According to the latest data from the Bureau of Labor Statistics, food and beverage manufacturing accounted for more than 1.5 million wage-and-salary jobs in the United States in 2015. Construction and expansion of food processing plants not only play a major role in providing markets with employment opportunities but also have a significant and direct impact on the industrial real estate sector. This article will explore paradigm shifts in food processing, how they are impacting site selection, and the resulting opportunities for property owners and investors.
Drivers of Change
- Food safety and regulation: Food safety is job number one for food and beverage manufacturers and, with longer supply chains and more complex food sourcing, that job is becoming more complicated. January 2016 marked the fifth anniversary of passage of the Food Safety Modernization Act (FSMA), and with enforcement of FSMA regulations beginning to phase in, manufacturers are focused intently on it. The FSMA is a paradigm shift for the industry. Along with the FSMA, the FDA is moving from the old food safety approach that reacted to potential harm to a new, preventive framework that puts greater responsibility on the food industry.
- Plant efficiency: Efficient plant production has always been important, but it is becoming critical to long-term survival as producers pursue both traditional and new, faster-growing distribution channels. Incorporating more technology into food production and packaging processes is becoming more widespread. Among the technologies making their way to the production line are advanced robotics capable of automating manual processes; sensors incorporated into labels; packaging to determine product freshness; and information systems that offer solutions to specific pain points. Equipment and production line operations are also becoming more complex with the increased interest in organic and natural foods, which must be handled differently.
- Cold storage: Over the past five years, public refrigeration space increased 2 percent and private space increased 5.3 percent. Alongside the growth in cold storage is increased demand for transportation infrastructure capable of handling temperature-sensitive products. Consumer demand for locally sourced foods, along with the desire for freshness, has changed the way in which food is packaged and is a major force in the requirement for refrigerated space. Energy consumption has also hit the forefront for cold storage providers, as it comprises a substantial portion of operating costs. Although the focus on energy consumption itself is not new, the tools and strategies to achieve it keep evolving.
- The young and the old: Given the highly competitive nature of food manufacturing, capturing the favor of millennials — the fastest-growing consumer segment — may be the biggest challenge facing food executives. Given the sheer number of millennials, as they go so goes the food industry. Case in point, over the past decade, consumption of fresh foods grew by more than 20 percent, and millennials are a big reason why.
Another group driving change in food and consumption patterns is the baby boomers. This generational group is aging, retiring, and developing health ailments, all of which are typically associated with major changes in approach to food and beverage consumption. Taken together, consumers are increasingly more concerned as to where their food is coming from: is it sustainable and is it good for them?
As the economy continues to strengthen, and in response to the food and beverage manufacturing industry’s revolution, manufacturing inventory is growing at an accelerated pace in key markets across the United States. From 2011 to 2015, 1,691 food processing project announcements were made, including 1,033 expansions and 658 new projects. In 2015 alone, 249 expansion projects and 155 new projects were announced — the largest total food manufacturing project announcements in the past five years. We expect this trend to continue, with the 2016 tally surpassing that number.
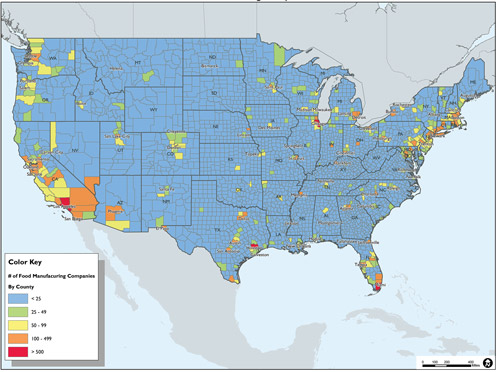
Notable new projects include Duke Food’s 150,000-square-foot plant in Texas and Clif Bar’s 300,000-square-foot bakery in Twin Falls, Idaho. Many newly announced projects result from the drive by food manufacturers to gain efficiency following mergers and acquisitions. They are closing smaller (older) plants and constructing larger regional facilities. A prime example involves the recent acquisition of Friendly’s Ice Cream, LLC by Dean Foods and the closure of facilities in Orem, Utah; Buena Park, Calif.; and New Orleans, Louisiana; and the transfer of those operations to St. George, Utah.
