Front Line: Manufacturers Look to Nontraditional Locations
As the labor supply tightens, nontraditional manufacturing hubs are upping their game by investing in workforce training programs.
Q3 2019
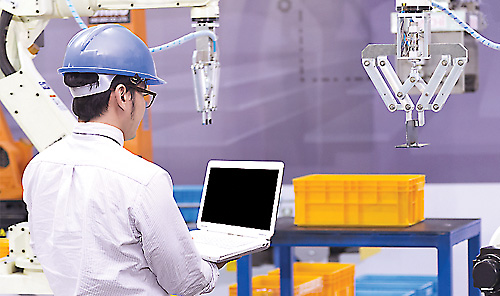
We’ve heard the political drumbeat: jobs, jobs, jobs! Politicians campaigning in the 2020 elections will beat that drum even louder.
President Trump claims that his administration is “restoring jobs” and that states and counties that were depressed under the Obama administration are now experiencing strong growth. Yet a June 13, 2019 article in The New York Times entitled “In the Race for Factory Jobs Under Trump, the Midwest Isn’t Winning” points out that the vast majority of manufacturing jobs Trump claims his policies have added are actually in the West and oil-rich areas rather than the industrial Midwest.
The article cites the Economic Innovation Group, a Washington think tank that studies regions and advocates for new economic development policies, but “if you don’t look behind the numbers or at different numbers, you aren’t getting the entire picture” warns Michelle Comerford, project director and Industrial & Supply Chain Practice leader at Biggins Lacy Shapiro & Co.
“Data in the referenced Economic Innovation Group study actually tells a different story,” she notes. Comerford emphasizes how nearly every part of the country — including “traditional hubs” in the Midwest — is seeing activity. However, manufacturers are increasingly turning to outlying areas for new growth.
Site selection decisions are complex. “Some of our clients much prefer to be a ‘big fish in a smaller pond’ as opposed to being in a location where there’s a lot of concentrated, direct competition for workers,” Comerford observes. In short, nontraditional locations are increasingly considered for manufacturing and are seeing growth.
Finding Skilled Labor
Today’s manufacturing activity is extremely diverse. Projects run the full gamut from biotech and pharmaceutical to environmental tech and food-processing, to traditional industrial supply and those that are utility-related, and more. But despite this diversity, the number-one common denominator to all site selection decisions today is availability of skilled labor.
“It’s not an issue of sheer numbers, but needed skills,” Comerford explains. “Manufacturers want to know where they can find the skilled workers that they need to operate or maintain equipment both today and in the future.”
For years, traditional hubs have been attuned to developing workforce needs. But today, nontraditional hubs are also investing in workforce training programs to up their game to meet manufacturer needs. This has increased company location options.
Driving much of the training is automation. “Manufacturing plants today have a much higher level of automation than even 10 years ago,” Comerford says, but “workforce needs have changed considerably.”
This brings us back to political chest-beating over number of jobs created. Manufacturing lost six million jobs from 2000 to 2010 as companies moved low-skilled jobs offshore. About 1.5 million manufacturing jobs have been since added back, but not necessarily in the places that lost them. And with automaton, job creation is not really accelerating. So claims of manufacturing job growth, particularly in the Midwest, are a misnomer. The added jobs aren’t the low-skilled ones that were lost.
“Automation is what makes manufacturing viable in the United States today,” concludes Comerford. “Companies are not beholden to low labor wages. But they need people with higher skills and are paying them more.”
Project Announcements
Wyandot Snacks Expands Marion, Ohio, Production Operations
08/29/2025
Trane Technologies Expands Fort Smith, Arkansas, Operations
08/29/2025
BioMADE Plans Boone, Iowa, Bioindustrial Manufacturing Operations
08/29/2025
Choice Fabricators Expands Rainbow City, Alabama, Production Operations
08/29/2025
Ranovus Expands Ottawa, Ontario, Semiconductor Operations
08/29/2025
Belgium-Based Stow Group Plans Gordon County, Georgia, Manufacturing Operations
08/28/2025
Most Read
-
Tariffs, Talent, and U.S. Expansion
Q3 2025
-
What We’re Getting Wrong About Gen Z’s Future in the Skilled Trades
Q3 2025
-
Data Center Demand Stabilizes Amid Changing Market Forces
Q3 2025
-
A New Course for U.S. Shipbuilding
Q3 2025
-
Optimizing Your Rail-Served Transportation Network: Strategy Before Steel
Q2 2025
-
In Focus: AI Is Changing Incentives Math
Q2 2025
-
Rewriting the Rules of Warehouse ROI
Q3 2025