On a national level, Gross Domestic Product (GDP) growth and employment figures seem to contradict each other at times, perhaps due to this dynamic. Looking at where investor dollars are flowing suggests that the jury may still be out on whether we’re experiencing a true national manufacturing renaissance — or if it’s limited to a few key regions.
Are the Jobs Coming Back?
It’s no secret that the manufacturing sector has seen dramatic job loss over the last 30 years. While the mood is more upbeat these days for the sector generally, jobs are only slowly coming back. After all, advances in automation and other technologies have changed the nature of the work and reduced the functions that humans must perform.
Even if companies add manufacturing facilities, there will still likely be a continued slide from 12 million manufacturing jobs today to 10 million in 2028.
An October 2014 article in Bloomberg Businessweek notes that the U.S. has added 600,000 new manufacturing jobs since the spring of 2010, during a time when companies have been moving certain operations back from overseas. However, those jobs comprise only 8.7 percent of the total labor employment in the U.S., down significantly from 15 years ago when it was 13 percent.
The more labor-intensive manufacturing processes — think textile mills and furniture products — tend to stay offshore, where labor is cheaper. As you might expect, those same companies are also seeing lower-than-average GDP growth in the U.S. Typically, it’s the manufacturers with more capital- and talent-intensive plants — such as computer and electronic products — that are investing in the U.S.
That said, economic growth doesn’t necessarily translate to job growth. GDP growth is up 103 percent for electronics manufacturers since 2004, compared with 13 percent GDP growth across all industries. At the same time, more efficient manufacturing processes have kept employment growth at a slow pace, even when functions return to America. According to JLL estimates, even if companies add manufacturing facilities, there will still likely be a continued slide from 12 million manufacturing jobs today to 10 million in 2028.
So, why is there such a buzz about the shortage of skilled labor? Because tech-savvy workers are hard to find.
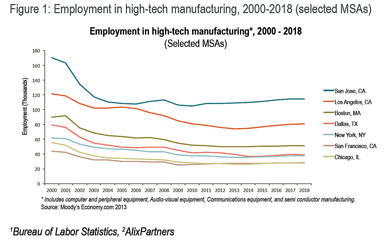
As a result, the manufacturers expanding in the U.S. are generally going where the technically trained talent lives. For example, the high-growth computer and electronic manufacturing sector tends to migrate to California and the U.S. Northeast, prioritizing their need for skilled talent above high labor and real estate costs.
Where Are Plant Investments Happening?
While the U.S. workforce is struggling to keep pace with evolving manufacturing processes, it is still very well positioned in the world and remains one of the largest recipients of foreign direct investment. The U.S. shale boom and the low price of natural gas have been a particular boon for the chemicals manufacturing industry. The American Chemistry Council reports that foreign companies account for 62 percent of announced capital investments in the U.S. chemical industry, with chemical-makers planning to invest a record $72 billion in U.S. plants, drawn to cheap and abundant natural gas in the region, according to Bloomberg. German-based BASF, one of the largest chemical-makers in the world, is planning its most expensive plant to date on the Gulf Coast, hoping to leverage the cost advantages of having easy access to a natural gas hub.
This skills gap is generational; legacy manufacturing employees were trained for the labor-intensive jobs that moved offshore, not the technical jobs that are available now.
Texas, Mississippi, and Louisiana have all become more attractive targets for manufacturing plants, given their proximity to the Gulf of Mexico and the natural gas industry. In July, Area Development reported that China-based Yuhuang Chemical was investing $1.85 billion in a methanol manufacturing complex in St. James Parish, Louisiana, to take advantage of natural gas feedstock.
Natural gas isn’t the only major draw to the U.S. market; so is having the ability to shorten the supply chain. As labor costs have gone up in China, manufacturers of heavy machinery and other heavy materials are finding multiple benefits in investing in the U.S., including shortened travel times to the end-market and lower transportation costs. JLL data finds that the East Coast is generally a more attractive area for large-scale manufacturing investment than the West Coast. One of the largest U.S. manufacturing investments in the last year was an announcement by China’s Shandong Tranlin Paper Co. to invest $2 billion over the next five years into a new factory in Virginia. Readily available utilities, transportation, and labor resources made it an attractive option.
Regional optimization and reshoring isn’t just good for America; one of the biggest beneficiaries will be Mexico. More companies are eyeing Mexico for its low costs, while still offering proximity to the North American consumer market. Recent news stories have touted Mexico as an emerging powerhouse in luxury car production, hosting new factories for BMW, Audi, and Mercedes-Benz since 2012. South Carolina and Tennessee have been the recipients of foreign automotive manufacturing investments in recent years as well.
Regional optimization and reshoring isn’t just good for America…More companies are eyeing Mexico for its low costs, while still offering proximity to the North American consumer market.
What Does It All Mean?
If the manufacturing process still relies heavily on people doing the work instead of machines, then companies will zero in on sites with low-cost labor environments. Escalating labor costs in China — where costs have doubled in the last 10 years — are a big reason more companies are re-evaluating their location choices. However, where low-cost labor is a determining factor, the U.S. reshoring impact is minimal. Typically, the choice is made to re-locate a facility to another low-cost labor environment, like Thailand or Vietnam.
Alternatively, if a company requires skilled labor and proximity to technically minded engineers, higher costs are palatable, to ensure access to the talent required for high-tech manufacturing success.
For other companies, it’s the proximity to the end customer that matters most. These investments have generally never left the U.S. What are the cost advantages offered by moving closer? The growth of e-commerce has put more pressure on supply chains, and speed is increasingly a competitive advantage in some sectors. The proximity of a manufacturing facility to distribution centers or end customers can have a dramatic impact on site selection strategy.
Where low-cost labor is a determining factor, the U.S. reshoring impact is minimal. Typically, the choice is made to re-locate a facility to another low-cost labor environment, like Thailand or Vietnam.
Regardless of the driving forces, relocating a facility is a major expense and involves significant risk. Trade-offs between financial and non-financial risks will need to be made. As investments start to come back into U.S., more companies are thinking through the long-term goals of training a sustainable supply of labor, and how they will continue to maintain a productive workforce as technology continues to evolve the manufacturing process.
The real impact of reshoring to the U.S. remains to be seen and will play out in coming years. Significant facility investments are already in progress, so we expect some headlines touting jobs returning to America. But is this a true manufacturing renaissance? Certainly, for some communities. But for the nation as a whole, only time — and ultimately, corporate location decisions — will tell.