Revitalized Cities: Which Locations Have Outperformed and Why?
Many locations that saw economic contractions have been able to revitalize themselves by instituting pro-business policies, developing innovative workforces, and drawing the right industry mix — sprinkled with a little bit of luck!
Q1 2020
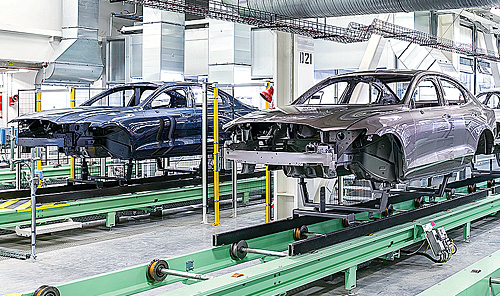
Because most U.S. cities saw a return to economic growth in 2010 following a painful contraction in 2009, it’s sensible to define the current business cycle as 2010 through 2019. To be sure, U.S. metro performance has varied widely during this period. Places that saw the greatest expansion from 2010–2019 were generally clustered along the West Coast, in Texas, and throughout the Intermountain West. In contrast, 59 metros — 15 percent of nation’s 382 metropolitan areas — have a smaller economy today than in 2007. These laggards can generally be characterized as smaller cities with a manufacturing legacy, and more than 60 percent of them are in either the Midwest or Southeast regions.
This backdrop has created the widely touted narrative of “left-behind” industrial centers in the Heartland versus high-tech coastal enclaves filled with bright young programmers. While this story is easy to distill into a headline, the reality of America’s post-global-financial-crisis economic geography is more nuanced.
Some communities far away from Silicon Valley, New York, or Boston have experienced an impressive turnaround during the past decade — by having the good fortune to host the right industry mix, employing aggressive economic development policies, and mobilizing their labor forces.
Frankly, luck should not be dismissed as a factor in economic development. What would Seattle be like today if Bill Gates was not from there? Would Boston be more like Buffalo if it was not for MIT? Some of the fastest-growing cities of recent years have been places where the underlying geology was “ripened” by the emergence of new fracking technologies. Other metros have benefitted from events elsewhere entirely — such as the combination of immense wealth creation and restrictive zoning policies in coastal California, which has pushed many middle-income households to other cities across the West.
The implications for Bend, a small “outdoorsy” metro in central Oregon, have been dramatic. When its home values fell 45 percent from 2008 to 2011, Bend’s construction industry was decimated. In 2009, the unemployment rate hit 15 percent. Yet today, an influx of newcomers — especially telecommuters from the San Francisco Bay Area — has sparked a turnaround. In 2019, Bend’s population grew by an estimated 2.7 percent, making it the third-fastest growing U.S. metro; and its unemployment rate is now in the low 4 percent range.
Increase Demand for Manufacturing Goods
Just as revived real estate investment supported a turnaround in Bend’s economy, increased global demand for manufacturing goods has revitalized midwestern metros that are fortunate enough to have the right industry base. A well-documented example is Elkhart, Indiana, whose unemployment peaked at 17.9 percent in 2009, yet is currently at about 3 percent, thanks to the growing popularity of motor homes (a very labor-intensive product) from both retiring boomers and footloose millennials.
There is a very small group of U.S. cities that offers both a highly skilled workforce and a relatively low-cost structure, allowing both migrants from elsewhere and lower-margin industries to participate in local growth. Other midwestern cities that produce feedstock and capital goods for export have also bounced back. For example, GDP in Midland, Mich., contracted by just over 3 percent during the recession, far greater than the U.S. average of 1.3 percent. But this small metro has since achieved 4.4 percent annualized growth between 2010 and 2019, supported mainly by sturdy demand for chemicals (DuPont employs several thousand here).
Similarly, the economy of Grand Rapids, Mich., contracted by 5.7 percent per year in 2008–2009 — but since then, the combined success of its auto parts suppliers, office furniture firms, and pharmaceutical manufacturers has all contributed to the city achieving 3.1 percent annualized growth.
Historically, the Midwest’s focus on heavy industry has contrasted with manufacturing in the South, which has generally produced lower-value, labor-intensive products — such as furniture and textiles — that are especially vulnerable to globalization. While these legacy industries still have a presence in the South, they no longer drive the region’s growth. Instead, its manufacturing base has quickly tilted toward aerospace, motor vehicles, and capital goods production.
This transition is partly due to the region’s pro-business policies, such as right-to-work laws and a light-touch regulatory and tax environment. It has enabled some of the region’s premier manufacturing clusters to rebound quickly from the depths of the recession, while more traditional centers have remained weak — manufacturing output in Dalton, Ga. (textiles) and Hickory, N.C. (furniture, apparel) is presently some 7 percent lower than their 2006 output levels.
