KISS concepts in today’s manufacturing environment is two-fold: 1) Johnson’s concept is often misinterpreted; and 2) the market has changed; it’s much more competitive.
When I see a KISS solution being implemented in today’s manufacturing environment, it is often interpreted by management as a means of simplifying their decision-making by excluding certain secondary and tertiary decision criteria from their solution. For example: “We don’t need to look at tax or workforce pipelining as part of the site selection; we need to get a production line running,” or “Why bother looking at new locations when we have a half-empty plant that’s losing money?”
Program managers often see KISS as a justification to eliminate complexity in decision-making, usually to concentrate solely on finishing a design or accelerating production readiness. If we express the optimal solution (OBS(X)) to a business problem as a mathematical equation, the best solution is derived as the sum of the production variables (PV) multiplied by their relative coefficients (C) — OBS(X) = (C1 x PV1) + (C2 x PV2) + (C3 x PV3).
Kelly Johnson’s concept was to eliminate only any C*PV combinations which have a negligible impact on OBS(X). He would never have advocated ignoring production variables that materially impacted product performance, defined by W. Edwards Deming (father of Total Quality Management), as a product that meets the customer’s minimum technical specification at or ahead of schedule at the lowest possible cost.
In popular usage today, we’ve extended the KISS concept to go well beyond negligible items to production variables that have a significant impact on long-term business performance. Program managers often see KISS as a justification to eliminate complexity in decision-making, usually to concentrate solely on finishing a design or accelerating production readiness. By definition, unless you’re extremely lucky, that creates inefficiency in design and production, and that can mean you never reach an optimal production model.
The Market Has Changed
In the United States, in the 1950s and 1960s, you could get away with such a semi-optimized model; today you can’t. The 1950s–1960s was a “happy time” for American manufacturing. The country had just come out of WWII as the only heavily industrialized country not severely damaged by the war. Further, we were operating at full production capacity, with a huge artificial export market created by the Marshal Plan in Europe and Asia. Back then, if you wanted to buy consumer goods anywhere in the world, you were buying them from the United States, at the U.S. firm’s prices and quality levels.
As the 1960s drew to a close, the U.S. production monopoly was coming to an end with the reemergence of the United Kingdom and West Germany, and the emerging powerhouse of Japan. Western Europe then followed West Germany, and South Korea then followed Japan. The Soviet Union collapsed, and Eastern Europe joined the capitalist fray. NAFTA then encouraged capacity-building in Mexico and Canada. Finally, the Chinese and Indians, seeing the writing on the wall, also adopted Total Quality Management (TQM) and capitalist economic principles.
As a result, businesses today compete with companies from over 150 countries on six continents worldwide. The capitalist economic system (more often than not a laissez-faire capitalist economic system) that Britain, France, and the United States sold the world is now universally recognized as not only the premier but also the only feasible economic system on which to found a healthy economy. As Deng Xiaoping so aptly put it concerning the People’s Republic of China, “If we are going to progress as a nation, I guess some of the people are going to have to get richer first.”
Modern analytic site selection and Total Quality Management processes evaluate every production variable to avoid the inherent inefficiencies of a KISS. The laissez-faire capitalism that the United States has espoused now for nearly two-and-a-half centuries is indeed wonderfully effective at growing an entire commonwealth’s affluence, and so far, it’s proven to be the only viable economic system out there, regardless of its paired political system. However, capitalism’s wonderful effectiveness is driven by its ruthless efficiency. By definition, a laissez-faire capitalist system will tirelessly relocate all production of a given good or service to those providers, and those locations, able to produce the product to the customer’s specification, at or ahead of schedule, at the lowest possible cost.
Improvements in workforce development and pipelining practices across the globe have greatly increased the number of viable locations where any product, even very technical goods and services, can be produced. The United States no longer holds a monopoly on production capacity and workforce demographics, and the country is in many instances an expensive option for continued production.
In the 1950s and 1960s, a U.S. manufacturer could afford to absorb numerous inefficiencies in quality, the production process, and the underlying business/tax climate. Today, the efficiency of global markets ensures that any inefficiency in production will be exploited by competitors, often turning a sizable production investment into a slow bleed to financial extinction. An investment mistake via a KISS solution may create a competitive disadvantage that can never be overcome.
However, there is no need for despair. Modern analytic site selection and Total Quality Management processes evaluate every production variable from process efficiency to workforce demographics and tax climate to avoid the inherent inefficiencies of a KISS, and economic development business incentives programs can be applied to negate production and business climate inadequacies.
Nevertheless, unfortunately, for those of us who design new products or establish new production lines, I’m afraid we’ve seen our last KISS .
Project Announcements
Otto Aviation Plans Jacksonville, Florida, Manufacturing Operations
06/20/2025
Howmet Aerospace Expands Morristown, Tennessee, Production Operations
06/18/2025
Kratos Defense & Security Solutions Expands Bristow, Oklahoma, Manufacturing Operations
06/18/2025
JetZero Plans Greensboro, North Carolina, Headquarters-Production Operations
06/17/2025
Rolls-Royce Expands Mankato, Minnesota, Manufacturing Operations
06/12/2025
StandardAero Component Services Expands Sharonville, Ohio, MRO Operations
06/12/2025
Most Read
-
20th Annual Area Development Gold and Silver Shovel Awards
Q2 2025
-
First Person: Joe Capes, CEO, LiquidStack
Q2 2025
-
The Legal Limits of DEI in Incentives Agreements, Hiring, and Contracting
Q2 2025
-
From Silicon to Server: Mapping the Data Center Supply Chain
Q2 2025
-
39th Annual Corporate & 21st Annual Consultants Surveys: What Business Leaders and Consultants Are Saying About Site Selection
Q1 2025
-
Rethinking Life Sciences Site Selection in a Resilient and Dynamic Market
Q2 2025
-
Top States for Doing Business in 2024: A Continued Legacy of Excellence
Q3 2024