Editor's Picks
Why Cold Storage May Defy the Tariff Crunch
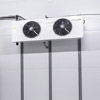
Food related projects remain resilient as tariff pressures shake other sectors of commercial real estate
Large-Scale Projects Face Financing Challenges
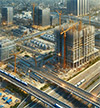
Executives have been forced to find new ways to finance projects.
The Location Economics of Advanced Nuclear
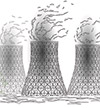
Technology gains traction as a strategic investment, with evolving reactor designs, streamlined site selection, and regional incentives shaping the future of clean, reliable power.
The Battle to Break China’s Rare Earth Supply Chain Dominance
U.S. faces challenges in reducing reliance on China for rare earths.
Recent Features
Skilled Labor / STEM
What We’re Getting Wrong About Gen Z’s Future in the Skilled Trades
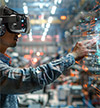
Employers must modernize their training programs if they want to attract and retain the next generation.
ContinueContributed Content
How Virginia Minimizes Risk for New Facilities
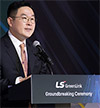
How shovel-ready sites and talent programs are helping Virginia win major manufacturing projects.
ContinueLogistics / Infrastructure
Optimizing Your Rail-Served Transportation Network: Strategy Before Steel
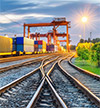
Infrastructure can power your supply chain—but only when planned with foresight.
ContinueBusiness Globalization
Reshoring Reality Check from Construction
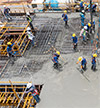
How tariffs and economic incentives are influencing FDI and location decisions.
ContinueManufacturing / Industrial
U.S. Textile Manufacturers are Building for the Future
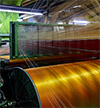
Automation and policy incentives could reshape the future of American textile production.
ContinueEnergy / Clean Tech
Energy Costs and Constraints Are Reshaping Site Selection in 2025
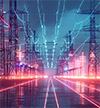
Surging energy demands, grid instability, and ESG pressures are changing how companies choose new facility locations.
ContinueGovernment Policy / Business Climate
Manufacturing’s New Risk Game for Site Selection
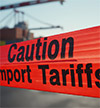
Companies face growing challenges as tariffs, political shifts, and trade policies disrupt location strategies.
ContinueContributed Content
All Roads Lead to Kansas: Logistics and Distribution Thrive at the Center
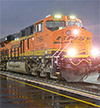
Location, logistics parks, and workforce are a dominant force in this state’s distribution strategy.
ContinueContributed Content
Michigan Resilience: Global Infrastructure and Smart Investments Power Future Supply Chains
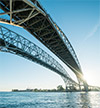
Michigan upgrades ports, invests in tech, and links talent to global trade for smarter, resilient supply chains.
ContinueContributed Content
Anduril Industries to Build Historic Arsenal-1 Defense Manufacturing Hub in Ohio
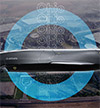
The state cements its role in defense innovation with a transformative investment in autonomous weapons manufacturing.
ContinueContributed Content
Assessing Risk Assessment
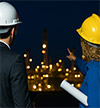
Companies are looking beyond cost and factoring in culture, politics, and community fit for resilience.
ContinueLogistics / Infrastructure
The Quest for Logistics Supremacy
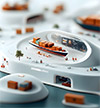
With supply chain pressures mounting, America’s logistics network is being rebuilt from the ground up and states are competing for the infrastructure edge by investing in ports, air cargo, and cold storage.
ContinueData Centers
First Person: Joe Capes, CEO, LiquidStack
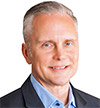
LiquidStack CEO Joe Capes on choosing Texas for expansion, working through AI supply chain shocks, and why hot water is the future of cooling.
ContinueTaxes / Incentives
The Legal Limits of DEI in Incentives Agreements, Hiring, and Contracting
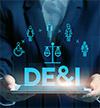
States and cities have tied incentives to diversity, equity, and inclusion (DEI) goals — such as subcontracting targets or workforce composition — but a new executive order from the Trump administration and related lawsuits are raising the legal stakes. That raises new questions about what’s lawful and what’s not when it comes to DEI, affirmative action, and the use of contracting targets — and how that may impact your next location decision.
ContinueTaxes / Incentives
What You Need to Know About NMTCs
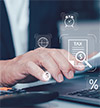
New market tax credits offer millions in upfront funding for projects that create jobs and serve underserved communities.
ContinueEnergy / Clean Tech
Powering the Next Generation of Projects
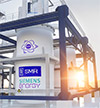
Small modular reactors could help meet surging demand for energy in manufacturing and data centers.