A key winner in the region is Spartanburg, S.C., whose economy contracted by around 6 percent during 2008–2009. The area has long hosted major European companies such as BMW and Michelin, and rising auto sales both domestically and abroad have since supported average annual GDP growth for the city of 3.4 percent.
A sizable share of the BMWs produced in Spartanburg are exported via the Port of Charleston, which in turn is a factor behind the success of the wider metro region of Charleston in this cycle — exhibiting annual GDP growth of around 4 percent since 2010. Another key catalyst here was Boeing opening its 787 assembly plant in 2011.
South Carolina has employed aggressive financial incentives to attract manufacturers, such as having no corporate income tax, and not taxing machinery or international sales. Another important factor is the state’s efforts to mobilize a manufacturing workforce: in a country where some half-million manufacturing jobs remain unfilled, South Carolina subsidizes workforce training via its readySC program, which pairs workers with manufacturers.
Workforce Is Key
Workforce quality is paramount to local success. While highly educated cities such as San Jose, Seattle, and Boston have all seen exceptional growth driven by increased public and private investment in technology, possessing well-rounded and innovative workforces has also been crucial to their success during the past several business cycles. The tech crash of 2000 did not kill-off Silicon Valley; instead, the region’s engineers reenergized it with smart phones and cloud computing. This is in stark contrast to local economies that are adept at making only one type of “widget” — a problem faced by many U.S. manufacturing hubs.
The South’s manufacturing base has quickly tilted from lower value, labor-intensive products (e.g., furniture and textiles) toward aerospace, motor vehicles, and capital goods production. A key constraint to the ongoing growth of superstar tech cities is their high cost structure (e.g., house prices, office rents, and labor costs). There is, however, a very small group of U.S. cities that offers both a highly skilled workforce and a relatively low-cost structure, allowing both migrants from elsewhere and lower-margin industries to participate in local growth. This rarefied shortlist includes Raleigh and Denver, whose economies are now around 40 percent larger than in 2007, as well as Austin, whose economy is nearly 80 percent larger. Similarly, other relatively low-cost cities that are also seeing some success at incubating early-stage tech clusters include Salt Lake City and Pittsburgh.
Macroeconomic Headwinds
Many of these revitalization stories are, however, now losing momentum due to macroeconomic headwinds — notably, trade policy uncertainty and weaker global growth, which are constraining business spending on machinery and equipment (expected to decline by 0.3 percent this year). This is already weighing on capital goods manufacturing clusters across the Midwest and South. In contrast, places with a focus on information technology should fare better, as investment in intellectual property remains heightened, growing by roughly 5 percent this year. However, this is a downgrade from the 7+ percent growth experienced in recent years.
It should be reinforced that just as macro risks can weigh on local growth, the ability of cities to regenerate themselves can also be down to happenstance. But there are, of course, active strategies cities can employ to attract growth and recover from hardship:
(1) Creating an environment that allows the existing industrial base to thrive and easily react to market forces by designing an efficient tax and regulatory environment is important;
(2) Inviting new industries and people in — by keeping barriers-to-entry low — has been an important feature of many cities that were able to generate outperformance since the financial crisis; and
(3), having training strategies that pair the skills of people with the needs of local industry is key.
From manufacturing to computer science, recruiting skilled technicians is a systemic problem. For many sectors this third point trumps the previous two as advanced manufacturing, research and development, and other skilled functions are often willing to endure higher taxes and rents to recruit the right type of people.
Oxford Economics produces economic forecasts and analysis for more than 3,000 cities globally and offers comprehensive coverage of all U.S. states, metros, and counties.
Project Announcements
AVAIO Digital Plans Brandon, Mississippi, Data Centers Operations
08/21/2025
Schütz Container Systems Establishes Kenosha, Wisconsin, Production Operations
08/21/2025
GE Vernova Expands Charleroi, Pennsylvania, Operations
08/18/2025
Busch Vacuum Solutions Plans Tempe, Arizona, Operations
08/18/2025
Made Scientific Establishes Princeton, New Jersey, Manufacturing-Headquarters Operations
08/18/2025
Comcast Establishes West Palm Beach, Florida, Operations
08/17/2025
Most Read
-
Tariffs, Talent, and U.S. Expansion
Q3 2025
-
What We’re Getting Wrong About Gen Z’s Future in the Skilled Trades
Q3 2025
-
A New Course for U.S. Shipbuilding
Q3 2025
-
Optimizing Your Rail-Served Transportation Network: Strategy Before Steel
Q2 2025
-
In Focus: AI Is Changing Incentives Math
Q2 2025
-
Rewriting the Rules of Warehouse ROI
Q3 2025
-
How to Choose the Right Site for Your Factory in 2025’s Volatile Landscape
Q2 2025