A Constant Pain Point
With unemployment benefits having ended for millions of Americans on September 5, it remains to be seen how labor markets will respond. The COVID-19 pandemic sparked the acceleration of e-commerce/online shopping demand, which drove a greater need for space in the industrial real estate world. This acceleration also brought about labor challenges for the industrial and manufacturing sectors. Though it’s been an issue throughout the current expansion, finding, training, and retaining an efficient industrial workforce remains a constant pain point for most distributors and manufacturers.
At the end of the summer, warehouse employment reached a new high after a months-long dip, but companies are still scrambling to keep pace with demand. There were 1.44 million workers in the warehouse and storage industry in July, according to the Bureau of Labor Statistics (BLS). This surpassed the previous record high set in November 2020 and is the third consecutive month employment in the sector has grown. Even with the surge in employment, many companies continue to face hiring obstacles today.
Factors such as substantial unemployment benefits continuing in most states, lack of affordable childcare, school closures due to exposure, and constant pandemic-related health concerns have made staffing warehouses and manufacturing facilities more difficult.
As e-commerce has become more prominent, its seasonal influence on hiring patterns throughout the year has followed suit. Seasonal demand for workers has become more acute during the holiday period, with November to January being the most impacted. This also has resulted in a greater number of seasonal layoffs during the spring, with April to June most prominent. Occupiers who are trying to attract talent in warehousing/final mile — whether e-commerce related or not — will find certain months of the year to be more challenging than others. For these reasons, retention will be critical.
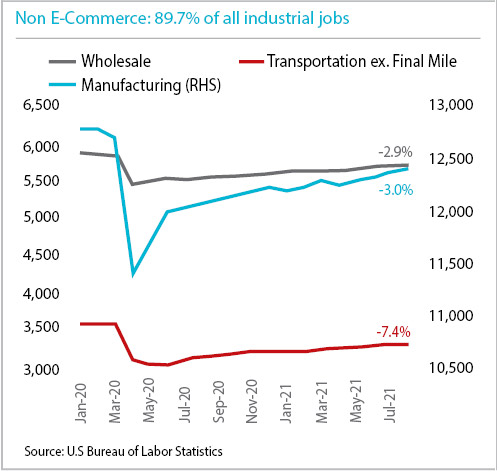
Despite high unemployment rates brought on by the pandemic, manufacturers are also having trouble filling entry-level roles. Between December 2020 and February 2021, The Manufacturing Institute and Deloitte surveyed over 800 U.S. manufacturers about hiring. They found manufacturers are having trouble filling 46 percent of open positions due to a mismatch in skills — a 12 percent increase over the 2018 survey. This is believed to be caused by competition in the warehouse/distribution sector and by automation. Manufacturers would benefit by beginning to look to tech and automation as not just replacing workers but creating new jobs and programs that are better for workers and higher-paying. U.S. manufacturers need to prioritize retraining programs, access to STEM education, and training on vocation/trade skills if they want to attract labor to their industry.
With the holiday season just around the corner, it will become increasingly difficult to find seasonal workers as well as to retain top talent among companies. With the pandemic still impacting the country, online shopping is likely to be popular again this year. Demand may require temporary labor to manage the influx of orders. Solving for the immediate need is the priority, but as seasonal demands turn into longer stretches of time throughout the year, a more strategic approach may be warranted.
As e-commerce has become more prominent, its seasonal influence on hiring patterns throughout the year has followed suit. Companies with warehousing needs are responding to the shortage in a variety of ways. One of the top ways is increasing hourly pay. The preliminary average hourly earnings in the industry were $22.47 in June 2021, up from $21.99 in March, according to the BLS. The Wall Street Journal recently reported that logistics executives were increasing wages for e-commerce workers, jumping from between $13 to $15 an hour in recent years to as much as $19 an hour in some markets, led by the sector’s biggest operators.
Another approach to solving labor challenges is to consider automation and robotics to supplement the labor force. Sorting systems in e-commerce hubs can increase sortation speeds and help current employees more easily complete tasks. Though it can be an effective solution, the capital investment is large. In MHI’s annual report with Deloitte, the percentage of supply chain and manufacturing leaders reporting they were using automation and robotics was 38 percent in 2021, slightly higher than 35 percent of respondents in 2016. However, robotics was also one of the top three areas respondents were increasing investment in. Robotics have partially eased the sting of labor shortages, but many tasks still cannot be completed by a robot.
So how can warehousing and manufacturing companies work to retain their workforce and attract new hires to meet their ever-evolving needs?
Share knowledge. Consider forming an informal group of human resources and operations managers among other local employers to discuss successful strategies for effective worker recruiting and retention. Ensure periodic and ongoing conversations with operations, facility management, HR, IT, and other stakeholders at the facility and corporate level to discuss future plans for operational improvements, automation, or anticipated changes in workforce requirements.
U.S. manufacturers need to prioritize retraining programs, access to STEM education, and training on vocation/trade skills. Diversify the labor pool. Consider potential worker pools in the community that remain untapped. The majority of industrial, warehousing, and manufacturing jobs are filled by men. There is potential to attract more women to the workforce by adjusting hiring practices and addressing other challenges that deter women from applying for these jobs.
Invest in training and education. Proper training is a necessity for developing efficient and savvy workers. It is extremely important that new hires be trained properly from the start. Retention could also be improved if workers have opportunities to take classes or complete courses that prepare them for advancement within the company.
Provide family-oriented benefits. As children have returned to school or daycare, there are still frequent outbreaks and situations where children need to be sent home or quarantined due to the pandemic. There is a strong possibility that workers may be supporting school-age children with virtual learning or may not have access to childcare or family/eldercare options, limiting their ability to go to an on-site job or to work the hours required. Offering flexibility in schedules and potential childcare options could be a differentiator in attracting labor.
Offering flexibility in schedules and potential childcare options could be a differentiator in attracting labor. Enable facility access/transportation. Before the boom of e-commerce, many large warehouses or manufacturing plants were traditionally in locations requiring a commute by car. Now it is essential for most companies to have an infill/last mile location for fulfillment in large metro areas. Shuttles, carpooling options, or access to public transit can make the commute easier and more appealing for workers.
The pressures on the industrial labor markets are real and lasting, and while there are many potential solutions and paths forward, the reality is that many companies are going to struggle to fill roles in the short- and medium-terms. The most successful firms will look at the problem holistically and be proactive with a range of strategies and tactics that compensate for the workplace challenges.