ContinueDCs / Warehousing
Rewriting the Rules of Warehouse ROI
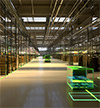
Embedding automation into leases may offer companies a smarter way to balance risk, cost and productivity.
ContinueData Centers
Data Center Demand Stabilizes Amid Changing Market Forces
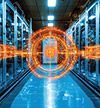
Pre-leasing slows, location criteria evolve, and real estate tax structures face pressure from leaner buildouts.
ContinueBusiness Globalization
Tariffs, Talent, and U.S. Expansion
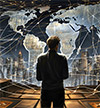
International executives reveal what’s driving their U.S. site decisions amid policy changes and workforce pressure
ContinueGovernment Policy / Business Climate
Last Word: Time for States to Shine
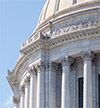
With federal action slowing and market forces accelerating, private firms are finding that the most effective policy responses—on issues like energy, housing, and workforce—are coming from state and local governments with the agility to act.
ContinueBusiness Globalization
The New Math Behind Mexico and U.S. Manufacturing Decisions
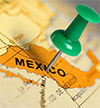
Rising wages, grid strain, and policy shifts are changing the calculus for manufacturers in North America.
ContinueManufacturing / Industrial
How to Choose the Right Site for Your Factory in 2025’s Volatile Landscape
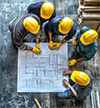
Why manufacturers should treat site selection as a form of risk management — not just opportunity hunting.
ContinueManufacturing / Industrial
Rebuilding the Industrial Base Requires a Commitment to Ecosystem Formation
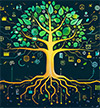
A return to American manufacturing demands more than factories — it requires coordinated, community-wide ecosystem development
ContinueAdvanced Manufacturing
In Focus: AI Is Changing Incentives Math
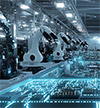
Headcount-focused incentives punish evolving companies, payroll helps reward a different kind of growth.
ContinueData Centers
First Person: David Robey, Co-CEO of QTS Data Centers
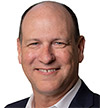
With QTS rapidly scaling to meet hyperscaler and enterprise demand across North America and Europe, Co-CEO David Robey shares his perspective on site selection, utilities, incentives, and what’s next for the industry. Robey, who previously served as COO, brings a tactical mindset to an evolving set of location priorities.
ContinueBiotech / Life Sciences
How Innovation and Investment Are Reshaping Life Sciences in 2025
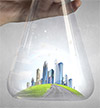
Talent shortages, financing volatility, and supply chain shifts define the life sciences outlook.
ContinueBiotech / Life Sciences
What It Takes to Power the Next Generation of Biomanufacturing
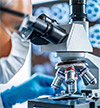
Flexible utilities and workforce pipelines are essential to meet growing life sciences manufacturing demand.
ContinueData Centers
New Rules for the Cloud Rush

What developers need to know about how states are regulating data centers—and utilities are shifting the cost burden.
ContinueBiotech / Life Sciences
Rethinking Life Sciences Site Selection in a Resilient and Dynamic Market
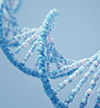
Planning new facilities now requires deeper segmentation, faster timelines, and more nuanced incentive approaches.
ContinueConstruction / Project Planning
Scaling Up Without Falling Short
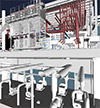
Scaling a pilot into full production requires smart planning, the right team, and constant flexibility.
ContinueProject Announcements
France-Based Cailabs US Plans Arlington County, Virginia, Headquarters Operations
08/21/2025
AVAIO Digital Plans Brandon, Mississippi, Data Centers Operations
08/21/2025
Schütz Container Systems Establishes Kenosha, Wisconsin, Production Operations
08/21/2025
GE Vernova Expands Charleroi, Pennsylvania, Operations
08/18/2025
Busch Vacuum Solutions Plans Tempe, Arizona, Operations
08/18/2025
Made Scientific Establishes Princeton, New Jersey, Manufacturing-Headquarters Operations
08/18/2025
Comcast Establishes West Palm Beach, Florida, Operations
08/17/2025
Most Read
-
Tariffs, Talent, and U.S. Expansion
Q3 2025
-
What We’re Getting Wrong About Gen Z’s Future in the Skilled Trades
Q3 2025
-
A New Course for U.S. Shipbuilding
Q3 2025
-
Optimizing Your Rail-Served Transportation Network: Strategy Before Steel
Q2 2025
-
In Focus: AI Is Changing Incentives Math
Q2 2025
-
Rewriting the Rules of Warehouse ROI
Q3 2025
-
How to Choose the Right Site for Your Factory in 2025’s Volatile Landscape
Q2 2025