Challenges and Solutions
This trending, in turn, has led to the obsolescence of many manufacturing plants. It has become increasingly challenging to secure new manufacturing tenants for these assets because the work needed to meet a new tenant’s layout and use can be cost- and time-consuming. This is especially true for cold storage facilities that have gone dark. Once buildings are vacant and not seen by a maintenance tech daily, they tend to deteriorate very quickly, which can complicate the re-commissioning and re-certification process, with higher capital investments needed. What is the next chapter for these properties? We are seeing several stories unfold.
The first involves strong momentum among local and regional food processors. These smaller manufacturing operations are far more likely to consider second-generation product, provided the geography and the building bones meet their needs. For example, our team is marketing a 129,600-square-foot facility in western Georgia. The seller is an international frozen food processing company that supplies frozen products to major chains; the company recently built a new, larger facility to accommodate organic growth. The older facility is being pursued by several regional users for whom an affordable retrofit of the building would accommodate their needs. From 2011 to 2015, 1,691 food processing project announcements were made, including 1,033 expansions and 658 new projects. In 2015 alone, 249 expansion projects and 155 new projects were announced — the largest total food manufacturing project announcements in the past five years.
Investors are also re-purposing buildings speculatively. A perfect example is a former Miller International Foods bakery located in Lithonia, Ga. Earlier this year, Mark Cusumano, president and CEO of FW Warehousing, purchased the 180,000-square-foot building at auction for pennies on the dollar of reproduction cost. Like most factories, the facility was cut up into sections to accommodate different stages of product processing. The new ownership blew out the walls and reconditioned the floors to accommodate a warehouse/distribution use. The lower cost basis justified the capital investment to re-purpose the property, which was quickly re-tenanted by Home Chef, a meal kit delivery service, under a long-term lease.
Both cases illustrate how available facilities are being targeted by companies that are retrofitting for other food uses. Demand for existing, older plants is also being driven by emerging industries, which may use second-generation product as a stepping-stone for growth.
When re-purposing manufacturing product, the existing infrastructure often helps determine the future use. For instance, a former ice cream manufacturing property in Sacramento, Calif., now houses a craft brewery, a cold storage facility, and a specialty meatpacking operation. The new tenants benefit from the heavy power, freezer space, and water and water discharge capacity built into the original use. In Baltimore, a 161,000-square-foot former margarine production plant now houses a commercial laundry operation (another heavy water intake and discharge use). According to the latest data from the Bureau of Labor Statistics, food and beverage manufacturing accounted for more than 1.5 million wage-and-salary jobs in the United States in 2015.
Leveraging Opportunity
What are the key takeaways for property owners and investors? Ground-up development is the choice of major food manufacturers. At the same time, we are seeing a strengthening market for re-tenanting existing manufacturing facilities with regional food processing companies, or re-purposing properties for other uses (particularly those requiring robust utilities infrastructure and permitting).
When assessing the viability of a property for a pure food manufacturing reboot, it all comes down to cost of replacement. Does the price tag of installing new equipment and amenities justify the investment? Does the building have the right bones, such as slanted floors with working drains? Can it support modern loading and offer ample truck parking? Looking deeper, why was the property shut down in the first place? Was it shuttered appropriately, with compressors purged correctly and pest control preventatives put in place?
Location is also key. Municipal utility rates and permitting policies should be major considerations, along with the availability and cost of labor. Proximity to highways/freeways and rail is paramount for efficient product distribution. This is more pertinent today than ever before, as many food manufacturers are consolidating their distribution networks to gain supply-chain efficiency.
If food is no longer a viable option, will the space work for a different type of manufacturing? Better yet, does it provide competitive advantage in terms of in-place systems or permits? Does it offer the kind of close-in access to population centers — or shipping hubs — that the red-hot e-commerce sector is seeking as it works to meet next-day and same-day delivery demand? In that case, a manufacturing-to-warehouse adaptation might be a lucrative answer.
Looking ahead, we anticipate that this “next chapter” momentum for older manufacturing product will continue to grow as property owners — and tenants — seek creative solutions to meet diverse demand in supply-constricted markets nationwide.